AUTOMATYKA I ROBOTYKA
Trendy na 2025 rok
Misją firmy Raion jest uwalnianie potencjału ludzkiego, co silnie koreluje z rozwojem społecznym i gospodarczym. Ludzkość dąży do tego, by człowiek był coraz mniej obciążony pracą manualną, a co za tym idzie – w ogóle mniej pracował. Dużo się mówi ostatnio o czterodniowym tygodniu pracy czy siedmiogodzinnym dniu pracy. To, że takie rozmowy w ogóle się odbywają, w dużej mierze jest zasługą automatyzacji i robotyzacji! – mówi Mateusz Bąk, prezes firm Raion Software i Raion Automatyka.
Data publikacji: 25.11.2024
Data aktualizacji: 15.01.2025
Podziel się:
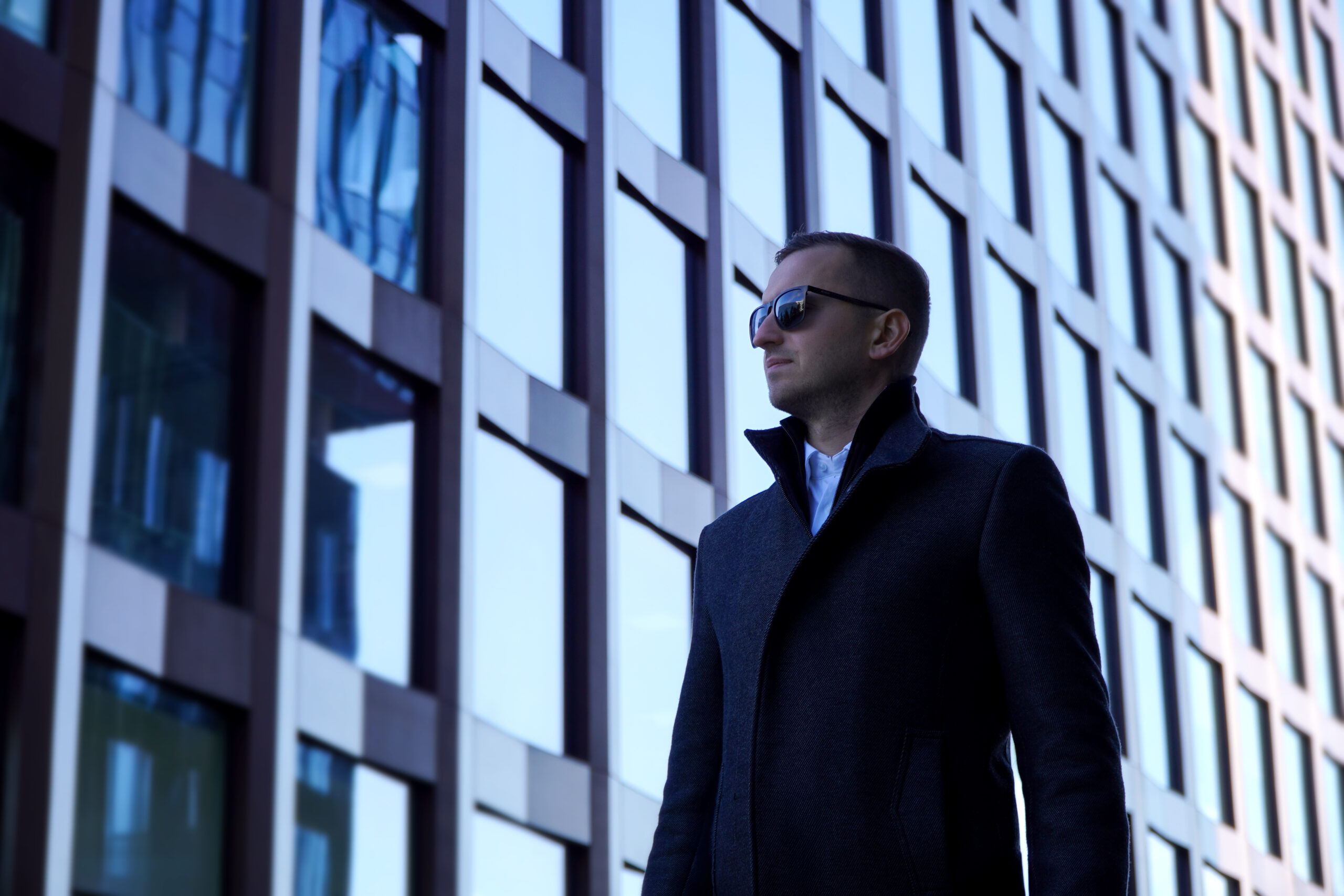
Przemysław Ozga: Rok 2024 przebiega w światowym przemyśle pod hasłami deglobalizacji i reindustrializacji. Przemysł przygląda się i rozważa relokacje, skracając łańcuchy dostaw, oraz planuje inwestycje w opłacalne technologie – wszystko, by pozostać konkurencyjnym. Co będzie według ciebie główną troską dla firm produkcyjnych w 2025 r.: uporządkowane dane, deficyt zasobów, zarządzanie kosztami, agregacja kompetencji, a może zielony przemysł lub wciąż chwiejny popyt?
Mateusz Bąk, prezes Raion Software: Reindustrializacja i relokacja produkcji m.in. do Europy to tendencje, które widzimy już od kilku lat. Dla nas, jako Raion, jest to korzystne zjawisko. Europejska produkcja jest mocno oparta na robotyce i technologii, ma odmienną specyfikę od przemysłu z Dalekiego Wschodu. Fabryka, która zatrudniała trzysta osób w Chinach, po relokacji do Niemiec liczy już trzydzieści osób. W 2023 r. podczas jednego spotkania biznesowego w Stanach Zjednoczonych usłyszałem o odradzaniu się tamtejszego przemysłu z chęcią uniezależniania się od Chin. Do niedawna produkcja w Azji była tak tania, że nie opłacało się produkować w Ameryce. Obecnie, z uwagi na uwarunkowania geopolityczne i kwestie bezpieczeństwa, koszty nie są już kluczowym aspektem, jeśli chodzi o lokalizację produkcji, ponieważ mamy różne scenariusze przyszłości. Jeśli chodzi o troski w 2025 r., jestem przekonany, że tematem numer jeden będzie wysoko wykwalifikowana kadra. Wciąż zastępujemy osoby o niskich kompetencjach maszynami i robotami, a potrzebujemy każdej niemal liczby automatyków, mechaników, inżynierów. Wymaga to mądrej edukacji inżynierów, np. takiej, jak mają Niemcy, które przygotowują ekspertów od początku ich szkolnej nauki. W Polsce idziemy w dobrym kierunku, potrzebujemy jednak jeszcze trochę czasu. Drugim z wyzwań będą rozporządzenia Unii Europejskiej dotyczące „zielonego przemysłu”. Dużo firm produkcyjnych pyta nas o minimalizację śladu węglowego, zarządzanie odpadami, odnawialne źródła energii, ponieważ normy środowiskowe są coraz bardziej wymagające, a koszt dostosowania się do nich, niestety, w większości ciąży na sektorze przemysłowym. Trzecim wyzwaniem będą dalsze zawirowania geopolityczne, np. konflikt za wschodnią granicą, którego rezultatem jest chwiejny popyt wywołany embargami, zakazami i sankcjami. Turbulencje z łańcuchami dostaw spowodowane pandemią wróciły już do normy i oby tak zostało! Ostatnim wyzwaniem na 2025 r. są rosnące wyzwania w zakresie analityki danych. Firmy stawiają coraz większy nacisk na systemy BI, sztucznej inteligencji, raportowania. Obecnie wartością nie są już tylko maszyny i inne dobra fizyczne, ale przede wszystkim dane potrzebne do podejmowania trafnych decyzji.
P.O.: Dane i informacja, o których wspomniałeś, wymagają odpowiednich kwalifikacji i technologii. Co będzie „wiatrem w żaglach” przemysłu w 2025 r., jeśli chodzi o te drugie? Które technologie zadecydują o przewadze konkurencyjnej w najbliższych miesiącach? Możemy pokusić się o np. wskazanie lidera 2025 r.?
M.B.: Wyznacznikiem w 2025 r. będzie umiejętność agregowania danych lokalnych, dzięki technologiom przemysłu 4.0 i Internetowi rzeczy (IoT). Teraz możliwe jest uczynienie produkcji bardzo przejrzystą, połączenie się z maszynami za pomocą różnych czujników i monitorowanie wydajności i jakości procesów, dzięki czemu otrzymujesz wiele danych. Ale same dane są niczym w porównaniu z wnioskami, jakie można z nich wyciągnąć. Dlatego bardzo ważne jest prawidłowe zbieranie danych, po drugie, gromadzenie ich w jednym systemie, a po trzecie, sporządzanie odpowiednich raportów i podejmowanie na ich podstawie decyzji zarządczych. Silną, cały czas rozwijającą się tendencją jest automatyzacja, nie zapominajmy o tym. Wiele firm w Polsce, ale nie tylko, jest nadal oparta na zasobach ludzkich i ręcznej pracy. Cieszy mnie, że coraz więcej firm z polskim kapitałem inwestuje – niekiedy miliony – w automatyzację, i nie dotyczy to już jedynie wielkich globalnych korporacji. Przykładem jest np. polska branża meblarska, w której jesteśmy światowym potentatem. Ważnym tematem w 2025 r. będzie naturalnie sztuczna inteligencja. Już od lat sztuczna inteligencja jako uczenie maszynowe czy algorytmy w systemach wizyjnych była wykorzystywana w procesie kontroli jakości czy predykcji awarii. Obecnie wchodzimy z tą technologią szerzej w obszary analityki danych, wyciągania wniosków, przewidywania tendencji, dając jej bardziej całościowy charakter.
P.O.: Sztuczna inteligencja została ogłaszana wynalazkiem na miarę druku. Jak jej algorytmy wpisują się w oferowane przez was systemy? Czy sztuczna inteligencja to bardziej bajka, czy rzeczywista rewolucja dla przemysłu?
M.B.: AI będzie rewolucją w przemyśle – to coś, co docelowo wejdzie w kanony standardów i będziemy jej używać podobnie jak druku czy samolotów. Pamiętajmy jednak, że przemysł rządzi się swoimi prawami i rzeczywistość produkcyjna to także rygorystyczne normy i certyfikaty, przez co zmiany mają swoje tempo i dynamikę. AI może być wdrażana po głębokiej analizie stabilności i bezpieczeństwa procesów i danych. Drugim obszarem, w którym wykorzystamy AI w najbliższym czasie, jest obszar tworzenia oprogramowania – dzięki już dostępnym i cały czas rozwijanym narzędziom zespoły są coraz wydajniejsze i podejmują się coraz trudniejszych zagadnień. Skoro rozmawiamy o sztucznej inteligencji, przypomniała mi się wypowiedź jednego ze szkoleniowców z tej dziedziny podczas warsztatów dotyczących AI w Raion, który powiedział, że dzisiejsza sztuczna inteligencja, jest na poziomie „papugi” – analizuje i odtwarza dane na zewnątrz, jak papuga, która powtarza, ale nie do końca rozumie, co mówi. To, do czego dążą dzisiaj twórcy modeli AI, to poziom „kruka”, na którym to poziomie zachodzą wstępne wnioski przejawiające się w jego proaktywnej postawie. Podobno jest to perspektywa kilku lat. Jak to usłyszałem, przypomniała mi się wypowiedź jednego z moich wykładowców na Politechnice Poznańskiej, który podczas zajęć z sieci neuronowych powiedział, że ówczesna sztuczna inteligencja była na poziomie „pająka”. Jak widać, cały czas idziemy do przodu. Nasza mapa drogowa w Raion jest również silnie skorelowana ze sztuczną inteligencją i 2025 r. będzie przełomowy dla nas pod tym kątem. Już się nie mogę doczekać.
P.O.: Czy wszystkie systemy IT będą ostatecznie migrować do chmury obliczeniowej? Jakie są „za” i „przeciw” posiadania systemów w chmurze?
M.B.: Dane statystyczne pokazują, że stosunek danych trzymanych w chmurze rośnie w porównaniu z rozwiązaniami lokalnymi i według mnie ta tendencja utrzyma się jeszcze przez wiele lat. Wdrożenia chmurowe mają dużo niższe koszty początkowe, są dużo szybsze i łatwiejsze. Kontruje nam tutaj tematyka cyberbezpieczeństwa. Firmy kładą coraz większy nacisk na bezpieczeństwo danych, co często powoduje, że mimo większych kosztów decydują się na utrzymywanie własnej infrastruktury IT. Co ciekawe, zabezpieczenia IT takie jak VPN czy SSL, są tak silne i dopracowane, że środowiska chmurowe są bardzo bezpieczne, więc problem tkwi w człowieku – najsłabszym ogniwie ochrony danych. Musimy również pamiętać o problemie samej lokalizacji serwerów. Przy decydowaniu się na rozwiązania chmurowe warto się upewnić, że serwery znajdują się w bezpiecznych strategicznie lokalizacjach. Jeżeli producent z Polski przesyła swoje dane np. do chmury w Chinach czy na Tajwanie, to przy zawirowaniach geopolitycznych firma może zostać odcięta od danych i informacji, co będzie oznaczało kompletny paraliż jej funkcjonowania.
P.O.: Inteligentne fabryki wymagają wielopoziomowej integracji, m.in. warstw IT i OT. Jak wygląda orkiestracja nowych systemów, np. MES, z istniejącymi systemami ERP oraz wspomnianych warstw – czy dane przesyłane w górę i w dół mają charakter symetryczny (jest ich podobna ilość)?
M.B.: Integracja danych między warstwami IT oraz OT jest dzisiaj absolutną podstawą wdrożeń systemów efektywnie wspierających produkcję. Już nieraz spotkałem się z systemami, które miały zarządzać produkcją, ale nie miały żadnej integracji z warstwą fizyczną. Powodowało to w najlepszym wypadku bardzo duże opóźnienia w dostarczaniu danych deklaratywnych, a ostatecznie najczęściej były one po prostu nieprawdziwe. Mówiąc o wymianach na linii IT–IT, czyli o dialogu czysto software’owym, widzimy pozytywną tendencję, w której coraz więcej systemów ze swojej specjalizacji, przeznaczonych dla konkretnego obszaru, ma ustandaryzowane „uchwyty”, czyli dane wejściowe i wyjściowe, co bardzo ułatwia integrację.
P.O.: Z punktu widzenia szefa produkcji lub dyrektora zakładu produkcyjnego – jak zmienił się system MES w ostatnich dziesięciu, piętnastu latach? Jakie nowe funkcje pomagają im w ich codziennej niełatwej pracy?
W ciągu ostatnich lat zaszły ogromne zmiany w systemach MES, które znacznie ułatwiły pracę w produkcji. Przede wszystkim dzięki integracji z innymi systemami, jak ERP. Wszystkie dane o zamówieniach czy zasobach przepływają automatycznie, co oszczędza czas i zmniejsza ryzyko wystąpienia błędów. Dużą rewolucją jest komunikacja z parkiem maszynowym (IoT). Maszyny są teraz podłączone do sieci i na bieżąco wysyłają dane o swoim stanie technicznym, wydajności, obecnie realizowanym produkcie. Dawniej systemy pracowały w trybie offline – wszystkie informacje były deklarowane przez operatorów. Osoba zarządzająca produkcją ma teraz wszystkie informacje podawane w czasie rzeczywistym, zachowując przy tym pewność rzetelności danych. Bardzo ważną rzeczą jest też możliwość monitorowania produkcji zdalnie – szef produkcji może kontrolować procesy nawet z telefonu, co daje ogromną elastyczność.
P.O.: Wspomniałeś wcześniej o niemieckiej edukacji. Firmy o zautomatyzowanych procesach produkcyjnych są często dużo atrakcyjniejsze i skuteczniejsze w przyciąganiu talentów. Ponadto automatyka uwalnia kurczące się demograficznie zasoby ludzkie. Jakie największe szanse i bariery widzisz w implementacji automatyki i robotyki w polskich zakładach produkcyjnych?
M.B.: Dzisiaj główną barierą dla polskich przedsiębiorstw są przede wszystkim wysokie koszty początkowe takich inwestycji. W wypadku firm o własnym kapitale inwestycyjnym zrozumiałe jest oczekiwanie szybkiego zwrotu z inwestycji, np. w pół roku lub rok. Niezbędne jest jednak spojrzenie w długiej perspektywie. Zaawansowane technologicznie firmy liczą ROI inwestycji w automatyzację w horyzoncie pięciu, a nawet siedmiu lat. Drugą przeszkodą jest niezrozumienie technologii, deficyt doświadczenia. Człowiek z natury boi się tego, czego nie zna. Pracując z różnymi firmami, widzę ogromną różnicę w świadomości przy pierwszym, a np. przy dziesiątym wdrożeniu stacji zrobotyzowanej. Dlatego mocno wspieram każdy rodzaj szerzenia informacji o automatyzacji i robotyzacji. Co się często dzieje, np. wraz z migracją menedżerów między firmami. Wraz z nimi migrują również wiedza i dobre praktyki na temat automatyzacji.
P.O.: Czy jak już sfinansuję i zainstaluję MES i roboty w dwóch różnych fabrykach, czy mogą one komunikować się ze sobą, wymieniać informację np. o awariach lub o optymalizacjach procesowych?
M.B.: Prowadzimy wdrożenia u klientów mających kilka, a nawet kilkanaście fabryk rozproszonych na całym świecie. Dane z nich są agregowane w wielkich hurtowniach danych i tam porównywane pod kątem poszczególnych działów czy całych fabryk.
P.O.: Wspomniałeś wcześniej o uczeniu maszynowym. Jak bardzo popularne są dzisiaj uczenie maszynowe oraz systemy wizyjne? Czy i jak te technologie wpływają na optymalizację kosztów (usprawnienie procesu) lub np. spadek zużycia energii w procesach?
M.B.: Uczenie maszynowe i systemy wizyjne są wykorzystywane w dużej mierze do zarządzania jakością. Algorytm przez systemy wizyjne uczy się „dobrego detalu”, odróżniając właściwy produkt od niewłaściwego. Jest to zakres mocno wyspecjalizowanych branż, więc nie jest to technologia używana na szeroką gospodarczo skalę. W dalszym ciągu to branża automotive wyznacza kierunki rozwoju w dziedzinie automatyki i tam najczęściej spotykamy tego typu rozwiązania. Pozostałe sektory jednak nadgoniły w ostatnich latach ten dystans, zmniejszając tę dysproporcję w poziomie zaawansowania technologicznego.
P.O.: Czy robotyzacja sprzyja idei zrównoważonego rozwoju i gospodarce o obiegu zamkniętym? Możemy wyobrazić sobie robota wyprodukowanego i działającego z użyciem odnawialnych źródeł energii?
M.B.: Myślę, że robotyzacja bardzo sprzyja idei zrównoważonego rozwoju. Misją firmy Raion jest uwalnianie potencjału ludzkiego, co silnie koreluje z rozwojem społecznym i gospodarczym. Ludzkość dąży do tego, by człowiek był coraz mniej obciążony pracą manualną, a co za tym idzie – w ogóle mniej pracował. Dużo się mówi ostatnio o czterodniowym tygodniu pracy czy siedmiogodzinnym dniu pracy. To, że takie rozmowy w ogóle się odbywają, w dużej mierze jest zasługą automatyzacji i robotyzacji! A czy robotyzacja sprzyja ochronie środowiska i gospodarce o obiegu zamkniętym? Na pewno nie przeszkadza.
P.O.: Zajmujecie się również budową maszyn na specjalne zamówienie firmy produkcyjnej. Jak wygląda i ile trwa taki projekt? Jak wygląda certyfikacja i testowanie go w warunkach całkowitej unikatowości waszego produktu?
M.B.: Budowanie prototypów jest bardzo złożonym procesem. Nasi inżynierowie wykonują całą pracę, zaczynając od koncepcji, przez projekt, następnie budowę prototypu, aż po wdrożenie produkcyjne. Wymaga to bardzo wysokich kompetencji i doświadczenia już od pierwszych etapów projektu, aby eliminować potencjalne problemy, które mogą wystąpić na końcu procesu budowy maszyny. Oczywiście Raion ma w swoim portfolio też sporo standardowych maszyn, które wraz z każdą kolejną wersją są ulepszane i usprawniane, dążąc do najwyższej jakości produktu dla klienta. Czas budowy maszyny jest mocno zdeterminowany skalą i poziomem jej skomplikowania. Budowa zaawansowanej i skomplikowanej
maszyny na indywidualne zamówienie może trwać ponad dwanaście miesięcy, są też projekty indywidualne, które realizujemy w cztery miesiące, a np. standardowe stanowiska do paletyzacji jesteśmy w stanie dostarczyć już w dwa miesiące. Certyfikacja i testowanie maszyn zaczynają się już na początku projektu, gdy nasi inżynierowie projektują każdy element zgodnie z normami dotyczącymi budowy i bezpieczeństwa maszyn. Jest to ogrom wiedzy, który trzeba mieć, aby zrobić to dobrze. Dopiero po zakończeniu projektu maszyna przechodzi certyfikację, która weryfikuje zgodność z normami oraz ogólne bezpieczeństwo maszyny.
P.O.: Czy korzystacie z cyfrowych bliźniaków przy projektowaniu i testowaniu tego typu niestandardowych rozwiązań?
M.B.: Oczywiście, wykorzystujemy tego typu technologię przy projektowaniu maszyn i urządzeń. Co prawda nie robimy tego przy każdym projekcie, ponieważ nie zawsze jest taka potrzeba. Jednakże w wypadku przedsięwzięć, w których mamy do czynienia np. z wysoką wydajnością procesu lub wyzwanie stanowią inne warunki czy wymagania aplikacji, wspomagamy się różnego rodzaju środowiskami do symulacji cyfrowej zaprojektowanych urządzeń i (lub) procesów. Tego typu technologię wykorzystujemy bardzo często w projektowaniu stanowisk zrobotyzowanych. Przeprowadzenie takich symulacji na etapie projektu daje ogromne korzyści, jesteśmy w stanie przeanalizować i wychwycić potencjalne problemy lub błędy już na tak wczesnym etapie, co pozwala zaoszczędzić ogrom czasu oraz kosztów. Dodatkowo, dysponując takim cyfrowym bliźniakiem, programowanie sterowników PLC czy robotów w offline, jeszcze przed fizycznym zbudowaniem i powstaniem maszyny jest znacznie uproszczone lub wręcz możliwe, co wpływa na skrócenie czasu dostawy funkcjonującego rozwiązania do klienta. Nie wspominając o symulacjach wydajności czy analizie wąskich gardeł.
P.O.: Wspomniałeś o uwalnianiu, dzięki automatyzacji, potencjału kreatywności ludzi. Czy zauważacie wynikające z inwestycji w roboty rzeczywiste wzmocnienie kultur organizacyjnych, np. automatyczny rozwój kompetencji ludzkich?
M.B.: Nierzadko, gdy uruchamiamy proces w fabryce, ludzie boją się utraty pracy. Patrząc na nasze realizacje, widzimy, że częstym warunkiem inwestycji w automatyzację jest zwiększenie mocy produkcyjnych, jakości produkcji lub poprawa bezpieczeństwa i ergonomii pracy, a nie redukcja kadr. Osoby wykonujące dotychczas prace manualne są przekwalifikowane i przenoszone do procesów o innym charakterze, dzięki czemu firma się rozwija. Przykładowo ostatnio wdrożyliśmy robota paletyzującego, który zwiększył wydajność procesu oraz pozwolił układać wyżej opakowania
na palecie tak, by maksymalnie wykorzystać miejsce w samochodzie ciężarowym w transporcie. A pracownica zamiast pracy fizycznej przy układaniu palet po przeszkoleniu została operatorem robota, jednocześnie obsługując inne maszyny produkcyjne na linii. Nie spotkałem się z sytuacją, żeby kogoś zwolniono po wdrożeniu robota lub nowej maszyny.
P.O.: Dziękuję za rozmowę.
M.B.: Dziękuję.
Zobacz również