AUTOMATYKA I ROBOTYKA
Skutki pracy z nieodpowiednio dobranym manipulatorem
Dobór odpowiedniego manipulatora przemysłowego to klucz do poprawy efektywności i ergonomii pracy. Dobrze zaprojektowane urządzenie przekłada się na realne oszczędności i zadowolenie operatorów. Co jednak, jeśli urządzenie nie odpowiada rzeczywistym potrzebom zakładu? Niestety, błędny wybór manipulatora może przynieść wiele problemów zarówno technicznych, jak i organizacyjnych. Sprawdź, skąd biorą się takie sytuacje i jak ich uniknąć.
Data publikacji: 25.06.2025
Data aktualizacji: 26.06.2025
Podziel się:
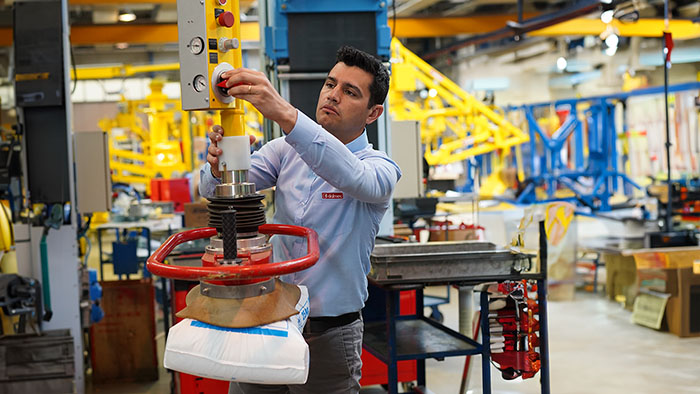
Dlaczego manipulator może być źle dopasowany?
Profesjonalni producenci projektują manipulatory pod konkretne zadania i środowiska pracy. To właśnie producent powinien odpowiednio rozpoznać potrzeby klienta i na tej podstawie stworzyć spersonalizowane rozwiązanie odpowiadające na wyzwania związane na przykład ze środowiskiem pracy czy przenoszonym produktem.
Problem pojawia się wtedy, gdy zamiast indywidualnego projektu, oferowane są gotowe urządzenia „z półki”. W takich przypadkach to zakład musi dostosować proces do możliwości manipulatora. To zaś czasami okazuje się po prostu niemożliwe. Ustandaryzowane manipulatory nie są w stanie poradzić sobie w każdej sytuacji, a firma z kolei niekoniecznie może być gotowa do tego, by pod sprzęt wywrócić swój proces do góry nogami. Oznacza to, że to właśnie brak indywidualnego podejścia ze strony producenta jest najczęstszą przyczyną nietrafionych inwestycji.
Co może pójść nie tak przy wyborze gotowego rozwiązania?
Stosowanie uniwersalnych manipulatorów niesie ze sobą szereg potencjalnych trudności:
- nieodpowiednia konstrukcja urządzenia – np. próba realizacji zadań wymagających stabilności za pomocą manipulatorów linkowych zamiast ramion sztywnych skutkuje pogorszeniem ergonomii i precyzji.
- zbyt uproszczone rozwiązania – manipulatory wyposażone jedynie w hak często nie posiadają odpowiednio dobranego chwytaka, co stanowi zagrożenie dla bezpieczeństwa pracy i produktów.
- źle zaprojektowany chwytak – zwiększa ryzyko upuszczenia lub uszkodzenia ładunku, a także wydłuża czas cyklu, co wpływa na wydajność.
- niewygodne rozmieszczenie uchwytów i sterowania – może wymagać od operatora niewygodnych ruchów, takich jak schylanie się czy unoszenie rąk ponad głowę.
- brak dostosowania do warunków w zakładzie – urządzenie może nie współgrać z infrastrukturą hali, powodując kolizje z maszynami, oświetleniem czy wentylacją.
Inne przyczyny niewłaściwego dopasowania
Czasem problemy wynikają nie tylko z gotowych rozwiązań, ale i z błędów na etapie specyfikacji. Przykładem jest przewymiarowanie manipulatora, czyli zaprojektowanie go do przenoszenia ciężarów, które występują rzadko. Jeśli większość ładunków waży do 100 kg, a urządzenie przystosowano do 300 kg, to jego obsługa staje się niepraktyczna i uciążliwa. Taki sprzęt bywa cięższy niż przenoszony towar, co drastycznie obniża komfort pracy. Doświadczony producent powinien odradzić takie rozwiązanie.
Kolejnym problemem jest chęć zastosowania jednego manipulatora do różnych, niepowiązanych produktów. Choć technicznie możliwe, w praktyce prowadzi to do tworzenia urządzeń przeładowanych funkcjami, z których realnie na co dzień się nie korzysta: wymiennymi chwytakami, dodatkowymi czujnikami czy skomplikowanym sterowaniem. Efekt? Operatorzy unikają pracy z takim sprzętem, a proces traci na płynności.
Ile może kosztować źle dobrane urządzenie?
Nieodpowiednio dopasowany manipulator to nie tylko frustracja pracowników. To również realne straty: uszkodzone produkty, kontuzje, spowolnienie pracy, a w skrajnych przypadkach całkowite zaniechanie używania urządzenia. Pracownicy wracają wtedy do ręcznej obsługi, narażając się na przeciążenia i urazy. Firma natomiast ponosi dodatkowe koszty: nie tylko operacyjne, ale i inwestycyjne, jeśli konieczny okaże się zakup kolejnego urządzenia. Paradoksalnie więc „tańsze” rozwiązanie staje się najdroższą opcją.
Dlatego też Dalmec Polska stawia na indywidualne podejście. Manipulatory są projektowane pod konkretne potrzeby i środowiska pracy, dzięki czemu zapewniają pełne bezpieczeństwo, wygodę użytkowania i wysoką efektywność. Chcesz dowiedzieć się, jak rozwiązanie szyte na miarę może pomóc w optymalizacji procesu? Skontaktuj się z ekspertami Dalmec Polska i okryj nowy wymiar transportu bliskiego!
Zobacz również