INTELIGENTNE TECHNOLOGIE
Najczęstsze błędy w planowaniu produkcji i jak ich uniknąć
Od skutecznego planowania produkcji zależy to, czy uda się wyprodukować tyle, żeby finalnie zaspokoić potrzeby klientów. Warto więc dobrze się do tego przygotować. W artykule przedstawiamy sprawdzone strategie, które pomagają w opracowaniu solidnego planu produkcji. Zobacz!
Data publikacji: 11.03.2025
Data aktualizacji: 12.03.2025
Podziel się:
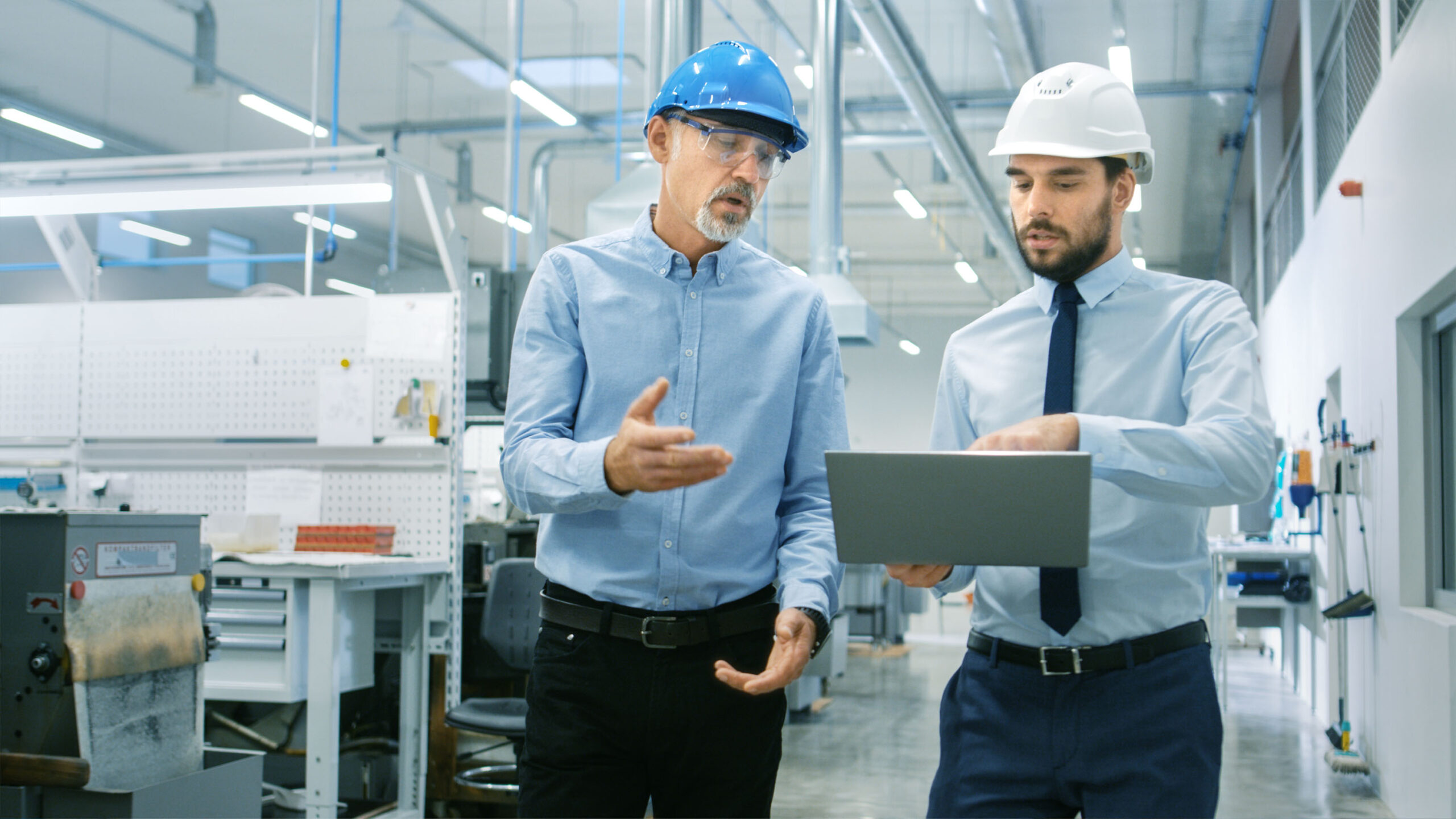
Główne błędy w planowaniu produkcji
Jeden z głównych błędów popełnianych podczas planowania produkcji polega na niewłaściwym oszacowaniu czasu potrzebnego na realizację poszczególnych zleceń. Zbyt powolny proces produkcji może prowadzić do sytuacji, w której firmie zaczyna brakować produktów potrzebnych do pokrycia bieżących zamówień.
Kolejny aspekt – zarządzanie zapasami. Niedoszacowanie poziomu surowców (w tym części, komponentów itd.) wymaganych do realizacji produkcji może prowadzić do przestojów na liniach produkcyjnych i wydłużać czas realizacji zamówień. Błędy tego rodzaju wynikają przeważnie z braku precyzyjnej kontroli nad przepływem towaru w firmie, czy niedostatecznej wiedzy o budowie produktów.
Zdarza się też, że osoby odpowiedzialne za planowanie produkcji nie potrafią określić, ile dokładnie wyrobów wytworzyć. Zazwyczaj kończy się to produkcją na oko. Choć intuicyjne planowanie może być zaletą, np. w firmach skupionych na masowym wytwarzaniu typu push, to przeważnie wyklucza profesjonalny tok produkcji i wpływa negatywnie na wyniki firmy.
Zmiany w trendach kształtują popyt, więc firma, która ich nie śledzi, może wyprodukować za dużo produktów. Kolejny błąd wiąże się więc z brakiem elastyczności i gotowości do wprowadzania w swoich planach wytwórczych korekt determinowanych przez zmiany na rynku.
Warto wspomnieć jeszcze o konieczności sprawnego zarządzania zasobami ludzkimi. Kadra zarządzająca produkcją powinna dysponować kompletnym wykazem kompetencji poszczególnych pracowników oraz stanowisk pracy (wiedzieć np. który spawacz ma zaawansowane umiejętności). Pozwala to już na etapie planowania produkcji, delegować do realizacji poszczególnych zleceń odpowiednie zasoby, co może znacząco wpłynąć na efektywność produkcji.
Skuteczne strategie unikania błędów w produkcji
Jak opracować solidny plan produkcji, aby zapewnić sprawny przebieg procesu wytwórczego?
Przede wszystkim należy regularnie monitorować rynek, śledzić zmiany popytu oraz szybko reagować na wszelkie odchylenia. Każda zmiana powinna znaleźć odbicie w przyjętym planie produkcji. Przykład? Jeśli prognozy przewidują, że w ciągu kolejnego kwartału wzrośnie zapotrzebowanie na artykuł X, to należy to uwzględnić w długoterminowym planie produkcji (poza bieżącymi zamówienia od klientów).
Równie ważna jest analiza zapotrzebowania na materiały. W tym celu warto wdrożyć system, który dostarcza wszystkich informacji potrzebnych do precyzyjnego wyliczania poziomu materiałów koniecznego do ukończenia produkcji. Nowoczesne systemy, poza aktualnym poziomem stanów magazynowych, uwzględniają ilości produktów, które firma planuje wytworzyć oraz ich struktury, tzw. BOM (opisują budowę produktów).
Dobra strategia produkcyjna uwzględnia również ciągły monitoring procesów wytwórczych. Dzięki stałemu nadzorowi można szybko reagować na wszelkie odchylenia od planu, co przekłada się ciągłą produkcję bez zbędnych przestojów.
System ERP podstawą skutecznego planowania produkcji
W kompleksowym zarządzaniu produkcją sprawdza się system ERP.
Przede wszystkim narzędzie wspiera proces planowania oraz harmonogramowania produkcji. Zaszyty w nim mechanizm umożliwia budowanie zintegrowanych planów produkcji złożonych z 2 poziomów: główny plan produkcji oraz plan potrzeb materiałowych. Ten pierwszy jest bardzo szczegółowy i uwzględnia konkretne ilości produktów. Z tego względu jest dobrą bazą wiedzy dla działów zaopatrzenia, które wykorzystują go do wyliczania ilości surowców niezbędnych do realizacji zleceń (plan potrzeb materiałowych).
Tak przygotowany harmonogram można w systemie ERP rozbudować o poziom sprzedaży i operacji (S&OP), który odbija aktualny popyt na produkty firmy. Za ten plan odpowiada z kolei dział sprzedaży (czasami marketingu).
Warto podkreślić, że choć dla każdego działu przewidziano osobne arkusze, to wszystkie posiłkują się danymi zaciąganymi z głównej bazy systemu. Użytkownicy znajdą w niej: listy BOM, historię sprzedaży, marszrut itd. W skrócie wszystko, czego potrzebują do tworzenia efektywnych planów produkcji.
Oprogramowanie ERP automatyzuje również proces harmonogramowania szczegółowego. Zaszyty w nim mechanizm dobiera do poszczególnych zleceń właściwe zasoby produkcyjne (maszyny, stanowiska, kooperantów itd.) najczęściej tak, aby minimalizować czas produkcji. W tym celu wykorzystuje szereg reguł oraz macierz kompetencji (słownik umiejętności zasobów).
Co poza tym?
System ERP umożliwia również monitorowanie każdego etapu produkcji. Meldunki zwrotne gwarantują szybki transfer informacji o przyczynach przestojów na hali (np. awariach). Ponieważ alert wyświetla się na panelu od razu po złożeniu meldunku, to planista może szybko reagować, przywracając produkcji normalny tok pracy.
Skuteczne planowanie produkcji - fundament nowoczesnej produkcji
Podsumowując, najczęstsze błędy w planowaniu produkcji to: niedoszacowanie czasu realizacji zleceń, brak strategii zarządzania zapasami i planowanie zasobów, a także brak gotowości do dynamicznego wprowadzania zmian w harmonogramach.
W tworzeniu skutecznych planów, które gwarantują płynny przebieg procesów produkcji, pomaga odpowiednia strategia zarządzania oraz systemy ERP.
Więcej o planowaniu produkcji z wykorzystaniem systemu ERP przeczytasz na stronie: https://www.streamsoft.pl/produkcja/planowanie-produkcji/
Źródło: Streamsoft
Zobacz również