INTELIGENTNE TECHNOLOGIE
MES i efektywność OEE - niewidzialna bariera wzrostu
Dostępność, wydajność, jakość. Jak mierzyć skuteczność wykorzystania dostępnych zasobów? Służą temu zaawansowane systemy teleinformatyczne. Ale technologia to jedno, kluczowe jest zaś to, co firma produkcyjna robi z danymi.
Data publikacji: 09.05.2025
Data aktualizacji: 09.05.2025
Podziel się:
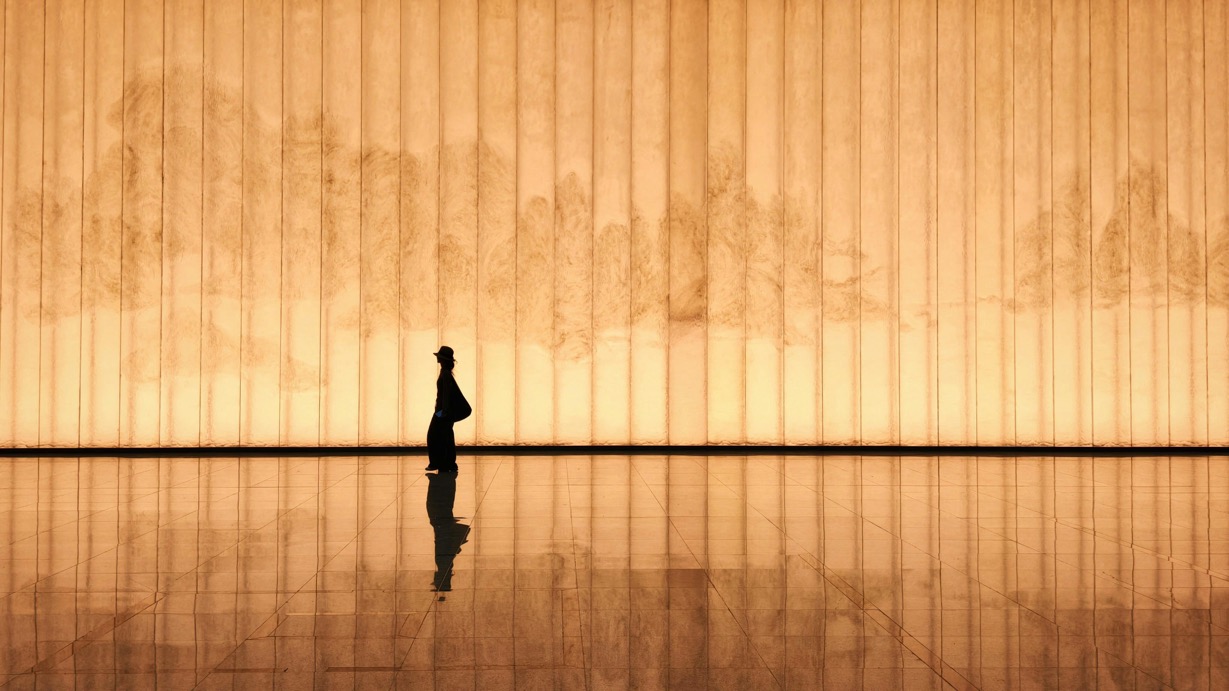
Overall equipment effectiveness (OEE) to jeden z podstawowych wskaźników KPI przedsiębiorstw produkcyjnych, używany do oceny efektywności funkcjonowania maszyn i urządzeń w procesie wytwórczym. Umożliwia pomiar skuteczności wykorzystania dostępnych zasobów produkcyjnych w danym czasie, uwzględniając trzy kluczowe składowe.
Ranking wskaźników
– Chodzi o dostępność (availability), mówiącą nam, jak długo maszyna była dostępna do pracy w porównaniu z zaplanowanym czasem – mówi Kamil Mostowy, kierownik projektów w firmie DSR. – Za spadek wartości tego wskaźnika może być odpowiedzialna awaria maszyny albo inny nieplanowany przestój. Wydajność (performance) określa, jak efektywnie maszyna pracuje w porównaniu z jej maksymalną wydajnością. Obniżenie tego parametru może wynikać z wolnego tempa produkcji, złych parametrów maszyny, zmniejszonej wydajności operatora. Z kolei jakość (quality) precyzuje, jaka część wyprodukowanych artykułów spełnia wymagania jakościowe.
Overall equipment effectiveness pomaga w identyfikacji i niwelowaniu strat w procesach wytwórczych, co przekłada się na oszczędności, lepszą kontrolę jakości oraz krótsze przestoje maszyn i urządzeń. Teoretycznie wskaźnik ten może przyjąć wartość od 0 proc. (brak efektywności) do 100 proc. (efektywność idealna). W praktyce OEE w okolicach 85 proc. i więcej oznacza bardzo dobry poziom wykorzystania maszyn, zaś spadek poniżej 60 proc. wskazuje na konieczność wprowadzenia zmiany poprawiającej efektywność pracy takiej maszyny.
Norma ISO 22400-2 opisuje standard dotyczący wskaźników wydajności produkcji. Jest częścią normy ISO 22400, która skupia się na wskaźnikach wydajności w przemyśle. Wskaźnik OEE pomaga w osiągnięciu celów zawierających się w normie ISO 22400-2. Koncentruje się na efektywności wyposażenia zakładów (maszyn i urządzeń).
Artykuł trafnie ukazuje znaczenie wskaźnika OEE w zarządzaniu produkcją oraz rolę systemów MES w monitorowaniu efektywności. W praktyce jednak największe wyzwanie nie leży w mierzeniu dostępności czy jakości – te dane najczęściej są rejestrowane automatycznie i bez większych trudności. Ilości wyprodukowanych jednostek są również dobrze raportowane. Problem pojawia się przy dokładnym określeniu normatywnych tack-timów (czyli owej „maksymalnej wydajności”) oraz budowie macierzy przezbrojeń, które pozwoliłyby na minimalizację planowanych niedostępności. To zadania wymagające głębszej analizy – możliwe do przeprowadzenia ręcznie lub z wykorzystaniem zaawansowanej analityki, której często brakuje w standardowych rozwiązaniach MES. Warto podkreślić, że tylko prawidłowe parametry wejściowe – takie jak rzeczywiste czasy cykli czy rzeczywiste czasy przezbrojeń – pozwalają na rzetelne i miarodajne obliczanie OEE, a co za tym idzie, na podejmowanie trafnych decyzji optymalizacyjnych. Dane dostarczane automatycznie do systemów MES stanowią świetną bazę wejściową do przeprowadzenia owej analityki i dokonania jednorazowych obliczeń pozwalających na poszukanie rzeczywistego, dodatkowo ukrytego, potencjału drzemiącego w naszym parku maszynowym – mówi Maciej Gniadek, Head of Managed Service, summ-it s.a.
Skąd brać dane do OEE?
W wypadku dużej zmienności planu produkcji to system MES dostarcza aktualnych danych o postępie realizacji zleceń produkcyjnych, stanie maszyn, opóźnieniach przepływu materiałów. Potencjalna obustronna wymiana informacji między systemami APS oraz MES daje efekt synergii w procesie zarządzania harmonogramem produkcji i reakcji na zakłócenia mające różne przyczyny. Polepsza także zarządzanie przepustowością maszyn przy dynamicznych zmianach w obszarze produkcji. Dostęp do informacji w czasie rzeczywistym umożliwia np. zmianę kolejki zleceń na danym zasobie, priorytetów zleceń czy przeniesienia realizacji na inną maszynę.
W zaawansowanych systemach klasy MES dane są dostępne w postaci dashboardów. Zaprojektowano je z myślą o monitorowaniu i zarządzaniu procesami produkcyjnymi z prezentacją danych w czasie rzeczywistym oraz z zachowaniem ergonomii użytkowania i możliwości szybkiego analizowania.
– Podpowiedź, jakie zmiany rekomendować w procesie produkcyjnym, aby osiągnąć jak najwyższy poziom OEE, zrealizowaliśmy w projekcie Production Management Smart Advisor – wyjaśnia Piotr Rojek, prezes firmy DSR. – Powstało narzędzie inteligentnej rekomendacji zmian w procesach produkcyjnych w celu ich optymalizacji, wykorzystujące techniki kognitywne. Jeden z projektów, który realizowaliśmy, koncentrował się na wskazaniu rankingu wskaźników wymagających monitorowania, aby zwiększać produktywność w fabryce. Ranking powstał na podstawie analizy danych ze środowiska produkcyjnego, pochodzących z systemów IT i z dodatkowych czujników. To dobry wstęp do bardziej zaawansowanych projektów. W wyniku analizy danych historycznych i – co równie ważne – bieżących system rekomenduje wartości nastaw maszyn, których zastosowanie pozwala osiągać większe wartości OEE w danej sytuacji. Projekt był możliwy za sprawą integracji systemów IT, która stała się szerzej dostępna kilkanaście lat temu dzięki dostępności narzędzi klasy Enterprise Service Bus. Ułatwiły one stabilizację połączeń między systemami, bieżącą administrację oraz wprowadzanie zmian w zakresie architektury rozwiązań. Jakość danych produkcyjnych jest jednak w największym stopniu zależna od jakości zarządzania produkcją jako procesem.
– Duże znaczenie ma wiek maszyn, determinujący sposób, w jaki system MES otrzymuje dane z maszyny – podkreśla Kamil Mostowy. Jeszcze dziesięć lat temu podłączenie starszych maszyn do systemów informatycznych było ryzykowne i kosztowne, a montaż dodatkowych czujników był wyzwaniem. Obecnie proces retrofitingu – dostosowania starszego sprzętu do możliwości integracji z systemami informatycznymi – jest szybszy i opłacalniejszy.
Priorytet pomiaru OEE w poszczególnych branżach jest różny i zależy od wagi efektywności procesu produkcji. Wskaźnik ten bywa częścią procesów porównywania efektywności między lokalizacjami produkcyjnymi większych organizacji. W tym wypadku pomaga standaryzacja mierzenia wartości OEE, czyli odniesienie go do ISO.
– Od jakiegoś czasu MES dostępne są w chmurze – przypomina Piotr Rojek. – Poza oszczędnościami w zakresie infrastruktury technicznej interesującym rezultatem takich modeli jest kontrola metod liczenia OEE, głównie przez ograniczenie lokalnych ingerencji w algorytm.
W dynamicznym środowisku produkcyjnym kluczowe jest bieżące monitorowanie wydajności maszyn, aby zwiększyć efektywność operacyjną i minimalizować przestoje. Współczesne systemy MES oferują szeroki wachlarz wskaźników pozwalających na analizę dostępności maszyn, czasu cyklu oraz trendów wydajności. Przykładem takiego rozwiązania jest DXC SPARK – zaawansowana platforma analityki przemysłowej, która poza podstawowymi funkcjonalnościami umożliwia także analizę danych między zmianami, maszynami i typami produktów. Pomaga to optymalizować procesy oraz podejmować lepsze decyzje biznesowe. Z naszych obserwacji wynika, że poprawa produktywności dzięki zastosowaniu systemów analitycznych może wynosić od 15 do 25 proc., w zależności od charakterystyki produkcji. Ważnym aspektem monitorowania w czasie rzeczywistym jest także kontrola parametrów procesu i poziomu defektów, co pozwala na szybką reakcję na spadek jakości. Firmy wdrażające to rozwiązanie mogą obniżyć koszty utrzymania jakości średnio o 5 proc. Dodatkowo coraz większą rolę odgrywa analiza zużycia energii. Wgląd w tendencje wykorzystania zasobów energetycznych pozwala na identyfikację anomalii i redukcję kosztów operacyjnych nawet o 10 proc., co przekłada się na bardziej zrównoważoną produkcję – mówi Paweł Worożyszczew, Service Delivery Manager, DXC Technology Polska
Rzeczywisty obraz sytuacji
– Pytanie nie brzmi, czy warto wdrożyć MES, ale czy twoja firma jest gotowa na podejmowanie decyzji opartych na danych? – twierdzi Małgorzata Szewczyk, konsultantka ds. Lean w firmie Lean Action Plan. – Wskaźnik overall equipment effectiveness opiera się na trzech filarach: dostępności, wydajności i jakości. W teorii wszystko wygląda prosto, ale w praktyce często stosuje się „skróty myślowe”, a część danych pomija się w raportach. Mikroprzestoje? Zazwyczaj nie są rejestrowane. Wolniejsza praca maszyny z powodu gorszej jakości surowca? Często jest nieuwzględniana. Straty wynikające z częstych przezbrojeń? W raportach nie są zawsze widoczne. To właśnie dlatego szefowie przedsiębiorstw myślą, że ich maszyny działają lepiej niż w rzeczywistości. Bo przecież MES nie poprawia OEE, ale pokazuje prawdziwy obraz sytuacji. Dopiero znając ją, można rzeczywiście podnosić efektywność. Przez długie lata miałam okazję współpracować z wieloma zakładami produkcyjnymi i w każdym z nich temat overall equipment effectiveness przewijał się jako jedno z najważniejszych zagadnień. Każdy chciał poprawić wskaźniki efektywności, zmniejszyć przestoje i zwiększyć wydajność maszyn. W większości napotykano tę samą barierę: brak rzetelnych danych.
Wielu menedżerów jest przyzwyczajonych do analizowania przestojów po fakcie – na koniec zmiany, czasem po kilku dniach. To jak próba leczenia pacjenta na podstawie wyników badań sprzed tygodnia. System MES zmienia to podejście, dostarczając dane w czasie rzeczywistym. Jeśli maszyna zaczyna działać wolniej, natychmiast o tym wiadomo. Jeżeli z jakiegoś powodu część wyprodukowanych elementów nie spełnia norm jakościowych – system od razu to sygnalizuje. Co to daje? Przede wszystkim możliwość reakcji w momencie, gdy problem powstaje, a nie po czasie. Dzięki temu firmy eliminują straty, zanim się pojawią. Ale na tym nie koniec. System MES pomaga w lepszym obciążeniu maszyn, optymalizując plan produkcji na podstawie rzeczywistych możliwości sprzętu. Często się okazuje, że wystarczy zmienić kolejność zleceń, by lepiej wykorzystać czas pracy maszyn i uniknąć strat wynikających z niepotrzebnych przezbrojeń.
– W wielu zakładach, z którymi pracowałam, wdrożenie MES pozwoliło zwiększyć OEE z 55 proc do 75 proc. w ciągu roku bez inwestowania w nowy sprzęt – zwraca uwagę Małgorzata Szewczyk. – Czy MES sprawdzi się w starszym parku maszynowym? To jedno z najczęstszych pytań. Pracuję zarówno z firmami, które mają najnowocześniejsze centra obróbcze, jak i z firmami, w których stoją maszyny z lat osiemdziesiątych. Czy w takim środowisku system MES ma sens? Oczywiście! Czujniki Internetu rzeczy (IoT), odpowiednie interfejsy i integracja pozwalają na podłączenie także starszych maszyn. Kluczowe jest odpowiednie dobranie technologii. W jednym z zakładów wystarczyło podłączenie prostych adapterów i czujników, by uzyskać dane o rzeczywistych przestojach i obciążeniu maszyn. Rezultat? Przestoje zmniejszyły się o 30 proc., awaryjność spadła o 25 proc., a OEE wzrosło z 52 proc. do 67 proc. w ciągu roku. Najważniejsze jest jednak to, że MES pomaga ujednolicić źródła danych. Zamiast analizować wydajność każdej maszyny osobno, system pozwala na spojrzenie całościowe – niezależnie od producenta i wieku urządzeń.
Technologia to jedno, ale ważne jest to, co firma robi z danymi. Małgorzata Szewczyk widziała wdrożenia, które miały świetnie skonfigurowane systemy, ale nic się nie zmieniało, bo menedżerowie nie wykorzystywali dostępnych informacji. We wdrożeniu MES nie chodzi tylko o oprogramowanie – to zmiana podejścia do zarządzania produkcją. System może pomóc zwiększyć OEE o 10–20 proc., ale jeśli firma nie analizuje danych i nie wdraża działań korygujących, żadne oprogramowanie nie przyniesie oczekiwanych rezultatów.
Najczęstsze błędy
Do częstych niedopatrzeń należy przede wszystkim brak integracji MES z ERP. Dane z MES są, ale nie mają wówczas wpływu na planowanie produkcji. Kolejnym błędem są nieprawidłowo dobrane wskaźniki. Jeśli nie wiadomo, co dokładnie mierzyć, trudno podejmować dobre decyzje.
Nierzadkim błędem jest również oczekiwanie natychmiastowych rezultatów – MES pokazuje dane, ale ich analiza i wdrażanie działań wymagają czasu.
– System MES sam w sobie nie poprawia efektywności – przypomina Małgorzata Szewczyk. – To ludzie wykorzystują informacje do podejmowania najtrafniejszych decyzji. Zanim zaczniemy mówić o wdrożeniu, warto zadać sobie kilka podstawowych pytań. Czy dane o produkcji są zbierane ręcznie? Czy wiadomo, która maszyna generuje największe straty? Czy znany jest koszt jednej godziny przestoju? Jeśli na któreś z tych pytań odpowiedź brzmi: „nie”, oznacza to, że w procesie zarządzania produkcją występują luki. Widziałam wdrożenia MES, które spektakularnie poprawiały wyniki firm, ale i takie, które nie przyniosły żadnej wartości. Różnica zawsze leżała w tym, w jaki sposób organizacja podchodziła do analizy danych i podejmowania decyzji. System MES nie jest już tylko dla największych fabryk, staje się standardem w nowoczesnym zarządzaniu produkcją. Firmy, które umiejętnie go wykorzystują, nie tylko poprawiają OEE, lecz również zwiększają swoją konkurencyjność, minimalizując straty, lepiej zarządzając zasobami.
Overall equipment effectiveness w okolicach 85 proc. i więcej oznacza bardzo dobry poziom wykorzystania maszyn, zaś spadek poniżej 60 proc. wskazuje na konieczność wprowadzenia zmiany.
Patrzeć na całość
– Automatyzacja procesów przekłada się na efektywniejsze korzystanie z zasobów w firmach produkcyjnych – mówi Krzysztof Sobota, product manager w firmie Nexelem. – Mierzenie overall equipment effectiveness i sama świadomość zmian tego wskaźnika jest często kluczem do optymalizacji produkcji. Jednak dashboardy wyświetlające OEE oraz podpowiedzi systemów umożliwiające jeszcze skuteczniejsze podbicie wskaźnika to nic nowego w dobie rozwiązań klasy smart factory. W sytuacji optymalizacji overall equipment effectiveness łatwo popaść w dążenie do maksymalizacji jego wartości, podczas gdy nie zawsze jest to korzystne dla produkcji jako całości. Powiązane gniazda produkcyjne mogą mieć mniejszą przepustowość niż wybrane mocno optymalizowane gniazdo, co prowadzi do powstawania zatorów w przepływach materiałowych. Objawem mogą być np. pojawiające się nadstany na miejscach odkładczych. Dlatego optymalizując overall equipment effectiveness, należy patrzeć na fabrykę całościowo.
Co warto integrować z MES? Na pewno systemy ERP, aby uchwycić przepływy materiałowe oraz ich wartości finansowe. Dzięki temu poznamy na bieżąco rentowność produkcji, nie czekając na podsumowanie kwartalne czy roczną inwenturę.
Uwzględniając specyficzne otoczenie rynkowe, w jakim znalazły się firmy produkcyjne (rozchwianie zamówień, przejście z produkcji masowej na krótkie serie), ogromną wartość daje integracja MES z systemem planowania i harmonogramowania produkcji (APS), a w tym ujęciu – również z matrycami kompetencji będącymi rozszerzeniem MES. W ten sposób jedną ze zmiennych sterujących optymalizacją harmonogramu produkcji stają się dostępność pracowników oraz ich kompetencje, a także ujęcie ich wyników na podstawie raportów produkcji z MES.
Sanok Rubber Company (klient Nexelem), producent komponentów gumowych dla branży motoryzacyjnej i agro, borykał się z problemem zarządzania kompetencjami pracowników oraz ich powiązaniem z planem produkcji, uwzględniającym ograniczoną dostępność kompetencji pracowników. Dzięki integracji systemów otwarto zupełnie nowe możliwości planowania produkcji w jednym z zakładów firmy, Wprowadzono wielowariantowe zarządzanie personelem oraz zadaniami produkcyjnymi, z uwzględnieniem hierarchii w zakładzie, wpływającej na listę zadań produkcyjnych rozplanowanych na poszczególne osoby. Umożliwiło to automatyczne przypisywanie pracowników na bazie kompetencji i uwzględnienie, jak byli historycznie przypisani, co wpłynęło na integrację środowiska z wieloma systemami (SAP, system HR, system RCP, system planowania, system CMMS, system kart dostępowych). Pozwoliło ponadto na automatyczne przeliczanie zapotrzebowania na podstawie planu produkcji, prognoz produkcyjnych, symulacji i rzeczywistej realizacji produkcji. Dzięki temu MES stał się centrum wszechświata produkcyjnego, umożliwiając zarządzanie zmiennością produkcji i przestojami w czasie rzeczywistym.
– Wdrożenie nowoczesnych systemów MES i APS stanowi nie tylko optymalizację procesu produkcyjnego, ale także wymierne wsparcie dla menedżerów, którzy mogą podejmować lepsze decyzje dzięki dostępowi do całościowych danych. Era dashboardów i podpowiedzi „co zrobić” to dla dużych i ambitnych organizacji tylko wstęp do efektywniejszych działań opartych na big data (w tym uczeniu maszynowym). Doświadczenie w implementacji takich rozwiązań, jak w wypadku Sanok Rubber Company, pokazuje, że skuteczna integracja MES z APS, ERP i systemami HR to rzeczywistość, w której systemy rozmawiają ze sobą z pominięciem ludzi, aby osiągnąć wyższą niezawodność procesów i wydajność produkcji. Takie podejście, oparte na danych i głębokim zrozumieniu procesów produkcyjnych, pozwala ambitnym organizacjom produkcyjnym osiągać wyższą wydajność i konkurencyjność na rynku, którego immanentnymi cechami stały się ciągłe fluktuacje i nieprzewidywalność – podsumowuje Krzysztof Sobota.
Autor: Mieczysław T. Starkowski
Zobacz również