INTELIGENTNE TECHNOLOGIE
Wpływ systemu zarządzającego produkcją na produktywność przedsiębiorstw
Wpływ autonomicznego systemu samodzielnie zarządzającego produkcją IPOsystem na produktywność i antykruchość przedsiębiorstw produkcyjnych
Ale jak to? Przecież takiej metody naucza się na studiach, napisano mnóstwo książek i artykułów na ten temat, a dostawcy IT wdrożyli systemy APS w wielu firmach. Przecież skuteczne zarządzanie produkcją jest możliwe tylko dzięki planowaniu i harmonogramowaniu.
Autor artykułu: Krzysztof Fiegler
Data publikacji: 22.09.2022
Data aktualizacji: 03.11.2023
Podziel się:
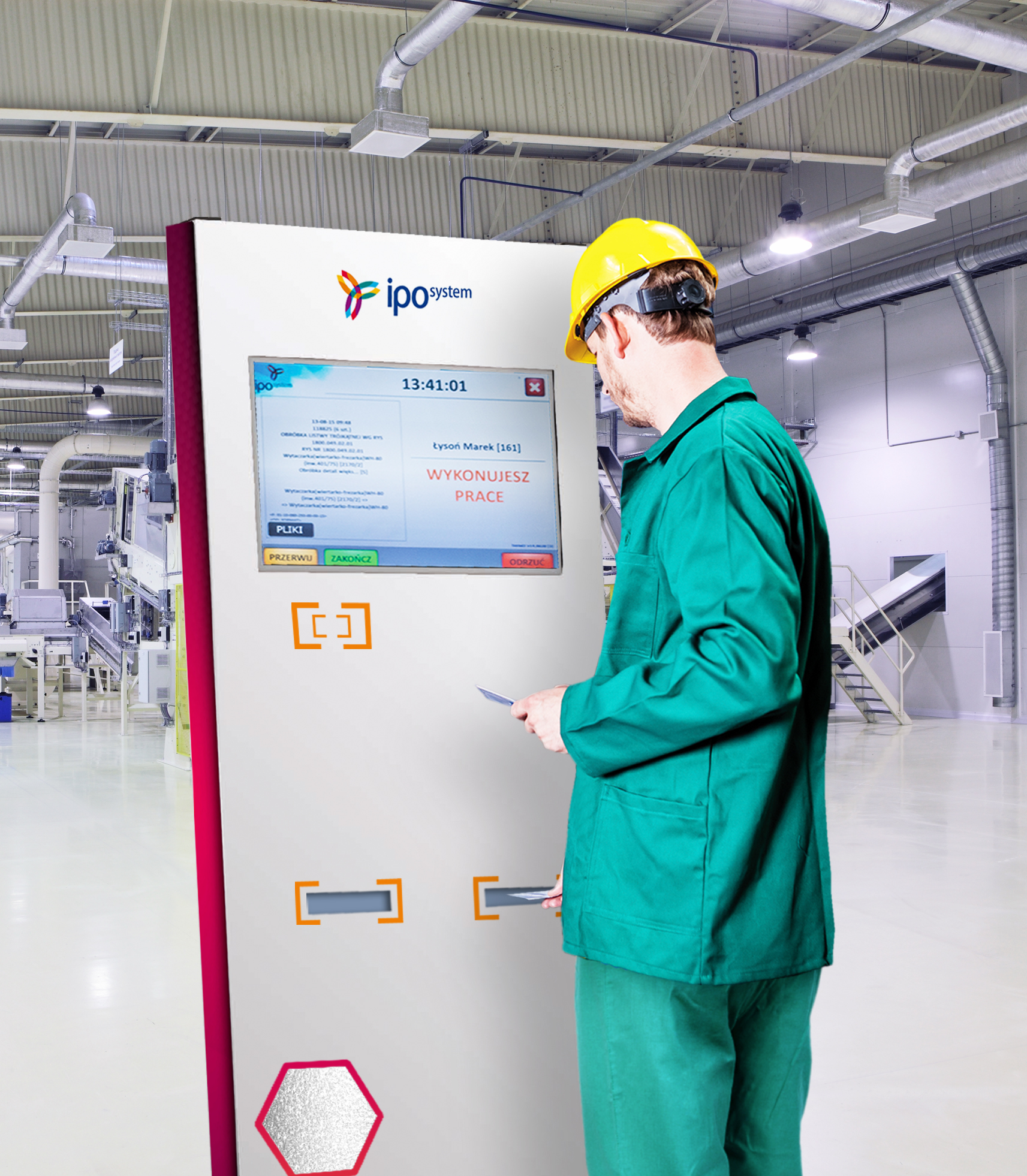
APS! Czy na pewno?
Idea tworzenia planów produkcyjnych odwzorowujących środowisko produkcyjne (APS), powstała na początku lat 90. XX w., gdy standardem była masowa produkcja – długie serie produkcyjne, niewielka wariantowość, niewielka zmienność, czasochłonne przezbrojenia. W takich warunkach szczegółowe plany produkcyjne miały swoje uzasadnienie.
Celem systemu APS jest przygotowanie harmonogramu produkcji. Ta obiegowa nazwa ukrywa fakt, że każdy plan w rzeczywistości jest symulacją. Przed uruchomieniem harmonogramowania musimy wprowadzić do systemu szereg założeń (parametrów planistycznych). Na ich podstawie APS przeliczy symulację i przygotuje szczegółowy plan produkcji, którego realizacja jest możliwa, gdy w rzeczywistych warunkach biznesowych i produkcyjnych uda się je wypełnić (inaczej należy szybko wprowadzić korektę i zasymulować nowy plan). W wypadku dużej zmienności parametrów planiści często nie nadążają z opracowywaniem nowych planów.
Aby przyśpieszyć harmonogramowanie, twórcy systemów APS opracowali szereg uproszczeń – definicje czasów operacji technologicznych nie uwzględniają różnic w rzeczywistych umiejętnościach pracowników. Pomijane są operacje okołoprodukcyjne (przygotowanie dokumentacji, przygotowanie i wydanie materiałów z magazynu, transport międzyoperacyjny, czynności kontroli jakości) oraz dostępność pracowników, gdy tworzony jest plan na gniazda produkcyjne, co powoduje przestoje i mikroprzestoje zasobów w wyniku konieczności ręcznego zarządzania tymi obszarami przez menedżerów.
Dodatkowo, w ramach „dobrych praktyk” wdrożenia systemów planistycznych, dąży się do ujednolicenia czasu realizacji operacji technologicznej przez wszystkie zasoby, np. na poziomie czasu średniego lub poniżej tego czasu. W rezultacie najbardziej produktywni pracownicy pracują z obniżoną wydajnością, ale zgodnie z planem. Ponadto dąży się do zamrażania planu na określony czas, aby unikać zmienności związanej ze stanem zleceń (nowe zlecenia, zmiany terminu, zmiany w ilościach), przez co firmy tracą tak istotną w obecnych warunkach gospodarczych elastyczność.
System zarządzający pracą
Wszystkie powyższe problemy rozwiązują systemy Manufacturing Operations Management (MOM) nowej generacji, których działanie oparte jest na autonomicznym systemie decyzyjnym Autonomous Decision System (ADS). Jednym z pierwszych takich systemów na świecie jest IPOsystem.
IPOsystem automatyzuje procesy planowania, bezpośredniego zarządzania zasobami i zbierania precyzyjnych danych o przebiegu procesów produkcyjnych. System podejmuje w czasie rzeczywistym decyzje dotyczące kolejności realizacji i doboru zasobów dla poszczególnych czynności technologicznych. Każdy pracownik, po zgłoszeniu gotowości do pracy w systemie, otrzymuje polecenie realizacji optymalnej w danym momencie operacji technologicznej.
Rysunek 1.
IPOsystem panuje nad całym obszarem produkcji i obszarami okołoprodukcyjnymi, zarządzając autonomicznie i bezpośrednio wszystkimi zasobami produkcyjnymi w czasie rzeczywistym.
System wskazuje precyzyjnie numer zlecenia produkcyjnego, stanowisko pracy, na którym należy wykonać pracę, szczegóły technologiczne operacji oraz miejsce, na którym znajdują się niezbędne, przygotowane przez system, materiały, półprodukty i narzędzia. Zarejestrowanie końca pracy w IPOsystem generuje kolejną decyzję systemu i wydanie zoptymalizowanego w danej chwili polecenia. Dzięki algorytmom decyzyjnym proces obliczenia i wydania pracy trwa nie dłużej niż pięć sekund. W ten sposób każdy pracownik w fabryce sterowanej przez IPOsystem pracuje w procedurze „praca – raport – praca – raport – …– praca – raport”.
Głównym celem algorytmów decyzyjnych systemu jest terminowa realizacja zleceń produkcyjnych przy maksymalnym wykorzystaniu dostępnego czasu wszystkich zasobów. System na bieżąco oblicza termin zakończenia zlecenia, informuje zarządzających o pracach, które są realizowane dłużej lub wolniej niż obowiązująca norma, wskazuje wąskie gardła w procesie.
Do interakcji pracownika z systemem służą terminale, tablety, smartfony, wyświetlacze sterowników maszyn, komputery osobiste, a w najbliższej przyszłości – rozszerzona rzeczywistość i polecenia głosowe. Za ich pośrednictwem IPOsystem przekazuje autonomicznie podjęte decyzje oraz umożliwia wprowadzenie dodatkowych raportów i informacji. System umożliwia również zbieranie i wykorzystywanie danych bezpośrednio z maszyn (IoT) oraz samodzielne sterowanie maszynami i robotami w procesach realizowanych bez udziału człowieka.
W systemie ADS, w przeciwieństwie do systemów APS, założone czasy realizacji poszczególnych operacji technologicznych mogą być przybliżone.
Celem menedżerów w IPOsystem nie jest planowanie, a następnie realizacja planu produkcji, ale rozwiązywanie problemów technologicznych i wydajnościowych.
Rysunek 2.
Schemat działania IPOsystem na hali produkcyjnej. W ten sposób system steruje pracą wszystkich pracowników/brygad.
Istotnym skutkiem pracy systemu jest zmiana w zachowaniu się pracowników na hali produkcyjnej. Starają się oni, przy zachowaniu wymagań jakościowych, jak najszybciej realizować wydawane przez system prace. Każdy pracuje w swoim optymalnym tempie, a system automatycznie w kolejnych decyzjach optymalizuje przebieg procesów produkcyjnych. Dzięki temu uzyskujemy bardzo precyzyjne i rzeczywiste dane o umiejętnościach i wydajności każdego pracownika, co umożliwia podjęcie odpowiednich działań doskonalących w miejscach, gdzie takie działania przyniosą najwyższą korzyść.
IPOsystem integruje się z dowolnym systemem ERP, pozwalając m.in. na pełną automatyzację tworzenia dokumentów magazynowych, zleceń produkcyjnych w IPOsystem, przenoszenie technologii i BOM-ów, przenoszenie i bieżącą aktualizację stanów materiałowych oraz zamówień na materiały.
Korzyści
• tanie zarządzanie – ograniczenie kosztów planowania i bezpośredniego zarządzania pracownikami nawet o 80 proc. w stosunku do systemów APS,
• zwiększenie produktywności przedsiębiorstwa nawet o 20–30 proc. po roku od zakończenia wdrożenia,
• zwiększenie wydajności każdego pracownika,
• wyeliminowanie przestojów związanych z przeplanowaniem, błędami w logistyce materiałów i narzędzi,
• uproszczenie i ułatwienie zasad zarządzania produkcją – brak konieczności ciągłego planowania i oceny planu oraz bezpośredniego zarządzania pracą ludzi,
• autonomiczna koordynacja między poszczególnymi działami eliminująca problemy z planowaniem i terminową realizacją zadań,
• obniżenie produkcji w toku,
• znaczna poprawa elastyczności przedsiębiorstwa w odpowiedzi na wymagania rynku,
• dostęp (również zdalnie, z dowolnego miejsca na świecie) do dokładnych, wiarygodnych i aktualnych danych o zleceniach, procesach i zasobach.
System dla wielu środowisk
IPOsystem działa już w niemal 60 fabrykach, sterując pracą ponad 12 tysięcy pracowników i wydając prawie 50 tysięcy decyzji operacyjnych dziennie. Fabryki, w których wdrożono IPOsystem, są różnej skali wielkości i zatrudnienia, reprezentującymi różnorodne branże i rozmaite typy produkcji, od produkcji indywidualnej, krótkoseryjnej, po masową. W każdej z nich po wdrożeniu IPOsystem nastąpiła gruntowna przemiana jakościowa.
Klient: Firma, która dostarcza elementy osprzętu sieci trakcyjnej dla kolejnictwa.
Wyzwanie: zarządzanie realizacją kilkadziesięciu tysięcy zleceń produkcyjnych rocznie.
Rozwiązanie: IPOsystem posiada rozbudowana funkcjonalność autoprodukcji. System samodzielnie, bilansując potrzeby wynikające z zamówień oraz analizując dostępne zasoby i obliczoną optymalną partię produkcyjną, uruchamia kolejne zlecenia z odpowiednimi datami realizacji, priorytetami i ilością.
Inny użytkownik systemu, który dostarcza maszyny oraz linie produkcyjne do przemysłowej produkcji lodów, osiągnął ponad dwudziestopięcioprocentowy wzrost produktywności. Firma podkreśla wiarygodność danych z IPOsystem, które wykorzystuje do celów motywacyjnych i premiowych. Wynika to z możliwości identyfikacji i analizy wydajności każdego pracownika w zależności od zewnętrznych uwarunkowań, co firma wykorzystuje w szkoleniach mniej wydajnych pracowników.
Klient: Producent monet obiegowych i kolekcjonerskich
Wyzwanie: duża zmienność panująca na produkcji połączona z ogromną liczbą operacji do wykonania
Rozwiązanie: IPOsystem umożliwił firmie zapanowanie nad tysiącami zmian, a jego autonomiczny mechanizm dba o optymalny przydział prac i ciągłość produkcji. Menedżerowie uwolnieni od rutynowych decyzji operacyjnych na bieżąco rozwiązują problemy technologiczne pracowników.
Dużemu polskiemu producentowi elektronarzędzi i narzędzi przemysłowych IPOsystem pozwolił zwiększyć stopień wielozadaniowości pracowników i znacznie podnieść ich wydajność. IPOsystem, dzięki swoim unikatowym algorytmom decyzyjnym nie tylko automatyzuje procesy planowania i bezpośredniego zarzadzania zasobami, uwalniając od tych zadań menedżerów, zmieniając ich role w zakładzie, ale także okazuje się skutecznym narzędziem wspierającym ciągłe doskonalenie. IPOsystem to skuteczne narzędzie Przemysłu 4.0, sprawdzające się nawet w najbardziej wymagających środowiskach produkcyjnych.
Artykuł ukazał się w nr 4(40) sierpień – wrzesień 2022 czasopisma „Production Manager”.
Więcej interesujących treści w naszym najnowszym wydaniu. Dołącz do klubu naszych prenumeratorów ▶ https://www.production-manager.pl/prenumerata/
Zobacz również