AUTOMATYKA I ROBOTYKA
Niepełny produkcyjny Golem. W głąb przemysłu 4.0
Już w połowie lat 90. Jeremy Rifkin stworzył koncepcję „końca pracy” spowodowanego gwałtownym rozwojem technologii. Ostrzegał, że będzie to problemem XXI stulecia. Po niemal 30 latach, w dobie przemysłu 4.0, koncepcja się urzeczywistnia. Ale nie dla wszystkich i nie wszędzie.
Data publikacji: 15.06.2021
Data aktualizacji: 17.11.2023
Podziel się:
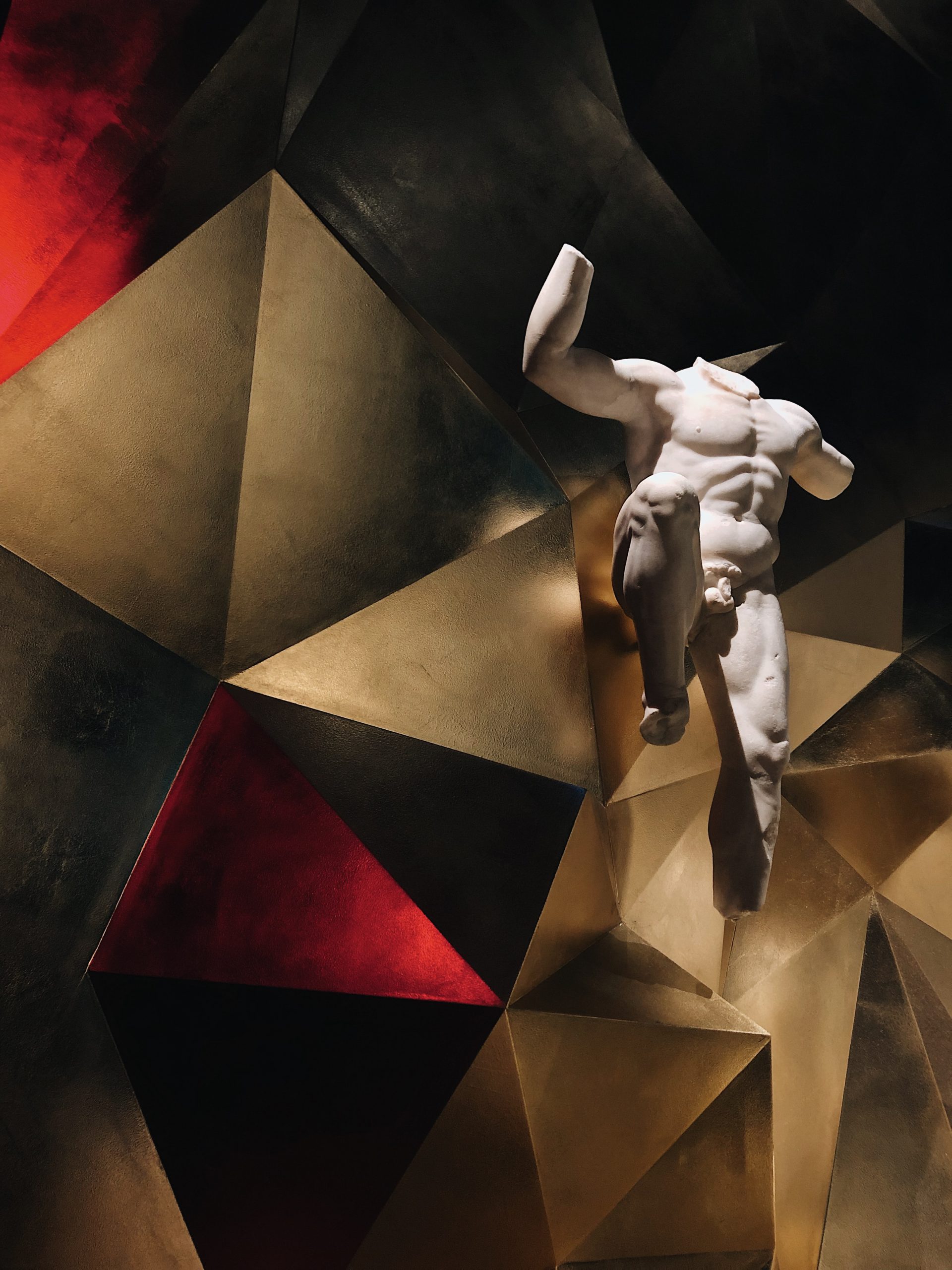
Piękny umysł
Czwartej rewolucji przemysłowej nie trzeba już specjalnie przedstawiać. Wiadomo, że składają się na nią potęga nowoczesnych komputerów o wysokiej mocy obliczeniowej, robotyzacja, rozbudowane technologie informacyjne, a kluczową rolę odgrywają analityka big data i rozwijająca się sztuczna inteligencja. Przemysł 4.0 to automatyzacja procesów produkcji oraz fabryki w pełni zintegrowane w jeden organizm, złożony z maszyn, urządzeń, technik i systemów informatycznych, procesów biznesowych i źródeł informacji wykorzystywanych w procesie produkcji. Różne obszary przedsiębiorstwa (smart factory) połączone są w inteligentne sieci, potrafiące samodzielnie się nadzorować i budujące zoptymalizowane ścieżki wytwórcze dla każde produktu. A technologia 5G zminimalizuje rozmiary sieci, pozwalając upchnąć setkę urządzeń komunikujących się ze sobą na jednym metrze kwadratowym Internetu rzeczy (IoT). Dzięki algorytmom samouczącej się AI produkcyjny Golem, wyposażony już w realne maszyny, cięgna, siłowniki, prasy i ciągi logistyczne, zyskuje zdolność samodzielnego myślenia, autokorekty działań i samonaprawy.
Najbardziej na tym procesie zyskuje konsument, który otrzymuje spersonalizowane, „szyte na miarę” produkty w krótszym czasie i w cenie standardowego produktu, dzięki bezpośredniej komunikacji z realizującą jego zamówienie fabryką. Tracą na tym kierowca ciężarówki, kolejarz, robotnik przetwórstwa spożywczego, pracownik administracji i obrotu pieniężnego, sprzątaczka lub kasjerka – ich zawody odejdą w zapomnienie. Kucharz i pielęgniarka – o ile przetrwają pandemię – na razie nie muszą się martwić o pracę. Powszechna jest opinia, że jako pracownicy będziemy podzieleni na tych mądrzejszych od maszyn i na tych tańszych od maszyn.
Następne dwudziestolecie
Zgodnie z projekcjami analityków firmy PwC czwarta rewolucja przemysłowa ma trzy etapy.
- Etap algorytmów (algorithm wave) – właśnie trwający i koncentrujący się na automatyzacji prostych zadań obliczeniowych i analizie ustrukturyzowanych danych w finansach, systemach informacji i komunikacji.
- Etap rozszerzenia (augmentation wave) – to etap, w który wejdziemy w pełni pod koniec lat 20. XX w. Skupiony jest na automatyzacji powtarzalnych zadań, np. wypełnianiu formularzy, komunikowaniu się i wymianie informacji, a także na analizie statystycznej nieustrukturyzowanych danych w częściowo kontrolowanych środowiskach, np. takich jak samoloty bezzałogowe i roboty.
- Etap autonomii (autonomy wave) – obejmie nas od początku lat 30. XX w. Nastąpi wówczas automatyzacja pracy fizycznej i czynności manualnych wykonywanych przez pracowników. Ponadto maszyny i roboty, w tym pojazdy autonomiczne, zastąpią ludzi w produkcji i transporcie, także w rzeczywistych, dynamicznych sytuacjach wymagających podejmowania decyzji. Pod koniec tego etapu 30 proc. miejsc pracy może zostać zautomatyzowane. Jednocześnie analitycy spodziewają się wzrostu liczby nowych zawodów. Należy jednak pamiętać, że, z jednej strony, przemysł będzie potrzebował osób nieposiadających wysokich umiejętności, zajmujących się prostymi pracami pomocniczymi na produkcji, a z drugiej strony – coraz cenniejsi będą pracownicy o najwyższych kwalifikacjach i wiedzy specjalistycznej. Z kolei pracownicy średniego szczebla, niepodnoszący swoich kwalifikacji, trafią na produkcję.
W związku z przemysłem 4.0 pojawia się także hasło reindustrializacji, stanowiącej szansę dla małych i średnich przedsiębiorstw, ponieważ specjalizacja regionów spowoduje rozproszenie ośrodków przemysłowych. A to stanie się lokalnym impulsem rozwojowym – uważają analitycy z Boston Consulting Group.
Praca – ale jaka?
PwC szacuje, że w Niemczech straci pracę 600 tysięcy pracowników przemysłowych, czyli prawie 10 proc. wszystkich zatrudnionych. Z drugiej strony powstanie ponad 900 tys. nowych miejsc pracy, z czego jednak tylko 200 tys. otrzymają wysoko wykwalifikowani programiści zajmujący się analizą danych, projektowaniem rozwiązań IT czy interfejsów dla użytkowników maszyn lub fachowcy z obszarów badawczo-rozwojowych. Reszta osób musi poszukać innych, niekiedy mniej złożonych zajęć.
Jednak poszukiwani będą także analitycy danych przemysłowych, koordynatorzy pracy robotów, fachowcy od zarządzania danymi i ich bezpieczeństwa, programiści maszyn i urządzeń, twórcy aplikacji, specjaliści do zarządzania produkcją i planowania procesów oraz sterowania maszynami. Ponadto powstaną nowe, poszukiwane stanowiska:
- specjaliści ds. sztucznej inteligencji (artificial intelligence specialists),
- specjaliści ds. transkrypcji medycznej (medical transcriptionists),
- analitycy danych (data scientists),
- specjaliści ds. sukcesów klientów (customer success specialists),
- praca programisty (full stack engineers),
- specjaliści ds. mediów społecznościowych (social media assistants),
- marketing z wykorzystaniem analityki (growth hackers).
Czwarta rewolucja przemysłowa zmienia zapotrzebowanie na profile zawodowe. Pracodawcy coraz częściej poszukują pracowników z know-how i umiejętnościami o charakterze technologicznym. Kluczowe stają się umiejętności STEM (science, technology, engineering and mathematics), czyli nauki ścisłe, technologia, inżynieria i matematyka. Nowe kierunki zatrudnienia stawiają też mocno na umiejętności społeczne i osobiste: samodzielne myślenie, zdolności analityczne, inteligencję emocjonalną i elastyczność poznawczą, bo to one mogą stać się niezbędne w nowej rzeczywistości. Czyli biegła znajomość nowych technologii już nie wystarczy, opłacani będziemy również za kreatywność, oryginalność, inicjatywę, krytyczne myślenie, perswazję, umiejętności negocjacyjne, dbałość o szczegóły, odporność, elastyczność i zdolność kompleksowego rozwiązywania problemów.
Cichaczem przemysł 4.0 wymusza dychotomiczny podział na wyższą kastę technokratyczno-menedżerską i wykonawców podstawowych, prostych prac. Technologiczna klasa średnia zanika, a majster będzie musiał odejść do lamusa. Szczególnie poszukiwani będą specjaliści posiadający kompetencje z zakresu specyficznych procesów produkcyjnych i automatyki przemysłowej, mający jednocześnie wiedzę i doświadczenie pracy z najnowszymi systemami sterowania i rozwiązaniami IT. O nowych wymaganiach już otwarcie informuje np. Siemens: „Inżynier 4.0 to osoba, która potrafi stać się motorem zmian w przedsiębiorstwie i będzie swoją firmę napędzać w kierunku cyfrowej transformacji. Przyjęcie tej roli wymaga jednak posiadania całej gamy zupełnie nowych kompetencji, wykraczających poza wiedzę ściśle techniczną”.
Według World Economic Forum do 2022 r. około 54 proc. pracowników będzie musiało przekwalifikować się lub podnieść kwalifikacje, ale i tak nie zmieni to faktu, że za tym zróżnicowaniem systemowym pójdzie duże zróżnicowanie finansowe, które już jest bólem głowy socjologów. Wynika to m.in. z niemożności dalszego podnoszenia kwalifikacji przez niektóre grupy zawodowe. Na przykład mechanik samochodowy musiałby stać się absolwentem wydziału elektroniki, aby móc naprawiać pojazdy przemysłu 4.0, podobnie jak kierowca ciężarówki.
Polski piekarz 4.0
Według PwC już podczas drugiego etapu rewolucji 4.0 liczba miejsc pracy w Polsce zostanie zredukowana o 18 proc. ze względu na wzrost automatyzacji o 16 proc. Wiele polskich firm i branż uśpionych mitem przewagi niższych kosztów robocizny nie dostrzega zagrożenia 4.0, które może wpędzić kraj w spiralę marginalizacji. Przy braku wdrożenia przemysłu 4.0 w krajach rozwijających się oznacza to transfer produkcji przemysłowej do krajów wdrażających koncepcję, nawet jeśli koszty pracy są tam wyższe, bo finalny produkt hi-tech i tak będzie tańszy oraz lepiej wykonany. Do tego tracimy swoją przewagę konkurencyjną – położenie geograficzne – ponieważ w realiach przemysłu 4.0 firmy decydują się przenosić swoje zakłady produkcyjne, ignorując aspekt kosztowy i geograficzny. Nam pozostanie produkcja wierzbowych narodowych mioteł.
Zagrożenia stojące przed polskim przemysłem i rynkiem pracy to niska świadomość zmian na poziomie menedżerskim, brak priorytetu rozwoju technologii przemysłu 4.0 ze strony polskiego państwa, utrudniony dostęp do szkoleń pracowników, brak wymaganych nakładów inwestycyjnych i niska świadomość ochrony własności intelektualnej. Zagrożenia te łączą się z danymi mówiącymi, że większość polskich firm wciąż tkwi w rzeczywistości 3.0, a część wciąż nawet 2.0 (czyli na poziomie elektryfikacji i wynalezienia linii produkcyjnej). Tymczasem z badań firmy ASTOR wynika, że większość polskich firm określa, że jest na etapie rewolucji 4.0 (42,44 proc.), ale jedynie 7 proc. przedsiębiorców deklaruje, że wdrożyło przemysł 4.0. Potwierdza to raport firmy Roland Berger „INDUSTRY 4.0. The new industrial revolution. How Europe will succeed”, w którym kraje Europy podzielono na grupy liderów, potencjalnych, wahających się oraz tradycjonalistów. Polska wraz z Włochami, Hiszpanią i Portugalią została zaklasyfikowana do grupy państw wahających się, czyli o niskiej gotowości do wdrożenia przemysłu 4.0.
Niepokojący jest także brak kadr dla przemysłu 4.0, które trzeba wykształcić, tworząc nowy system kształcenia, ponieważ nowe stanowiska pracy wymagają nowych, nienauczanych dotąd w Polsce umiejętności. Istnieje bowiem ryzyko pojawienia się wielu wakatów (np. na stanowisku koordynatora robotów przemysłowych) przy jednoczesnym strukturalnym bezrobociu. Na razie państwo zajęło się kształceniem rzemieślników i czeladników w wymiarze przemysłu 4.0. Choć nie powinno to przecież dziwić w kraju, w którym czeladnik piekarski funkcjonuje jako rzecznik prasowy rządzącej Polską partii.
Przegoni nas obcy przemysł 4.0?
Tymczasem przemysł 4.0 galopuje, mimo pandemii. O ile w 2018 r. średnio 71 proc. łącznych godzin pracy wykonywanych było przez ludzi, a 29 proc. przez maszyny, o tyle oczekuje się, że do 2022 r. już tylko 58 proc. czasu pracy przypadać będzie na ludzi, a 42 proc. na maszyny. Raport analityków Deloitte „Przemysł 4.0 w Polsce – rewolucja czy ewolucja?” nie pozostawia wątpliwości, na jakie przeszkody natrafiamy: brak wdrożeń i szkoleń dla szeregowych pracowników, trudności związane z poszukiwaniem, szkoleniem oraz utrzymaniem kompetentnych talentów, potrzeba budowania kultury organizacyjnej, która byłaby w stanie wspierać transformację cyfrową. Kolejny problem to brak wewnętrznej spójności w zakresie strategii rozwoju w firmach oraz brak spójności w zakresie wykorzystywanych narzędzi cyfrowych.
Jednak, zdaniem ekspertów, gwałtowne wdrażanie przemysłu 4.0 w Polsce niesie ryzyko zadławienia się, dlatego należy go wprowadzać stopniowo, poczynając od „wysp cyberfizycznych”. Nieważne, czy nazwiemy je zaawansowanymi rozwiązaniami przemysłu 3.0, czy wczesnym etapem rozwoju przemysłu 4.0. Ważne, żeby panować nad wyspami dziś, czyli nad danymi, które generują, ich odczytem, interpretacją i bezpieczeństwem, a jutro łączyć je w całość. Do tego jeszcze warto wykształcić pracowników, którzy te wyspy obsłużą. Z kolei w warstwie organizacyjnej najważniejszą zmianą powinno być przejście od kultury organizacji dyrektywnej do angażującej, co jest samo w sobie trudnym zadaniem. Zanim rozpocznie się ten proces, warto sobie zadać poniższe pytania:
- Jakie będą rzeczywiste korzyści dla naszej firmy z wdrożenia rozwiązań przemysłu 4.0?
- Ile czasu i środków należy przeznaczyć na wdrożenia tych rozwiązań?
- Czy te wszystkie roboty, czujniki, skomplikowane systemy nadzorowania i sterowania są nam potrzebne?
- Czy jesteśmy w stanie odpowiednio zabezpieczyć gromadzone dane?
- Czy znamy cel naszych działań i potrafimy dobrze wykorzystać dane i informacje, które otrzymamy?
Jeśli odpowiedzi są znane, można śmiało ruszać w głąb przemysłu 4.0.
Główną przyczyną luki technologicznej w Polsce jest stosunkowo długo utrzymujący się splot korzystnych czynników rynkowych: łatwego dostępu do pracowników (w tym taniej siły roboczej napływającej z innych krajów), niższych kosztów produkcji i dobrej lokalizacji w Europie. Producenci korzystający z takich przywilejów nie czuli potrzeby wprowadzania zmian w modelu produkcji, w przeciwieństwie do firm działających globalnie. Dziś musi się to zmienić, dlatego bardzo ważne jest upowszechnianie wiedzy na temat nowych technologii, szczególnie korzyści wynikających z jej zastosowania w sektorze przemysłu. We wspólnym interesie firm i sektora akademickiego jest przygotowanie przyszłych kadr do pracy wymagającej większej otwartości, chęci bieżącego uczenia się, samorozwoju, funkcjonowania w bardziej elastycznym i kreatywnym modelu współpracy.
Podejmując wyzwanie poprawy dostępu do edukacji w Polsce, stworzyliśmy Akademię FANUC, która oferuje pracownikom fabryk wiele możliwości podnoszenia kwalifikacji – od wstępnych programów szkoleniowych dla początkujących po kursy dostosowane do potrzeb ekspertów i specyficznych zastosowań. Ponadto wspieramy szkoły, organizujemy warsztaty dla młodzieży i działamy na rzecz zwiększania ogólnej świadomości na temat korzyści wynikających z robotyzacji. Przyszłym pracownikom fabryk oferujemy programy stażowe umożliwiające zapoznanie się z naszą technologią, a także aktywny udział w projektach wdrażania maszyn i robotów do polskich fabryk.
Jędrzej Kowalczyk
prezes zarządu
FANUC Polska
Obserwowany rozwój technologii spowoduje ogromne zmiany na rynku pracy. Rezultatem będą nowe zawody i potrzeba rozwoju istotnych kompetencji z nimi związanych z dziedzin nauk ścisłych i nauk społecznych: programowanie oraz projektowanie połączone z pracą zespołową i dobrą komunikacją. System edukacji powinien głębiej przenikać się z przemysłem i biznesem. O tym mówi się od dawna, podejmowanych jest wiele działań, m.in. z wykorzystaniem funduszy Unii Europejskiej. Wydaje się jednak, że można zrobić zdecydowanie więcej. Obecnie duża grupa absolwentów uczelni technicznych wchodzi na rynek pracy wyposażona w wiedzę teoretyczną. Brakuje praktyki – umiejętności stworzenia koncepcji automatyzacji danego procesu, policzenia stopy zwrotu z inwestycji w robotyzację, zarządzanie ryzykiem związanym z procesem implementacji czy zespołem realizującym dany projekt. Nauczyć się tego można tylko w działaniu, być może przez programy wsparcia dla robotyzacji powiązane z zaangażowaniem w projekty studentów. Z naszej strony dostarczamy stanowiska edukacyjne dla szkół i uczelni wyższych. Do tego prowadzimy wiele szkoleń mających na celu budowę świadomości i kompetencji z zakresu automatyzacji i robotyzacji. Rokrocznie oferujemy studentom miejsca do odbywania praktyk w naszej firmie, gdzie stykają się z praktycznymi problemami. Wielu z nich zostaje z nami i rozwija robotyzację polskiego przemysłu.
Krople:
- 10 proc. osób straci pracę w przemyśle niemieckim w wyniku czwartej rewolucji przemysłowej.
- 54 proc. pracowników będzie musiało do 2022 r. przekwalifikować się lub podnieść kwalifikacje.
- Do 2022 r. już tylko 58 proc. czasu pracy przypadać będzie na ludzi, a 42 proc. na maszyny.
Radosław Matiakowski
prezes zarządu
CoRobotics Sp. z o.o.
Artykuł ukazał się w nr 1(31) luty-marzec 2021 czasopisma „Production Manager”.
Więcej interesujących treści w naszym najnowszym wydaniu. Dołącz do klubu naszych prenumeratorów ▶ https://www.production-manager.pl/prenumerata/
Zobacz również