AUTOMATYKA I ROBOTYKA
Metody Smart Manufacturing Kaizen Level (SMKL)
Jeśli prześledzimy historię przemysłu albo – szerzej – wytwarzania, zauważymy powtarzający się scenariusz. Co jakiś czas pojawiają się narzędzie, metoda lub technologia, które zmieniają reguły gry: silnik parowy, taśma produkcyjna czy roboty przemysłowe. Początkowo wdrażają je nieliczni, później stają się one popularne, w końcu okazuje się, że rezygnacja z nich jest równoznaczna z marginalizacją.
Data publikacji: 21.10.2021
Data aktualizacji: 26.10.2023
Podziel się:
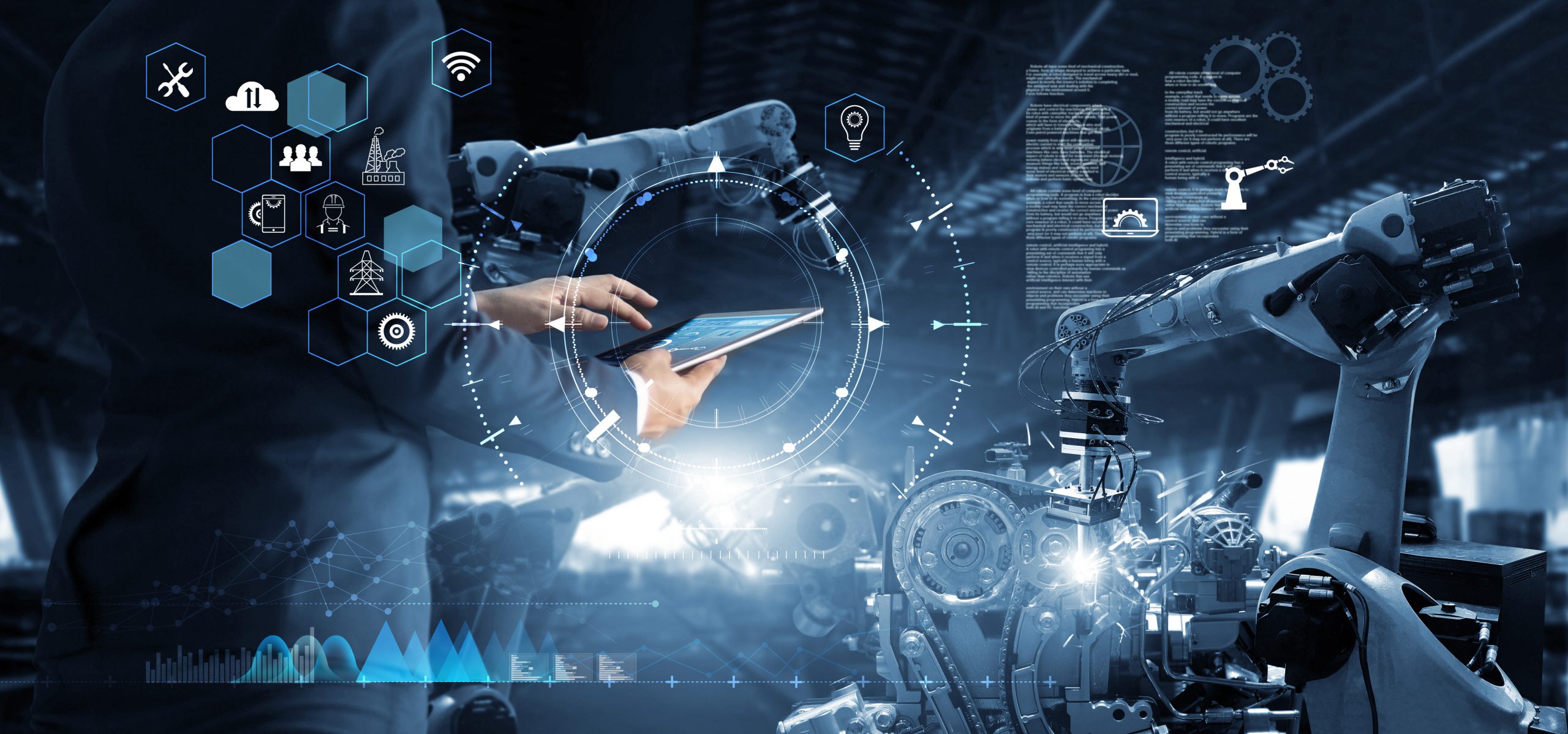
Obecnie taka rola przypada w udziale cyfryzacji produkcji. Jesteśmy między fazą fascynacji teoretycznymi możliwościami a uświadomieniem ryzyka biznesowego związanego z opóźnianiem decyzji o implementacji zasad przemysłu 4.0. Wiadomo już, że rezygnacja z cyfryzacji w perspektywie kilku lat będzie oznaczała narastające problemy z konkurencyjnością. Dlatego tak ważna jest odpowiedź na pytanie: jak zacząć i którą ścieżką podążać, żeby zmodernizować produkcję w sposób, który zaakceptują wszyscy”: od pracowników po zarząd i akcjonariuszy?
Zmiany muszą mieć sens
Strategia wprowadzania zmian musi uwzględniać ryzyko inwestycyjne, założone cele biznesowe, ale także możliwości zasobów przedsiębiorstwa. Planowanie działań i ocenę efektów można sobie ułatwić na wiele sposobów. Jednym z nich są metody Smart Manufacturing Kaizen Level (SMKL), w których przedstawia się poziom zarządzania, na którym wprowadzane są zmiany, i stopień ich zaawansowania. Jest to koncepcja strukturalnego podejścia do projektów cyfrowych, opracowana i używana przez fabryki Mitsubishi Electric.
Wolniej, ale konsekwentnie
Niewielkie zmiany mają ograniczony zasięg, angażują niewielką grupę pracowników, do ich przeprowadzenia wystarczą relatywnie niewielkie inwestycje. Ograniczone będą również ewentualne skutki błędów i nieprzewidzianych komplikacji. Po osiągnięciu jednego celu można obiektywnie ocenić rezultaty zmian, zestawić koszty z korzyściami, wyciągnąć wnioski i uwzględnić je przy planowaniu kolejnego kroku.
Ta metoda, charakterystyczna dla filozofii Kaizen, sprawdza się zarówno w małych przedsiębiorstwach, jak i w wielkich organizacjach. Porządkuje proces wprowadzania zmian i pełni funkcję zabezpieczenia. Jeśli się okaże, że któraś z cząstkowych decyzji była chybiona, można się z niej wycofać bez wywoływania lawiny niepożądanych zdarzeń.
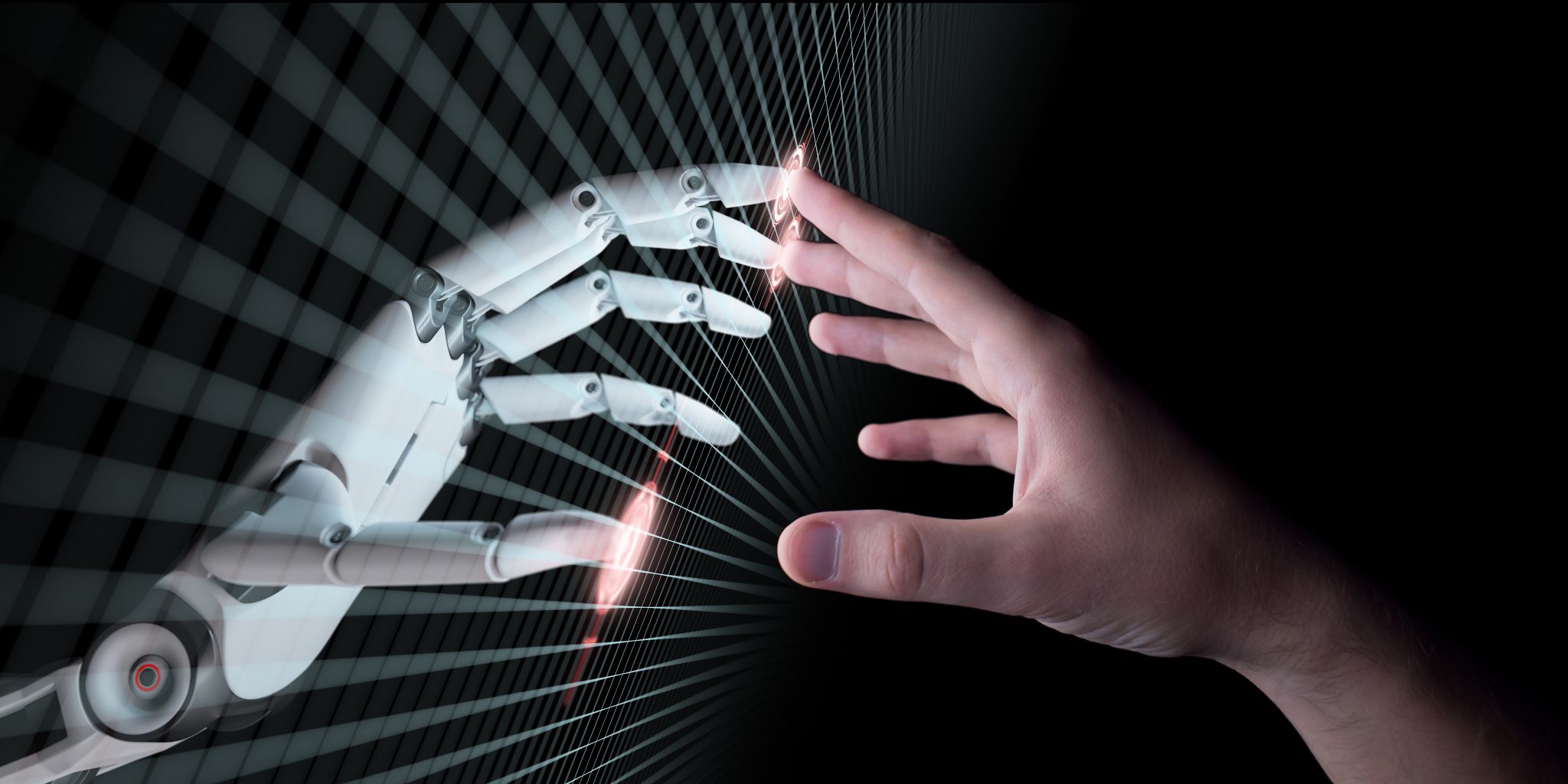
Wsparcie od początku
Metoda SMKL to świadome podejście do modernizacji. Na początku każdego projektu musi być określony obecny poziom digitalizacji. Ustalamy go bardzo konkretnie – łańcuch produkcyjny dzielimy na cztery obszary: stanowisko operatora, linia, cały zakład i cały łańcuch produkcyjny. Następnie w każdym z tych miejsc określamy poziom wdrożenia, który chcemy osiągnąć. Wybieramy także jeden z czterech poziomów: zbieranie danych, wizualizacja, analityka, optymalizacja. Metoda zatem używa prostych kryteriów oraz jest osadzona w realiach każdego miejsca w zakładzie. Określenie swojego poziomu jest o tyle ważne, że następnym ruchem jest zrobienie jednego małego, ale konkretnego kroku, aby przenieść się na inny poziom (wdrożenia czy zakładu).
Historia pewnej maszyny
W jednej z fabryk spożywczych produkujących ciastka kluczowa była maszyna do wyciskania porcji ciasta do pieczenia. Z nieznanego powodu wydajność tej maszyny pogarszała się z czasem, po czym znowu się poprawiała. Kluczowym jej elementem był cylinder pneumatyczny, który odpowiadał za napędzanie wyciskarki. Razem z klientem postanowiliśmy przyjrzeć się temu elementowi. Wiedzieliśmy, że maszyna nie ma czujników, więc pierwszym krokiem było zebranie sygnałów z tej konkretnej części. Dokładając dwa czujniki i prosty sterownik, zaczęliśmy zbierać dane o czasie ruchu cylindra. Analizując je, zauważyliśmy, że czas otwarcia i zamknięcia wydłuża się z każdą godziną pracy maszyny. Zmiany te jednak były właściwie niezauważalne dla ludzkiego oka, cykl wydłużał się bowiem powoli: z 1 s do 1,2 s. To aż 20 proc., jednak niemożliwe do wychwycenia przez ludzką percepcję. Zestawiając dane, można od razu to zauważyć! Dzięki temu znaleziono przyczynę spadku wydajności – ciasto ze względu na swoją strukturę z każdym ruchem lekko zapychało cylinder. Rozwiązaniem było opracowanie metody oczyszczania. Dzięki prostemu wdrożeniu odzyskano pierwotną produktywność maszyny. Kolejny krok był naturalny: dane z tabel przetworzono na czytelną wizualizację, z której korzystał operator i mógł reagować od razu, gdy cykl się wydłużał poza akceptowalny poziom. Tak działającą aplikację powielono na pozostałe maszyny w zakładzie, a w konsekwencji osiągnięto zamierzony cel. Nie byłoby to możliwe bez danych, ale także bez nastawienia, że najmniejszy nawet krok może dużo zmienić.
Przekonać zespół
Zmiana urządzeń czy modyfikacja procedur kształtują od nowa środowisko pracy. Pracownicy muszą przełamać rutynę, która stwarzała poczucie komfortu, i zmierzyć się z nowymi wyzwaniami. Wiąże się to z dodatkowym wysiłkiem i obawą przed popełnieniem błędu. Nie wolno ignorować samopoczucia osób zaangażowanych w zmiany. Od niego zależy akceptacja nowości, a w konsekwencji powodzenie przedsięwzięcia. Wywołanie fali odejść z pracy jest ostatnią rzeczą, której potrzeba modernizującej się organizacji. Zwłaszcza jeśli dotyczą osób z dużym doświadczeniem i unikalnymi kompetencjami. Przygotowanie zespołu do zmian oznacza także szkolenie, czasami rekrutację nowych pracowników. Wdrażanie mechanizmów raportowania czasu pracy, pomiaru czasu przestoju, identyfikacji wąskich gardeł kojarzą się z inwigilacją i dodaniem nowych obowiązków. Większość tych obaw można rozwiać, informując o planach, spodziewanym przebiegu procesu i oczekiwanych skutkach zmian.
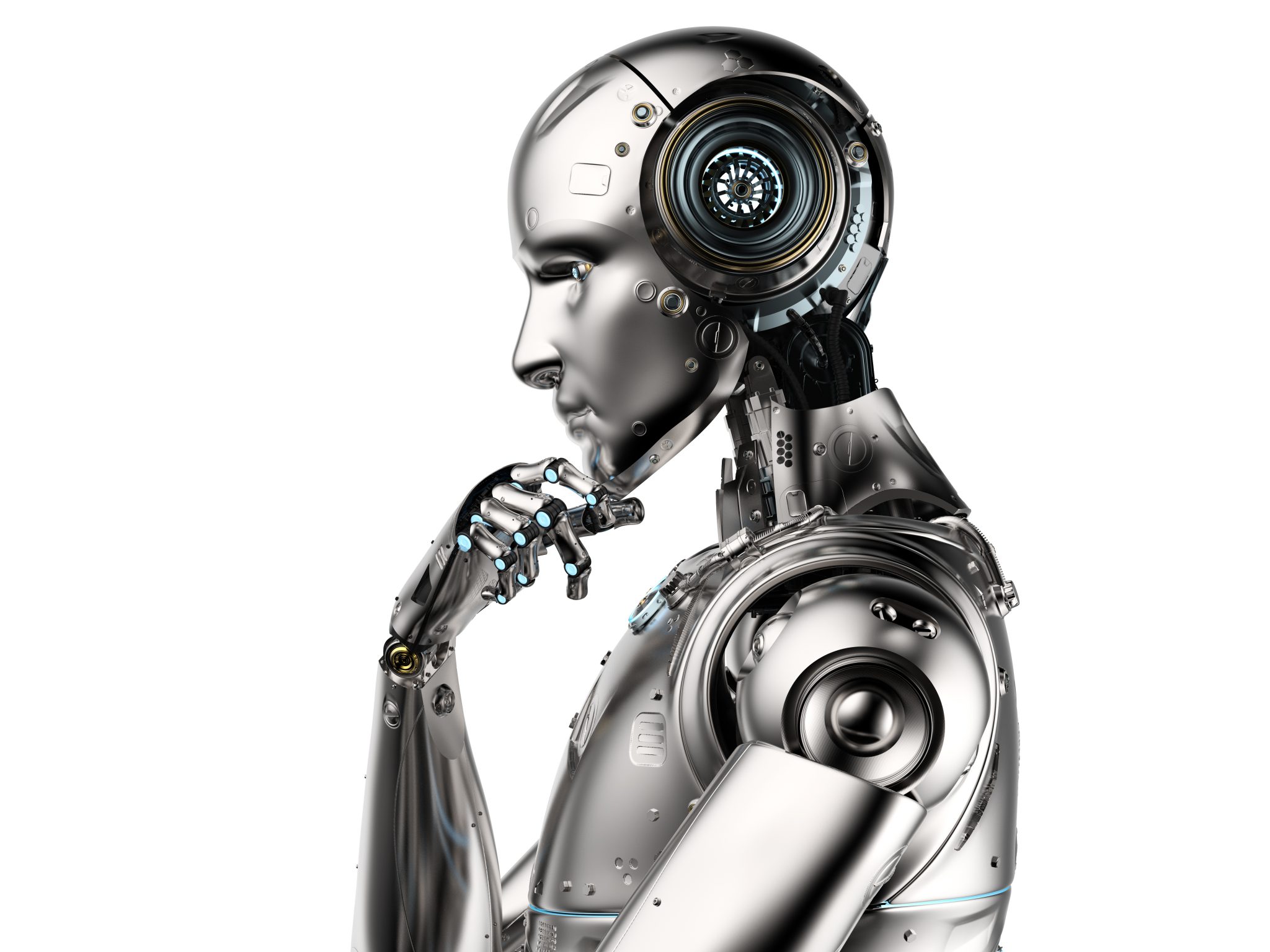
Sprawdzaj postępy
Wpływ wdrożonych rozwiązań na wynik finansowy przedsiębiorstwa można oceniać na podstawie wielu wskaźników. Jednym z nich jest overall equipment effectiveness (OEE), pokazujący efektywność wykorzystania maszyn i urządzeń. Współczynnik jest obliczany w systemie informatycznym przedsiębiorstwa na podstawie danych zbieranych z urządzeń i przesyłanych za pośrednictwem sieci. Można w ten sposób określić całkowity czas postoju, jakość wytwarzanych elementów, śledzić losy każdej części i monitorować stan fabryk czy identyfikować wąskie gardła i oceniać skuteczność podejmowanych działań. Biznes bazuje na faktach, decyzje powinny być podejmowane na podstawie twardych danych. Tylko wtedy można skutecznie zarządzać przedsiębiorstwem. Odnosi się to do firm każdego rozmiaru, tyle że wraz ze wzrostem organizacji zwiększa się strumień danych, które trzeba wziąć pod uwagę. Aplikacja do pomiaru OEE, gotowa do wdrożenia w zakładach, jest dostępna w ofercie Mitsubishi Electric. Jednym z użytkowników jest fabryka produkująca elementy do urządzeń AGD. Dzięki wdrożeniu aplikacji OEE osiągnięto tam spodziewany skutek: wzrost produktywności o około 17 proc. Uzyskano go jednak w nieoczywisty sposób. Pracownicy zaczęli zwracać uwagę na wyniki OEE, a to spowodowało wyrównanie produktywności na wszystkich trzech zmianach. Skrócono także średni czas cyklu przez skrócenie czasu przestojów maszyny. Zarząd zakładu dodatkowo ma dokładny obraz produkcji w raportach, opracowany na podstawie tych samych danych, dzięki czemu uprościł się proces planowania produkcji. Niewielka zmiana technologiczna oraz zmiana nastawienia pracowników pozwoliła osiągnąć efekt zwrotu z inwestycji na poziomie czterech, pięciu miesięcy. SMKL to docenienie małych kroków, niewielkich projektów, które – naszym zadaniem – wyznaczają drogę do cyfrowej fabryki przyszłości (Smart Factory). W języku angielskim „smart” to także spryt. A spryt to osiąganie wielkiego rezultatu małym nakładem. I dlatego właśnie małe nakłady (małe kroki, małe projekty) prowadzą nas to wielkiego wyniku.
Artykuł ukazał się w nr 4(34) sierpień-wrzesień 2021 czasopisma „Production Manager”.
Więcej interesujących treści w naszym najnowszym wydaniu. Dołącz do klubu naszych prenumeratorów ▶ https://www.production-manager.pl/prenumerata/
Zobacz również