ZARZĄDZANIE
Z siedmiu marnotrawstw do trzech: Metoda Yamady
Wszystko ulega przeobrażeniom. Nawet zasady leżące u podstaw Lean Management mogą – i powinny się – zmieniać. Mam szczęście utrzymywać relacje zawodowe z Hitoshi Yamadą, jedynym bezpośrednim autorytetem w zakresie koncepcji Taiichi Ohno, który osobiście upoważnił Yamadę do kontynuowania swojej spuścizny. Yamada jest zdecydowanie osobą, której warto posłuchać, jeżeli chcemy się dowiedzieć, w jaki sposób nowoczesne firmy wcielają w życie w najbardziej zaawansowany wariant metody Ohno.
Data publikacji: 24.02.2021
Data aktualizacji: 13.11.2023
Podziel się:
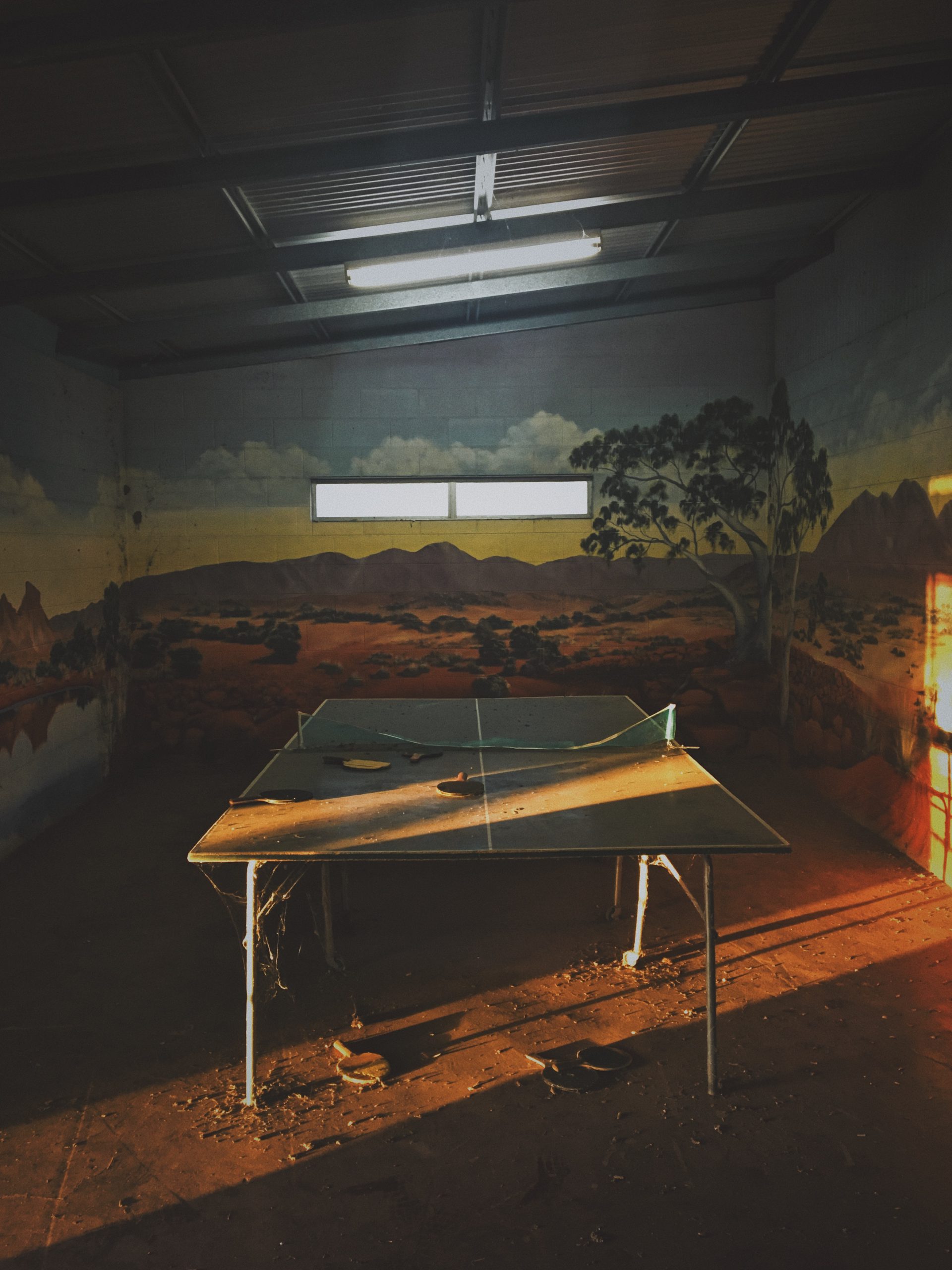
Kiedy Taiichi Ohno rozpoczął pracę w Toyocie, wyznaczono mu niezwykle ambitny cel: miał nadrobić różnicę w wydajności produkcji względem Stanów Zjednoczonych. Mówiono wówczas, że wydajność w Stanach Zjednoczonych jest dziewięciokrotnie wyższa niż w Japonii. Doprowadziło to do odkrycia słynnych siedmiu rodzajów marnotrawstwa. Zaproponowany przez Ohno podział rodzajów marnotrawstwa stał się kluczowym czynnikiem w przełomowym sukcesie Toyoty i innych firm w latach 70. i 80., więc wiele organizacji zaczęło naśladować metodę Ohno. Niektóre firmy dodały jeszcze ósmy rodzaj marnotrawstwa, spopularyzowany przez Normana Bodka, jakim jest niedostatecznie wykorzystany talent człowieka, jednak główne rodzaje marnotrawstwa zazwyczaj pokrywały się z tymi opracowanymi przez Ohno dla Toyoty wiele lat temu. Po śmierci Ohno Yamada otrzymał własne zadanie: miał dostosować metody Ohno w taki sposób, aby sprawdzały się w wielu gałęziach przemysłu niezwiązanych z produkcją.
Oczywiście marnotrawstwo ma wiele postaci. Gdyby tak nie było, osoby takie jak ja nie miałyby pracy. Ta różnorodność marnotrawstwa sprawiła, że Ohno zdecydował się w pierwszej kolejności podzielić je na kategorie. Uogólnienie tysięcy różnych problemów i milionów różnych okoliczności, w jakich mogły się one pojawić, do zaledwie siedmiu kategorii sprawiło, że o wiele łatwiej je zidentyfikować i wyeliminować. Co może nawet ważniejsze, tak ogólnie sformułowane kategorie pomagają zrozumieć nie tylko to, co jest marnotrawstwem, ale również dlaczego coś nim jest. Po wielu latach nauki pod kierownictwem Ohno Hitoshi Yamada uświadomił sobie, że pięć z siedmiu rodzajów marnotrawstwa wynika z tej samej przyczyny, którą nazwał stagnacją. Ta nowa kategoria była o wiele łatwiejsza do zrozumienia poza obszarem produkcji. Co ciekawe, dwie kategorie, które nie pasowały do tej grupy, są często uznawane za najtrudniejsze do odróżnienia: zbędny ruch i zbędny transport. Na podstawie tych spostrzeżeń Yamada podzielił rodzaje marnotrawstwa na zaledwie trzy kategorie: zbędny ruch, zbędny transport i stagnacja. Podział ten pozwalał pracownikowi na szybszą identyfikację problemu i jego rozwiązanie, zamiast snucia rozważań na temat klasyfikacji.
Problem podziału pracy
Przenośniki taśmowe są jedną z najważniejszych ikon masowej produkcji XX w. Związane z ich użytkowaniem marnotrawstwa są dobrze znane. Często są one przedmiotem kpin, począwszy od filmu Charliego Chaplina „Dzisiejsze czasy”, kończąc zaś na „Kocham Lucy” czy nawet „Ekstrakcie” Michaela Judge’a. Jak na ironię, przenośniki taśmowe to wciąż powszechny widok w organizacjach usiłujących wdrożyć metodę Just-in-Time w ramach koncepcji Lean Production. Nawet legendarna linia produkcyjna Toyoty to tak naprawdę bardzo zaawansowany technologicznie i dobrze zarządzany przenośnik taśmowy.
Eliminacja przenośników taśmowych i zastąpienie ich stacjonarnymi stanowiskami pracy przyniosły fantastyczne rezultaty w firmach takich jak Sanyo Electric (obecnie podmiot zależny Panasonic) czy Canon oraz w innych organizacjach, w których Yamada był zaangażowany jako osoba odpowiedzialna za przekształcenie zakładu produkcyjnego. Dlaczego przenośniki taśmowe to marnotrawstwo? Dlatego, że są ucieleśnieniem podziału pracy. Bez względu na to, jaką branżę reprezentujesz, sporą część marnotrawstwa związanego ze stagnacją (również w twoim wypadku) można prawdopodobnie przypisać temu funkcjonującemu od wielu lat sposobowi myślenia typowego dla produkcji masowej.
Stagnacja
Stagnacja to wszystko, co sprawia, że ludzie, informacje czy maszyny oczekują w przerwach w pracy wytwarzającej wartość dodaną. Interesujące jest to, że oczekiwanie było pierwszym rodzajem marnotrawstwa odkrytym przez Ohno podczas poszukiwania sposobów na usprawnienie procesów w Toyocie. Wiele pozostałych rodzajów marnotrawstwa wyszczególnionych przez Ohno, w tym nadprocesowość, nadprodukcja i zapasy, jest bezpośrednią przyczyną lub bezpośrednim skutkiem tego rodzaju marnotrawstwa. W wypadku przenośników taśmowych ustawiona prędkość sprawia, że podczas pracy nad produktem szybsze procesy muszą oczekiwać na swoją kolej. To zaś może inicjować przyspieszanie wolniejszych procesów, w wyniku czego powstają wady, co ponownie prowadzi do oczekiwania, podczas gdy pracownicy usiłują naprawić problem. Wreszcie, ponieważ system nie jest w stanie szybko przystosować się do zmieniającego się zapotrzebowania, może to w niedługim czasie doprowadzić do zbyt dużych zapasów i nadprodukcji. Podobne problemy powstają w branżach niezwiązanych z produkcją, np. w poczekalniach szpitali, kiedy to długi czas oczekiwania wpływa bezpośrednio na jakość opieki nad pacjentem. Nawet w branżach zajmujących się wyłącznie informacją stagnacja w zakresie przetwarzania i podejmowania decyzji jest jak wirtualny przenośnik taśmowy łączący sale konferencyjne, biura i komputery
Zbędny ruch
Marnotrawstwo w zakresie ruchu odnosi się do ruchu osób niewytwarzających wartości dodanej. Może on być tak duży, jak przejście przez cały zakład pracy, lub tak niewielki, jak szybki ruch nadgarstka. A gdyby tak jedna osoba była w stanie przeprowadzić cały montaż w miejscu i czasie, w których jest on potrzebny? Co by było, gdyby pracownik o szerokich kwalifikacjach, przeszkoleniu i sposobie myślenia, odpowiednich do udoskonalenia procesu i przekazania innym wiedzy o nim, mógł wykonać wszystkie niezbędne zadania? To jest właśnie model wdrożony przez Yamadę w firmach Sanyo i Canon. Jeżeli niewielka komórka produkcyjna ma ukończyć cały proces w potrzebnym do tego czasie, osoby pracujące w tej komórce muszą posiadać szczegółową wiedzę na temat wykonywanych przez siebie zadań. Jeżeli stwierdzony zostanie zbędny ruch, osoby pracujące w podobnych procesach mogą dzielić się pomysłami na poprawę tej sytuacji. Doprowadzi to do lepszej standaryzacji zadań. Osoby niezaznajomione jeszcze z danym procesem będą w stanie szybko nauczyć się standardów, a w miarę nabywania doświadczenia – wnosić wkład w ulepszanie sposobu wykonywania pracy.
Zbędny transport
Zbędny transport oznacza każde niepotrzebne przemieszczanie materiałów, informacji lub produktów, do którego wykorzystywany jest sprzęt, taki jak podnośniki widłowe czy wózki paletowe. Można go łatwo zaobserwować w wypadku liniiprodukcyjnych starego typu, w których produkty w toku i zapasy są przemieszczane z jednej części fabryki do innej, jak też w wypadku większych łańcuchów dostaw, w których niesprzedane towary zalegają na półkach i w magazynach. Może to zabrzmieć bardzo przemysłowo, ale wystarczy pomyśleć, jak dużo informacji „transportuje się” w każdej branży usługowej. Bez względu na to, czy używasz wózka widłowego, komputerowego serwera albo tuszu i papieru, ukończona i nieukończona praca może szybko przepaść w tym zamieszaniu.
Jak łatwo zauważyć, każdy z wyżej wspomnianych rodzajów marnotrawstwa występuje w specyficznych okolicznościach. To m.in. dlatego metodę Yamady tak łatwo zrozumieć i zastosować. Stagnacja pojawia się między procesami w strumieniu wartości. Zbędny ruch zachodzi w ramach procesów, a zbędny transport odbywa się na terenie obiektu. Spojrzenie na wszystko na tych trzech poziomach po raz kolejny pokazuje znaczenie walki ze stagnacją, ponieważ przybiera ona formę podziału pracy. Usunięcie tych podziałów ma największy wpływ na cały strumień wartości. Kiedy usunie się stagnację, można zapobiec wielu innym wynikającym z niej rodzajom marnotrawstwa.
Niektóre branże mają trudności z odejściem od podziału pracy. Nawet nowoczesne linie produkcyjne Toyoty wciąż pozostają pewną formą przenośnika taśmowego. Jeżeli nie uda się od razu wyeliminować tego ugruntowanego systemu, należy mieć świadomość marnotrawstwa, do jakiego może on prowadzić. Trzy kategorie marnotrawstwa zaproponowane przez Yamadę ilustrują wszystkie potencjalne rodzaje marnotrawstwa bez konieczności stosowania długiej listy kategorii.
Proponowany przez Ohno podział na siedem rodzajów marnotrawstwa jest często krytykowany za zbyt dużą koncentrację na koncepcjach z zakresu produkcji, ale nietrudno zauważyć, że podział Yamady można zastosować do każdego rodzaju pracy. Jeżeli jakikolwiek proces jest nieelastyczny, charakteryzuje się nadmiernym ruchem i podziałem na zbyt wiele osób, prowadzi do marnotrawstwa.
Niematerialny przenośnik taśmowy
Wyobraźmy sobie, że pracujesz w biurze. Jak często dokumenty są przekazywane kolejnym osobom, podczas gdy wystarczyłaby jedna osoba do ich wypełnienia? Czy wyznaczasz osoby nadające tempo poszczególnym operacjom? Czy stosujesz podział zadań? Ważne pytanie brzmi: „Czy jedna osoba może wykonać zadanie – cały cykl – od początku do końca?”. Jeżeli odpowiedź brzmi „nie”, posługujesz się niematerialnymi przenośnikami taśmowymi. Prawdę mówiąc, widzę przenośniki taśmowe wszędzie i w każdej organizacji, którą odwiedzam. Nauczono nas nie zauważać, że z nich korzystamy. Wszystko jest pewną formą przenośnika taśmowego: komunikacja, a nawet procesy przekazywania problemu na wyższy poziom kompetencji. Jak często telefony od klientów przekazuje się między oddziałami firmy, marnując czas pracowników i wywołując frustrację klientów z powodu konieczności oczekiwania na odpowiedź. Automatyczne serwisy telefoniczne to przykład niematerialnego przenośnika taśmowego, który wszyscy dobrze znamy. Ile razy jako klient, chcąc zadać jedno proste pytanie, musiałeś przebrnąć przez sieć różnych menu, zanim mogłeś porozmawiać z kimś, kto zna odpowiedź? Przez tego rodzaju menu trzeba przechodzić zgodnie z właściwym dla nich tempem, a nie zgodnie z tempem klienta czy nawet pracowników. Nie zostały one zaprojektowane w celu zaspokojenia potrzeb klienta – zaprojektowano je z myślą o redukcji kosztów dzięki przeniesieniu ciężaru na klienta. Oto dobry przykład cięcia kosztów, któremu bardzo daleko do Lean Management. To niefortunny przykład wykorzystania modelu produkcji masowej tam, gdzie automatyzacja nie dotyczy produkcji.
Zobacz również