ZARZĄDZANIE
Systematyczne dążenie do doskonałości
Ciągłe doskonalenie od dawna jest jednym z podstawowych sposobów na osiąganie lepszych wyników i zapewnienie konkurencyjności w branży FMCG. Międzynarodowe korporacje zbudowały wewnętrzne systemy specjalistów – niekiedy również metodologie – którzy wdrażają i propagują kulturę ciągłego doskonalenia.
Data publikacji: 08.02.2022
Data aktualizacji: 01.11.2023
Podziel się:
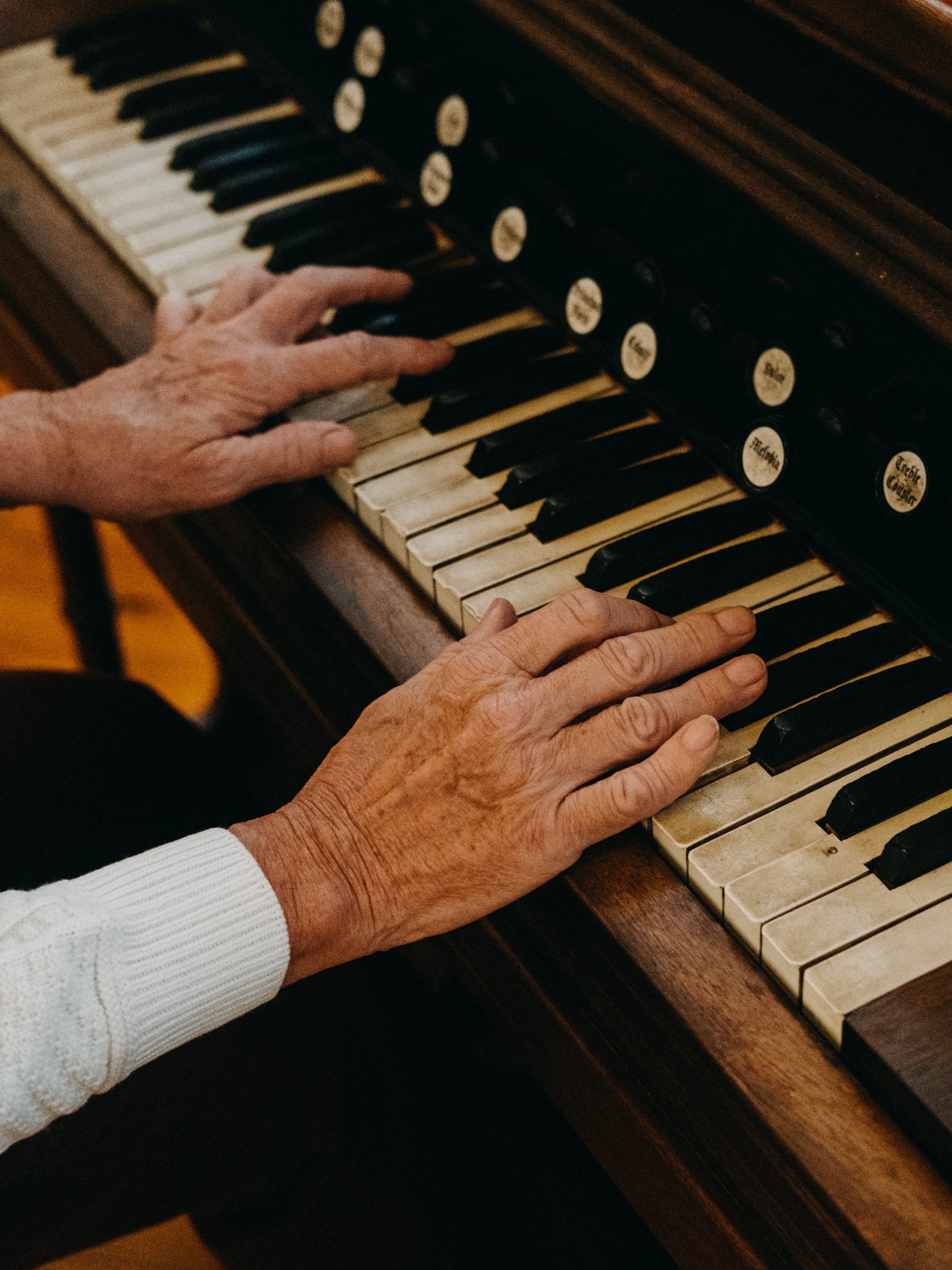
Około 20 lat temu w Nestlé wdrożono system Nestlé Continous Excellence (NCE), który łączy praktyki ciągłego doskonalenia znane z metodologii Lean, Six Sigma i IWS z wartościami Nestlé. Metodologia, a właściwie Struktura NCE, to model zrównoważonego rozwoju fabryki w działach produkcyjnych oraz działach wspierających. Model NCE (Rys. 1) opiera się na systematycznym dążeniu do doskonałości produkcyjnej przez eliminację strat, transformację miejsca pracy oraz budowanie kompetencji w działach produkcji, utrzymania ruchu, jakości, bezpieczeństwa i logistyki. W jego fundamentach widnieje:
- compliance – zgodność prawna i korporacyjna,
- leadership development – rozwój kompetencji liderskich w firmie,
- goal alignment – zapewnienie zbieżności celów na wszystkich szczeblach organizacji.
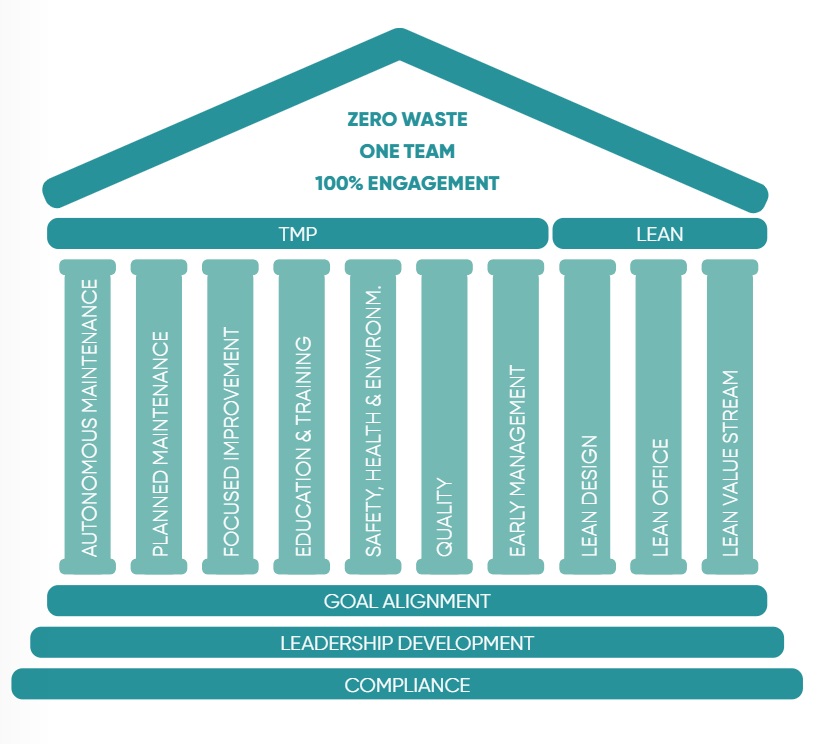
Rys. 1. Model NCE
Opisanie całego modelu wraz z systemami spotkań, organizacji działu, ze zbieżnością celów czy strukturą filarów kompetencji to materiał na kilkanaście artykułów, aby więc najlepiej zobrazować wdrożenie systemu Continous Excellence w Nestlé, posłużę się wybranymi przykładami zaimplementowanych narzędzi. Obrazowe porównanie, zapożyczone z działów związanych ze sprzedażą, to przedstawienie systemu NCE jako kombinacji farmingu i huntingu.
- Farming – działania mające na celu organiczne zwiększenie kompetencji i rozwijanie systemu standardów, w którym, tak jak w wypadku uprawiania roli, wzrost jest powolny, ale stabilny.
- Hunting – łapiemy za strzelbę i eliminujemy straty, polując na „grube zwierzę”.
Metodologia NCE łączy aktywności związane z polowaniem na straty (hunting) ze stopniowym budowaniem kompetencji i systemów (farming). Opisując, jak metodologia wygląda na co dzień w fabryce, skupię się na dwóch najbliższych mi filarach. Pierwszy, autonomous maintenance, jest przykładem farmingu, drugi, focused improvement – huntingu.
Autonomous maintenance w Nowej Wsi Wrocławskiej
Autonomous maintenance (AM) to aktywności, które zwiększają samodzielność (czyli autonomię) pracowników produkcji, aby mogli we własnym zakresie zadbać o park maszynowy, a w rezultacie doprowadzić do poprawy wyników oraz redukcji kosztów. Głównymi aktorami w tym systemie są członkowie grupy AWG, w której skład wchodzą operatorzy, liderzy produkcji oraz kierownicy zmian. Grupa obejmuje pełne właścicielstwo nad danym obszarem produkcji, dbając o implementację metodologii, rozwój kompetencji, a w rezultacie osiągnięcie wyników produkcyjnych z zakresu wydajności i jakości.
Członkowie zespołu są odpowiedzialni za wdrożenie systemów, które pozwalają na ustandaryzowanie podstawowych aspektów procesu produkcyjnego. Kluczowe systemy to:
5S (sortowanie, systematyka, sprzątanie, standaryzacja, samodyscyplina) – znany każdemu czytelnikowi system, od którego rozpoczyna się wdrożenie metodologii total productive maintenance. Pozwala na transformację miejsca pracy, ma pozytywny wpływ na bezpieczeństwo i jakość oraz wypracowuje podstawowe nawyki „właścicielstwa” obszaru. Właścicielami systemu są u nas inżynierowie produkcji, a za zgodność ze standardami odpowiadają kierownicy zmian.
CIL (czyszczenie, inspekcja, lubrykacja) – standard produkcyjny wskazuje krytyczne punkty procesu technologicznego, które należy regularnie czyścić i dokonywać ich inspekcji. Standard ma na celu uniknięcie zatorów oraz wydłużenie cyklu życia komponentów. Systemem zarządzają inżynierowie. Ważne jest jednak, aby operatorzy także uczestniczyli w procesie tworzenia standardu. Na naszym obszarze CIL (po kilku cyklach optymalizacji) trwa 23 minuty. Standard jest rewidowany cztery razy w roku na podstawie najbardziej krytycznych przestojów – w ten sposób możemy napędzać proces ciągłego doskonalenia przez nieustanną rewizję tego podstawowego narzędzia.
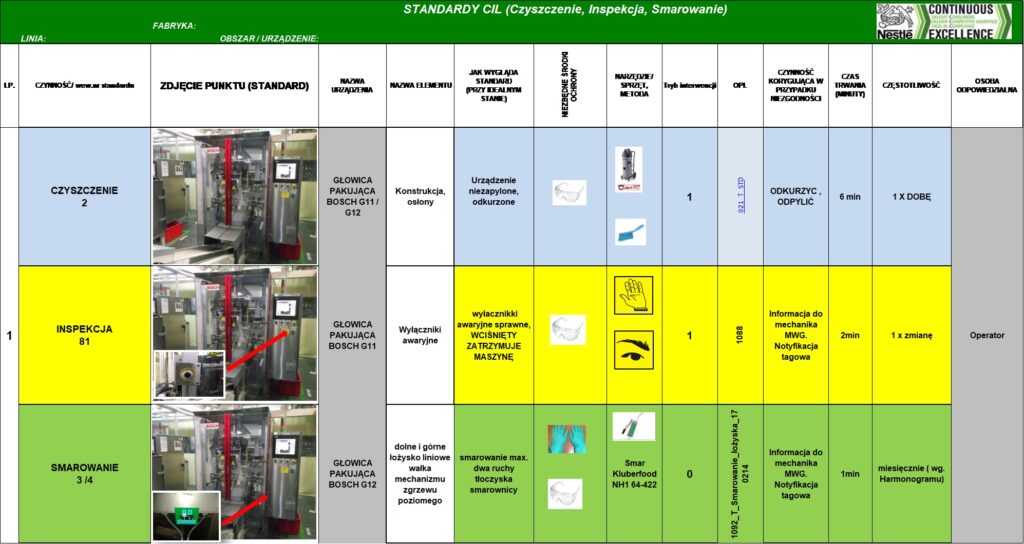
Rys. 2. Standard czyszczenia, inspekcji i lubrykacji
Centrowanie
Metoda polegająca na standaryzacji optymalnych parametrów procesu produkcyjnego: temperatur, ciśnień czy ustawień mechanicznych. Dążymy do wykluczenia możliwości regulacji, czyli popełnienia błędu (poka yoke). Jeśli potrzebna jest zmiana parametrów zależnie np. od formatów, wyznaczamy optymalne nastawy i regularnie je kontrolujemy.
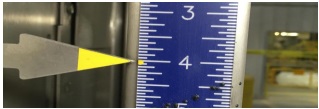
Fot. 3. Przykład centrowania z zaznaczonymi optymalnymi pozycjamiTagowanie – system zawieszek
Narzędzie, które pozwala operatorom na zgłaszanie wszelkich nieprawidłowości na linii produkcyjnej. Operatorzy mają do dyspozycji zawieszki w dwóch kolorach. Zależnie od tego, czy nieprawidłowość może być rozwiązana przez dział utrzymania ruchu lub przez nich samych, używają czerwonych lub niebieskich zawieszek, które oznacza się jedną z siedmiu kategorii „anomalii”: bezpieczeństwo, jakość, warunki bazowe, miejsca trudno dostępne, źródła zanieczyszczeń, 5S, błędy procesowe.
Na podstawie zebranych tagów liderzy AWG organizują regularne spotkania między działami produkcji i działem technicznym, aby nadać priorytet oraz zaplanować naprawy eliminujące wykryte niezgodności.

Fot. 4. Tag wystawiony na odpryski farby na silniku
Transfer kompetencji technicznych
Kto wie więcej o maszynach niż operatorzy, którzy na nich pracują? Doświadczeni operatorzy poradzą sobie ze wszystkimi regulacjami i drobnymi naprawami na swoich obszarach. Dlatego logicznym kierunkiem w ewolucji jest wyposażanie ich w coraz wyższy poziom wiedzy technicznej po to, aby mogli samodzielnie radzić sobie z jeszcze większą liczbą wyzwań, wykonywać regulacje, przezbrojenia, ale także usuwać awarie i regenerować części eksploatacyjne.
Wachlarz kompetencji jest ogromny, a szkolenia zajmują często wiele tygodni. Dlatego kluczowa jest dobra priorytetyzacja, aby najpierw skupić się na aspektach, które przyniosą nam najwięcej korzyści. Przy priorytetyzacji patrzymy na trzy aspekty:
- liczba przestojów, jakie moglibyśmy zredukować, mając większą wiedzę techniczną,
- koszt komponentów, których awarii moglibyśmy uniknąć,
- potencjalny czas zaoszczędzony przez mechaników.
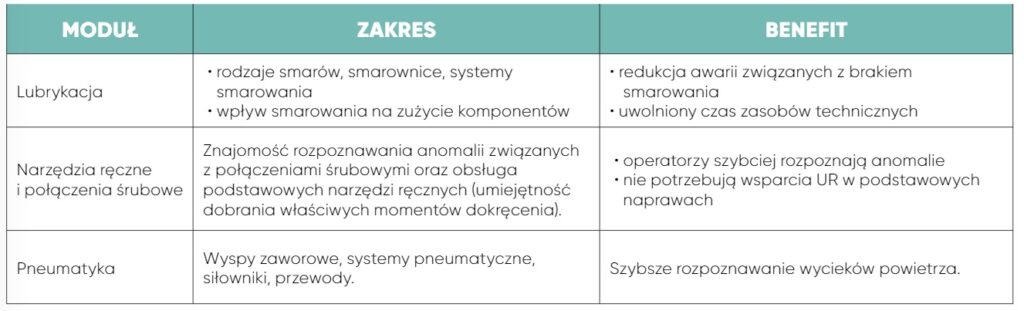
Tab. 1 Moduły techniczne wdrożone w Nestlé
W ramach rozwijania kompetencji technicznych operatorów osiągnęliśmy namacalne zyski z przenoszenia zadań technicznych:
- 40 proc. prac utrzymania ruchu podczas planowanych przeglądów wykonują operatorzy,
- 100 proc. przezbrojeń wykonują operatorzy,
- nieplanowane przestoje zredukowaliśmy o 18 proc. (przede wszystkim dlatego, że nie ma potrzeby oczekiwania na interwencję UR).|
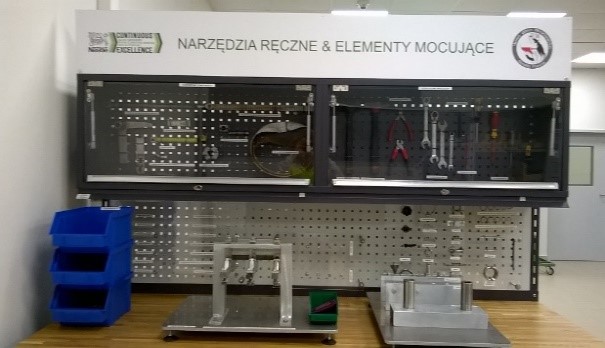
Fot. 5. Stanowisko dydaktyczne do modułu technicznego
Nie wszystkie problemy produkcyjne można rozwiązać za pomocą solidnych standardów oraz kompetencji. Nawet w najbardziej kontrolowanych procesach zdarzają się zakłócenia, których pochodzenia, w pierwszym momencie, nie znamy. Z pomocą przychodzi więc filar focused improvement (FI) – czyli hunting ciągłego doskonalenia.
Hunting – metodologia focused improvement
W metodologii FI skupiamy się na codziennym rozwiązywaniu problemów oraz podejściu strategicznym (cyklicznym). Podstawowym narzędziem w codziennych problemach jest „Go, See, Think and Do” (GSTD), które pozwala na szybką analizę problemu i dojście do przyczyny źródłowej za pomocą narzędzia 5 WHY. W innych firmach nazywa się je też „See, Think, Do, Care” lub po prostu „Problem Solvingiem”. Założeniem jest wykonanie szybkiej analizy na gemba. Całość projektu nie powinna zajmować dłużej niż 72 godziny. Stosujemy ją przede wszystkim do pojedynczych problemów jakościowych występujących na liniach pakujących, dzięki czemu upewniamy się, że dany problem już nigdy się nie powtórzy.
Grubszym kalibrem jest cykl strategicznego rozwiązywania problemów, nazywany potocznie cyklem focused improvement.
Cykl focused Improvement
Usystematyzowany proces, który pozwala na regularny przegląd największych przestojów oraz ich uwzględnienie przez narzędzia ciągłego doskonalenia. Cykl FI dzieli się na etapy analizy strat, implementacji projektów oraz fazy kontroli.
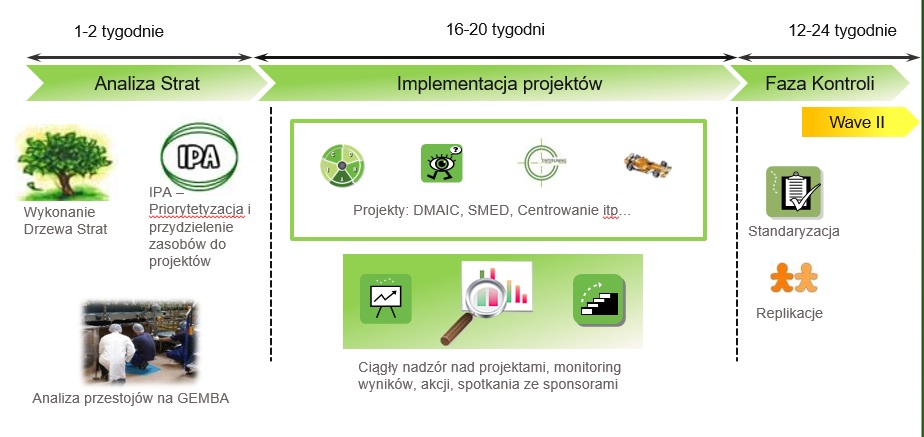
Rys. 3. Cykl focused improvement
Faza analizy strat – korzystamy w niej z tzw. Drzewa Strat, czyli podsumowania wszystkich strat finansowych z ostatniego kwartału (przestoje, części maszyn, defekty jakościowe) i konwertujemy je na wspólną jednostkę – koszt finansowy straty. Nie bazujemy tylko na suchych danych systemowych – podczas trwania tej fazy konieczna jest obecność na linii, aby zweryfikować poprawność danych systemowych oraz dokonać prawidłowego rozpoznania wstępnego problemu. Owocem fazy analizy strat jest lista projektów usprawnieniowych wraz z przypisanymi zasobami projektowymi.
Faza implementacji projektów – po zakończeniu analizy uruchamiamy projekty usprawnieniowe. Korzystamy z całej puli metodologii – od prostych modyfikacji technicznych przez standaryzacje i SMED aż po DMAIC czy centrowanie. Prowadzimy zazwyczaj od 20 do 30 projektów na każdy cykl. Spośród nich wybieramy 10 kluczowych projektów, które śledzimy na naszym cotygodniowym spotkaniu WOR.
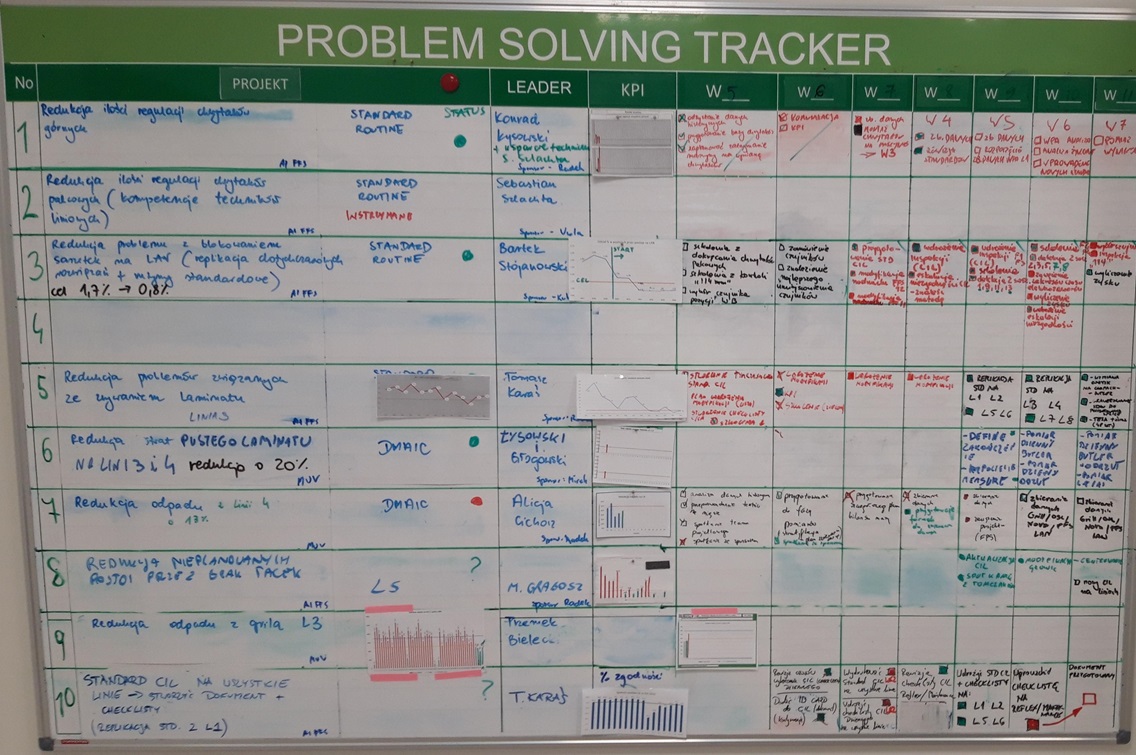
Fot. 6. Tablica projektowa
Priorytetowe projekty monitorujemy pod kątem kluczowych akcji z zeszłego tygodnia, kluczowych akcji na ten tydzień oraz wskaźnika projektu.
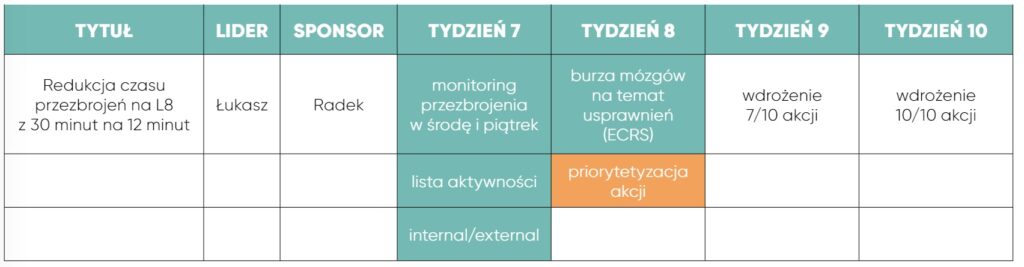
Tab. 2. Przykład rozplanowania akcji projektowych
W zależności od fazy projektu weryfikujemy skuteczność wprowadzonych akcji na podstawie osiągniętego wyniku. Przykładowy KPI projektowy jest zamieszczony poniżej. O ile w fazie analiz strat nie spodziewamy się pozytywnego wpływu na wskaźnik, o tyle w fazie implementacji kryterium sukcesu jest osiągnięcie oczekiwanego rezultatu. Dobrą praktyką jest monitoring osiągniętych wyników przez dłuższy okres, aby zobaczyć, czy problem nie powraca – na tym skupiamy się w fazie kontroli.
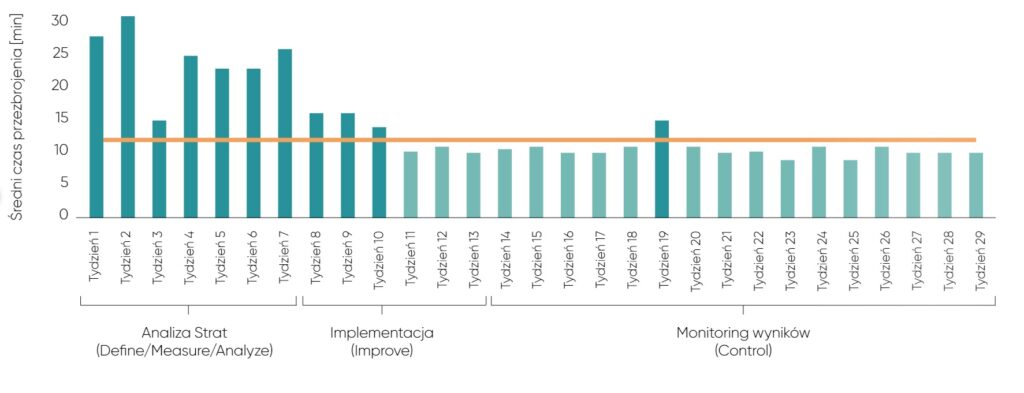
Wyk. 1. Wskaźnik projektu wraz z opisem faz projektowych
Nie tylko dział produkcji
Nie tylko dział produkcji
W powyższych przykładach skupiłem się przede wszystkim na zastosowaniu narzędzi NCE na produkcji. Aby osiągnąć wizję „niezawodnej i zwinnej produkcji”, ważny jest równoczesny rozwój wszystkich działów w fabryce.
Dział utrzymania ruchu przechodzi ewolucję z time based maintenance na condition based maintenance oraz predictive maintenance. Jego rola staje się bardziej ekspercka z racji tego, że duża cześć aktywności została przeniesiona na produkcję. Dział Logistyki jest motorem napędowym aktywności Lean – mapuje wszystkie przepływy w fabryce, aby osiągnąć oszczędności w procesach end to end.
Dział Jakości wykorzystuje narzędzia typu jidoka, Q-matryca, optymalizuje standardy jakościowe, starając się zwolnić czas operatorów, aby mogli poświęcić więcej czasu ciągłemu doskonaleniu.
Największym wyzwaniem w kwestii ciągłego doskonalenia w naszej fabryce jest znalezienie na to czasu pośród codziennego gaszenia pożarów. Trudno usiąść do analizy 5 WHY, gdy na naszym obszarze brakuje surowców lub mamy jednocześnie trzy awarie. Jeżeli jednak nie poświęcimy czasu na rozwiązywanie problemów, będą się one powtarzać i nawarstwiać – nie ma więc innej opcji jak rozsądnie inwestować swój czas.
Radosław Miszewski
Artykuł ukazał się w nr 5(35) październik-listopad 2021 czasopisma „Production Manager”.
Zobacz również