ZARZĄDZANIE
Karykatura lub autoportret – meandry Lean
Wdrożenie koncepcji szczupłej produkcji (lean manufacturing/lean production) jest ambitnym celem dla wielu przedsiębiorstw. Pokażę więc, jak się to robi w Toyocie i dlaczego ten sposób może nie sprawdzić się w twoim wypadku. Napiszę również, jak NIE NALEŻY wdrażać tej koncepcji. Postaram się ponadto zwrócić twoją uwagę na najczęściej popełniane błędy. Na zakończenie zechcę przedstawić możliwości drzemiące w przejściu na szczupłą produkcję.
Data publikacji: 25.01.2021
Data aktualizacji: 21.11.2023
Podziel się:
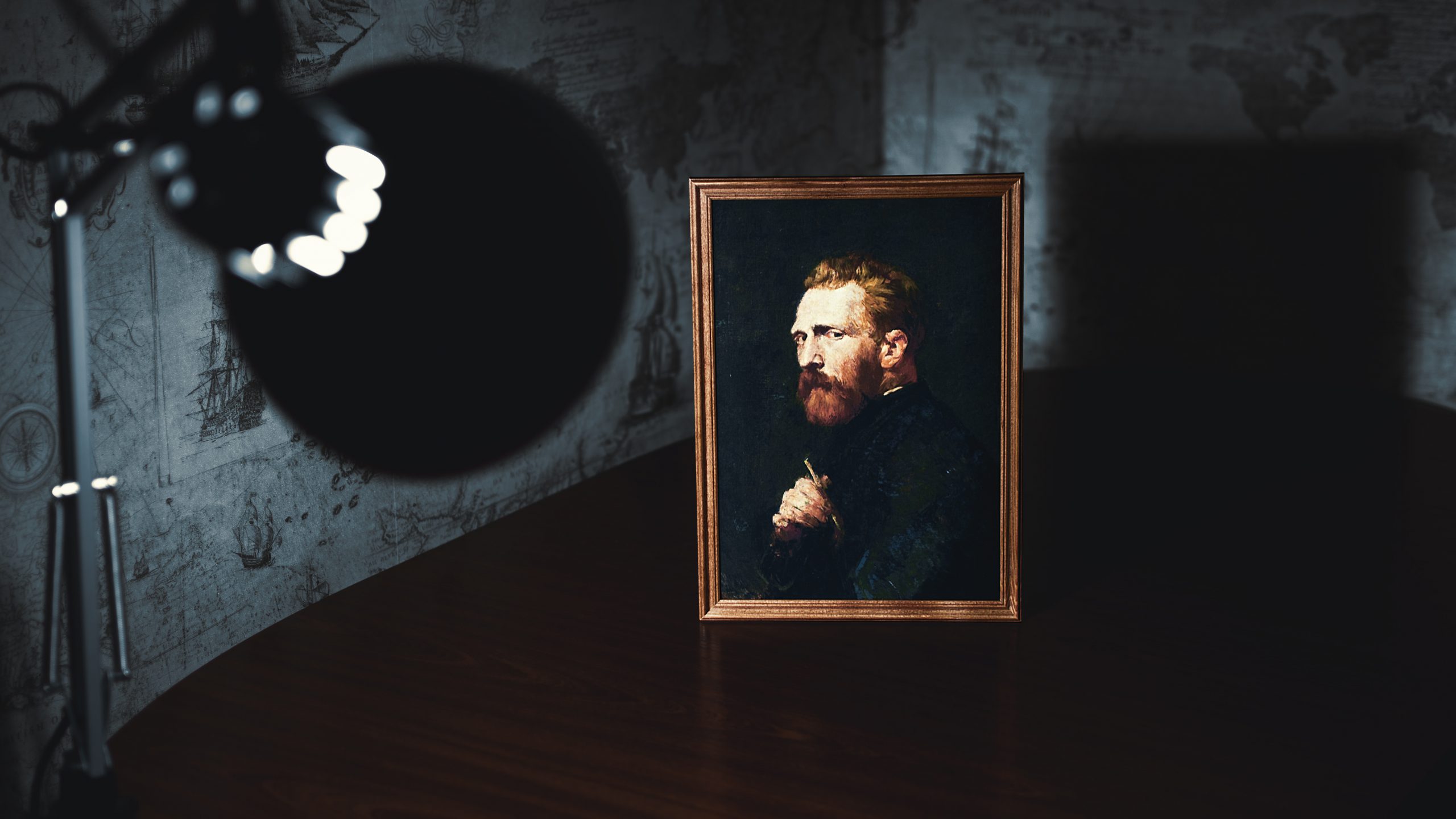
Aby przetrwać, firmy muszą się stale doskonalić. Szczupła produkcja może pomóc w ciągłym doskonaleniu, dlatego wiele organizacji dąży do tego, by stać się „szczupłym przedsiębiorstwem”. Pytanie brzmi: jak się to robi? Jak przejść na szczupłą produkcję lub, ogólnie mówiąc, zarządzać zmianą? Chciałbym opowiedzieć o tym, czego potrzebuje firma, aby rozpocząć drogę do przeobrażenia się w „szczupłe przedsiębiorstwo”. Ostrzegam, że nie jest to łatwe i naprawdę wymaga dużego wsparcia na wszystkich szczeblach firmy.
Czym jest szczupła produkcja?
Aby przejść na szczupłą produkcję, trzeba wiedzieć, co to pojęcie znaczy. W obiegu funkcjonuje wiele definicji szczupłej produkcji, choć, moim zdaniem, żadna z nich nie jest doskonała (z wyjątkiem tej, zgodnie z którą „Lean” to inne słowo na określenie Systemu Produkcyjnego Toyoty – nie jest to jednak zbyt przydatne na potrzeby tego artykułu). Często określenie to redukowane jest do zestawu narzędzi, począwszy od kanban, a skończywszy na SMED. Ale odbiega to daleko od tego, czym szczupła produkcja jest naprawdę. Uważam bowiem, że szczupła produkcja to kultura.
Rodzi to kilka problemów. Po pierwsze, jaka jest definicja kultury? Sformułowanie takiej definicji jest niemal niemożliwe. Jak definiuje się kulturę twojej narodowości? Każda próba prowadzi wkrótce do posługiwania się frazesami, a w rezultacie staje się obraźliwa. Stany Zjednoczone: hamburgery, patriotyczny ferwor i broń? Niemcy: Wurst, piwo i Nein? Myślę, że najlepiej będzie nie brnąć dalej, jeżeli nie chcę obrazić zbyt wielu czytelników. Podsumowując, bardzo trudno jest zdefiniować, czym jest kultura – w tym również kultura szczupłej produkcji.
Po drugie, jak zmierzyć kulturę? Aby wprowadzać ulepszenia, musimy wiedzieć, w jakim miejscu się znajdujemy i ile udało się już ulepszyć. Posłużmy się raz jeszcze przykładem twojej narodowości. W skali od 1 do 100, w jakim stopniu jesteś twoją narodowością? Jakich kryteriów użyłeś do zmierzenia powyższej cechy? Również tym razem ilościowy pomiar kultury okazuje się niemal niemożliwy, mimo że funkcjonuje wiele opinii na temat jej jakości.
I ostatni problem – jak zmienia się kulturę? Bardzo podchwytliwe pytanie. Jednak w wypadku szczupłej produkcji sprawa jest nieco łatwiejsza niż próba zmiany kultury twojej narodowości. Kultura organizacyjna jest często mniej zróżnicowana niż kultura danego narodu. Wchodząc np. do przedsiębiorstwa motoryzacyjnego, można zauważyć, że sposób myślenia pracowników jest bardziej jednolity, niż można byłoby to zaobserwować w wypadku losowo wybranych osób. Wciąż jednak jest on dość różnorodny, więc zadanie do wykonania nie jest łatwe.
Jak się to robi w Toyocie?
Zanim omówimy sposoby zmiany kultury organizacyjnej, przyjrzyjmy się podejściu wdrożonemu przez Toyotę. Na początku kultura tego przedsiębiorstwa miała charakter firmy rodzimej. Dlatego Toyota nie potrzebuje zmieniać całej swojej kultury organizacyjnej. Jednak firma często otwiera nowe zakłady produkcyjne – wiele z nich za granicą – którym musi przekazywać swoją kulturę, w tym System Produkcyjny Toyoty.
Sposób Toyoty to transfery sporej liczby pracowników między zakładami. Duże grupy z nowej lokalizacji wysyłane są do Japonii, gdzie zostają zanurzone w kulturze Toyoty. Toyota wysłała już setki pracowników do Japonii, aby nauczyć ich koncepcji szczupłej produkcji. Dotyczy to nie tylko osób na wysokich stanowiskach, ale również wielu pracowników wykonujących swoje obowiązki na pierwszej linii. Pracownicy pracują w japońskim zakładzie Toyoty, żeby poznać i zrozumieć sposób funkcjonowania przedsiębiorstwa. Pobyt taki trwa zazwyczaj cztery tygodnie lub dłużej. Kiedy pracownicy wracają do swojego kraju, przyjeżdża z nimi grupa pracowników z Japonii. Większość krajowych kierowników w nowym zakładzie ma swój japoński „cień” – coacha i mentora w zakresie sposobu wykonywania obowiązków. Toyota wysyła setki coachów z Japonii do innych lokalizacji. Wielu japońskich pracowników pierwszej linii pracuje obok zagranicznych współpracowników, również w celu przekazania nowemu zakładowi własnej kultury organizacyjnej.
Nawet w tym wypadku strategia ta nie zawsze działa. Między 2000 a 2010 r. Toyota prawdopodobnie przeprowadziła zbyt szybką ekspansję, co mogło być przyczyną skandalu z zacinającym się pedałem gazu w samochodach tej marki. Dyrektor zarządzający firmy, Akio Toyoda, przyznał, że rozwój działalności Toyoty „mógł być zbyt szybki” (ale mógł bardziej się zatroszczyć o jego stronę techniczną). Jednak ogólnie rzecz ujmując, podejście Toyoty działa. Zagraniczne zakłady Toyoty często charakteryzuje lepsza jakość i większa wydajność niż zakłady rodzimego konkurenta.
Słynnym przykładem jest fabryka NUMMI w miejscowości Fremont w stanie Kalifornia, przedsiębiorstwo joint venture z udziałami General Motors i Toyoty. Zakład na początku należał do koncernu General Motors i był najgorszym ze wszystkich jego zakładów. Nawet związki zawodowe tak twierdziły. Kultura organizacyjna była pełna wrogości i wszyscy czuli się nieszczęśliwi. Wreszcie zakład zamknięto. Dwa lata później został on ponownie otwarty wspólnie z Toyotą jako fabryka NUMMI. Nawet pracownicy zatrudnieni w fabryce to przeważnie byli pracownicy General Motors. Wiele osób martwiło się, że sytuacja wrogiej kultury może się powtórzyć. Jednak Toyocie udało się odmienić sytuację, sprawiając że fabryka NUMMI stała się dla pracowników powodem do dumy. Jakość i wydajność dorównywały japońskim zakładom, będąc nieporównywalnie lepsze niż każdy inny zakład General Motors. Skala absencji pracowników spadła z 20 proc. do 3 proc.
Dlaczego podejście Toyoty może się nie sprawdzić
Jeżeli czytasz ten artykuł, próbując się dowiedzieć, jak przekształcić własne przedsiębiorstwo, może wydawać się to niemożliwe. Potrzebny byłby zakład mający tego rodzaju kulturę, od którego można by się jej uczyć. Potrzebne byłyby setki osób na różnych szczeblach, które byłyby głęboko zakorzenione w kulturze szczupłej produkcji. Nie mam tu na myśli znajomości metody SMED czy kanban lub bycia kierownikiem projektu Six Sigma. Mam na myśli to, że szczupła produkcja powinna stać się stylem bycia, powietrzem, którym się oddycha. Z twojej perspektywy wygląda to jak zwykłe oszustwo, bo Toyota tak ma, a ty nie. Toyota wysłała 600 pracowników z NUMMI do Japonii na jednomiesięczne szkolenie i 400 coachów z Japonii do NUMI na wiele miesięcy. Jasno widać, że nie jest to realna opcja dla ciebie.
Zanim przejdę do omówienia możliwości, które rzeczywiście masz, a nawet do pokazania przykładu, jak tego nie robić, chciałbym opisać działania podejmowane przez Toyotę w celu przekazania swojej kultury. Mówimy tu o wielu większych grupach odwiedzających zakłady Toyoty w Japonii. Sześćset osób ze Stanów Zjednoczonych spędza cztery tygodnie w Japonii. Mimo że pracują i generują wartość, jest ona prawdopodobnie mniejsza, niż byłoby to w sytuacji, gdyby pracowali standardowo w swoim kraju. Potrzebują oni też coachingu, mentoringu i szkoleń prowadzonych przez japońskich pracowników. Dotyczy to również pracowników pierwszej linii, którzy uczą swoich zagranicznych kolegów. Z pewnością wiesz, że kiedy zatrudniasz nowego pracownika, przez kilka pierwszych miesięcy koszty tej operacji będą przewyższać jej zyski. Często wydajność osiąga poziom porównywalny z poziomem doświadczonego pracownika po około sześciu miesiącach zatrudnienia. Sytuacja jest trochę podobna w wypadku szkolenia zagranicznych pracowników Toyoty w Japonii.
Szacuję, że uwzględniając dodatkową pracę, jaką oznacza to dla gospodarzy w Japonii, sytuacja jest podobna do tej, kiedy przez miesiąc zatrudniasz 600 pracowników otrzymujących wynagrodzenie, ale nieprzynoszących korzyści – a wszystko to podczas wyjazdu służbowego do Japonii. Następnie, kiedy dodatkowi japońscy pracownicy i kierownicy są wysyłani do innego kraju, aby pomóc tamtejszym pracownikom, ich wydajność również nie jest tak wysoka, jak we własnym kraju. Zapewnienie osób doradzających dla większości kierowników jest wyjątkowo kosztownym przedsięwzięciem. Czterystu japońskich coachów przebywało w Stanach Zjednoczonych przez wiele miesięcy, a nawet przez ponad rok.
Wystarczy, że policzysz w pamięci: miesięczne wynagrodzenie dla 600 osób, połowa rocznego wynagrodzenia dla kolejnych 400 osób, z których wiele to dobrze opłacani członkowie kadry kierowniczej, plus koszty podróży zagranicznych dla wszystkich tych osób – całkiem pokaźna kwota! Nawet przy dostępie do 400 ekspertów z zakresu szczupłej produkcji nie mógłbyś sobie na to pozwolić. Te obliczenia mają na celu pokazanie, jak ważne jest dla Toyoty przekazanie nowym zakładom swojej kultury organizacyjnej. Tak – również Toyotę sporo to kosztuje!
Dlatego potrzebujesz mniej kosztownych możliwości. Jest to możliwe, nawet jeżeli potrwa to dłużej. Będzie to jednak spora inwestycja, pod względem zarówno czasu, jak i nakładów finansowych. Jeżeli zostanie przeprowadzona we właściwy sposób, zwróci się dzięki zwiększeniu jakości i wydajności. Potraktuj to jak duży projekt rozwojowy. Oczywiście, najważniejszym zagadnieniem jest dla ciebie cena i możliwość znalezienia konsultantów oferujących „tanie odchudzanie”: „Wystarczy, że wynajmiesz dwóch ekspertów w dziedzinie szczupłej produkcji, najlepiej świeżo upieczonych absolwentów, ponieważ ich usługi są tańsze, i zlecisz im, na pół etatu, zadanie przekształcenia twojej korporacji posiadającej 150 oddziałów na całym świecie”. Jeżeli w to wierzysz, nie jestem w stanie ci pomóc.
Ale pokażę ci lepsze sposoby w moich kolejnych artykułach. Ponieważ jestem zwolennikiem uczenia się na błędach – najlepiej na błędach innych osób – w pierwszej kolejności pokażę, jakie sposoby są NIESKUTECZNE.
Jak NIE NALEŻY przechodzić na szczupłą produkcję
Przemysł zna wiele przykładów porażek wdrażania szczupłej produkcji. Większość z nich jest znana tylko osobom wtajemniczonym, a wiedza ta najczęściej objęta jest tajemnicą służbową. Dlatego wiele przypadków niepowodzeń i firm mogę omówić, posługując się teoretycznymi przykładami. Istnieje jednak jeden szeroko opisywany (również w mojej książce „Faster, Better, Cheaper”) przykład, o którym mogę powiedzieć. Koncern General Motors przeszkolił wielu pracowników w zakresie szczupłej produkcji u samego źródła, za pośrednictwem NUMMI – przedsiębiorstwa joint venture z Toyotą, a następnie wszystko zaprzepaścili. Mieli kilkudziesięciu pracowników na średnim szczeblu zarządzania przeszkolonych w zakresie szczupłej produkcji i setki pracowników wierzących i ufających tej koncepcji, nie byli jednak w stanie przekazać tej wiedzy pozostałym zakładom. To raczej podręcznikowy przykład na to, jak tego NIE ROBIĆ. Wiele innych firm również poniosło porażkę, próbując przejść na szczupłą produkcję, jednak żadna z nich nie miała tak dobrej pozycji startowej jak General Motors.
Sytuacja początkowa – NUMMI
Na początku lat 80. Toyota zamierzała otworzyć swój pierwszy duży zakład w Stanach Zjednoczonych. Aby ograniczyć ryzyko, zdecydowano się na utworzenie przedsiębiorstwa joint venture. W pierwszej kolejności zwrócono się do Forda, ponieważ w przeszłości Toyota sporo się od tej firmy nauczyła. Ford jednak odmówił (i prawdopodobnie żałował tego później, gdy koncepcja szczupłej produkcji zyskała na popularności). Następnie zwrócono się do General Motors, czego rezultatem było utworzenie przedsiębiorstwa New United Motor Manufacturing Inc. w miejscowości Fremont w stanie Kalifornia, które lepiej znane jest pod nazwą NUMMI. Zakład General Motors we Fremont był zdecydowanie najgorszym i najnędzniejszym spośród wszystkich zakładów koncernu – i prawdopodobnie najgorszym w całych Stanach Zjednoczonych. Ostatecznie zamknięto go w 1982 r. Kiedy ponownie otwarto go w 1984 r. wspólnie z Toyotą, szybko stał się nie tylko najlepszym zakładem General Motors – również jakość i wydajność produkcji osiągnęła poziom porównywalny z zakładami w Japonii, mimo że zatrudniono tu w większości byłych pracowników zamkniętego wcześniej zakładu General Motors.
NUMMI GM Toyota
Wówczas była to wielka szansa dla General Motors. Firma miała w ramach inwestycji joint venture zakład, który doskonale sprawdził się w szczupłej produkcji. Cieszyła się ona poparciem pracowników, kierownictwo znało koncepcję kultury szczupłej produkcji i wiele osób wiedziało, jak skutecznie ją wdrożyć. Kiedy inne przedsiębiorstwa chcą przejść na szczupłą produkcję, jednym z głównych problemów jest zawsze pytanie o to, skąd wziąć dużą grupę osób obeznanych z tą koncepcją. General Motors miało to podane na tacy. Nie musieli się jej uczyć od podstaw, wystarczyło przekazać ją pozostałym zakładom. I właśnie w tym punkcie totalnie pokpili sprawę.
Stosowanie gróźb i przymusu w celu wdrożenia szczupłej produkcji
Koncern General Motors postanowił wprowadzać szczupłą produkcję etapami, co samo w sobie jest mądrym posunięciem. Do wdrożenia koncepcji wybrano dwa zakłady – w Van Nuys niedaleko Los Angeles i w Norwood w Cincinnati. Rozsądnym podejściem byłoby tu rozpoczęcie od kilku małych projektów w obrębie tych zakładów, mających na celu otwarcie pracowników na szczupłą produkcję i budowanie ich motywacji za pomocą historii sukcesu. W ten sposób stworzona zostałaby podstawa propagowania koncepcji w całym zakładzie.
Jednak kierownictwo General Motors miało lepszy pomysł na motywowanie pracowników. Niech rywalizują ze sobą na śmierć i życie! Tak, dobrze zrozumiałeś. Chcieli pojedynku, który tylko jeden zakład mógł przetrwać. Zarządzili zawody w szczupłej produkcji, w których zwycięzca mógł nadal istnieć, podczas gdy przegrany miał zostać zamknięty. Aby zmusić pracowników do przejścia na stosowanie szczupłej produkcji, posłużyli się wobec nich groźbą utraty pracy. Oczywiście od początku pracownicy obu zakładów byli wysoce nieufni wobec szczupłej produkcji, a nie zmotywowani, by przekonać się do tej koncepcji. Ciekawe, dlaczego…
Stosowanie szczupłej produkcji do redukcji zatrudnienia
Tak więc zwycięzca nie zostanie zamknięty. Ale dla General Motors nie oznaczało to, że wszyscy pracownicy zostaną. Celem była redukcja zatrudnienia o 25 proc.! Dlatego pracownicy General Motors mieli wybór między zamknięciem zakładu i zwolnieniem wszystkich, a zwolnieniem jednej czwartej kadry. Naprawdę atrakcyjna alternatywa.
Zwracali się więc do pracowników z prośbą o pomoc, polegającą na dobrowolnym odejściu z pracy. Nie dziwi więc fakt, że pracownicy nie byli chętni oraz że nasilała się niechęć wobec szczupłej produkcji. Związki zawodowe nazywały szczupłą produkcję „najniebezpieczniejszym systemem, jaki kiedykolwiek stworzono w General Motors w celu zburzenia jedności między pracownikami”.
Prawdopodobnie jednak najważniejszym czynnikiem porażki General Motors był brak uwagi ze strony kierownictwa najwyższego szczebla. Kierownictwo Toyoty wykazuje nieustanne zainteresowanie wszystkimi szczegółami, chcąc naprawdę zrozumieć działanie wszystkich procesów w firmie. Oczywiście jako kierownik nie możesz zagłębiać się w każdy szczegół, ale Toyota skupiała się na dokładniejszym zgłębieniu kilku przykładów, podczas gdy menedżerowie General Motors zainteresowani byli raczej płytką, a jednocześnie szeroką perspektywą. Kierownictwo wolało pobieżny pięciominutowy obchód niż poświęcenie danej sytuacji odpowiedniej ilości czasu. Koncern General Motors szukał metod i narzędzi, ale umknęła mu szersza perspektywa.
Zabiegi General Motors można porównać z ubieraniem pracowników w kimona i udawaniem, że od teraz są Japończykami. Koncepcja Lean to o wiele więcej niż tylko narzędzia. Używając innego przykładu – zakup najlepszych dostępnych na rynku farb i pędzli nie zrobi z ciebie Michała Anioła. Kierownictwo General Motors tego nie zrozumiało. Kierownik Toyoty powiedział, że General Motors rozumie proces „w zakresie sprzętu i organizacji przestrzeni zakładu. Obawiam się jednak, że kierownictwo najwyższego szczebla General Motors nie rozumie podstawowej koncepcji”.
Przekazywanie koncepcji dalej
General Motors zawsze poszukiwało panaceum, które mogłoby być następnie przekazane dalej. W firmie istniały osoby dobrze zaznajomione ze szczupłą produkcją za pośrednictwem zakładu NUMMI, jednak nie były one w stanie zapoczątkować procesu przekształcenia w obliczu braku zainteresowania kadry kierowniczej i sprzeciwu pracowników. Ponadto byli oni rozproszeni w małych zespołach lub pojedynczo i stanowili zbyt małą grupę, by móc działać skutecznie, nawet gdyby nie spotkali się ze wspomnianym brakiem zainteresowania i sprzeciwem.
Wyniki konkursu
Zakład w Norwood odrzucał koncepcję szczupłej produkcji już od początku i niewiele się wydarzyło. Pracownicy zakładu w Van Nuys również ją odrzucali, ale kierownictwo wymusiło na nich stosowanie niektórych narzędzi, mimo że rzadko działały one tak, jak powinny. Nie da się wdrożyć szczupłej produkcji przy sprzeciwie pracowników. Co gorsze, ich negatywne nastawienie wpłynęło na inne zakłady i wszystko, co pochodziło z NUMMI, napotykało opór ze strony innych zakładów. Umiejętności nabyte przez pracowników General Motors w NUMMI nie trafiły na podatny grunt, dlatego nie przyniosły rezultatów.
Ponieważ zakład Van Nuys przynajmniej udawał, że coś robi, wypadł lepiej niż zakład w Norwood, który nie podjął żadnych działań w kierunku wdrożenia szczupłej produkcji. Dlatego w 1987 r. zakład w Norwood zamknięto. Jednak obiekt w Van Nuys przetrwał tylko pięć lat dłużej i został zamknięty w 1992 r. W jego miejscu znajduje się teraz centrum handlowe, trafnie nazwane „The Plant” (zakład, fabryka).
Ogólnie rzecz biorąc, niezły bałagan. Szczupła produkcja nie przyjęła się w General Motors. Firma nie tylko nie była w stanie przekazać kultury z NUMMI do innych zakładów, ale napotkała również w nich aktywny opór. Jak często bywa, była to porażka kierownictwa. Na ich obronę wspomnę, że od tamtego czasu podnieśli swoje umiejętności w zakresie szczupłej produkcji, choć nadal polegają one głównie na stosowaniu narzędzi bez większych zmian w sposobie myślenia.
Artykuł ukazał się w nr 6(30) grudzień 2020-styczeń 2021 czasopisma „Production Manager”.
Więcej interesujących treści w naszym najnowszym wydaniu. Dołącz do klubu naszych prenumeratorów ▶ https://www.production-manager.pl/prenumerata/
Zobacz również