ZARZĄDZANIE
Gdy mniej, znaczy więcej
Toyota słynie m.in. ze swojej struktury zespołowej pracowników liniowych. Podczas gdy w wielu zachodnich firmach hierarchia wiąże się z nadmiarem obowiązków, w Toyocie przełożeni mają czas, by pomagać swoim pracownikom i usprawniać działania.
Data publikacji: 29.01.2024
Data aktualizacji: 29.01.2024
Podziel się:
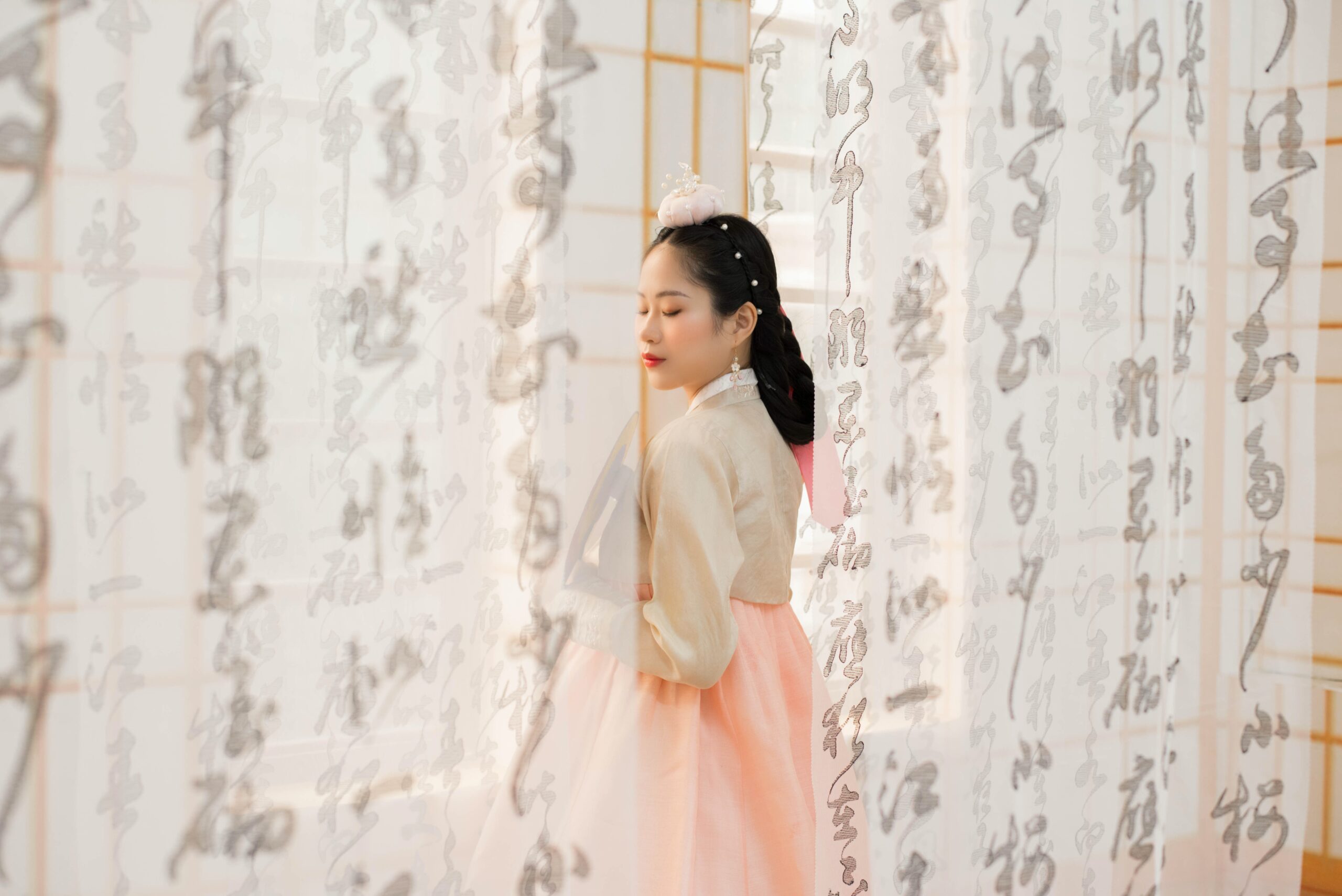
W Toyocie operatorzy liniowi pracują w zespołach składających się z czterech do sześciu operatorów (inne źródła mówią o pięciu do ośmiu, ale moje obserwacje skłaniają się ku mniejszej liczbie). Zespoły są prowadzone przez lidera zespołu, zwanego hancho (班長 – od lidera oddziału, lidera grupy, lidera zespołu), choć obecnie w Toyocie czasami używa się również angielskiego określenia „team leader”. Lider zespołu wywodzi się spośród operatorów i jest bardzo doświadczonym operatorem, który doskonale zna stacje robocze przypisane do danego zespołu. Stanowisko to jest w pewnym sensie etapem przejściowym między poziomem operatorskim a kierowniczym. Lider zespołu nie ma uprawnień do podejmowania działań dyscyplinarnych, a jego praca zwykle obejmuje również działania operacyjne oprócz funkcji kierowniczych. Pracuje on przez 40–60 proc. czasu nad rzeczywistymi zadaniami produkcyjnymi, a pozostały czas poświęca na nadzór.
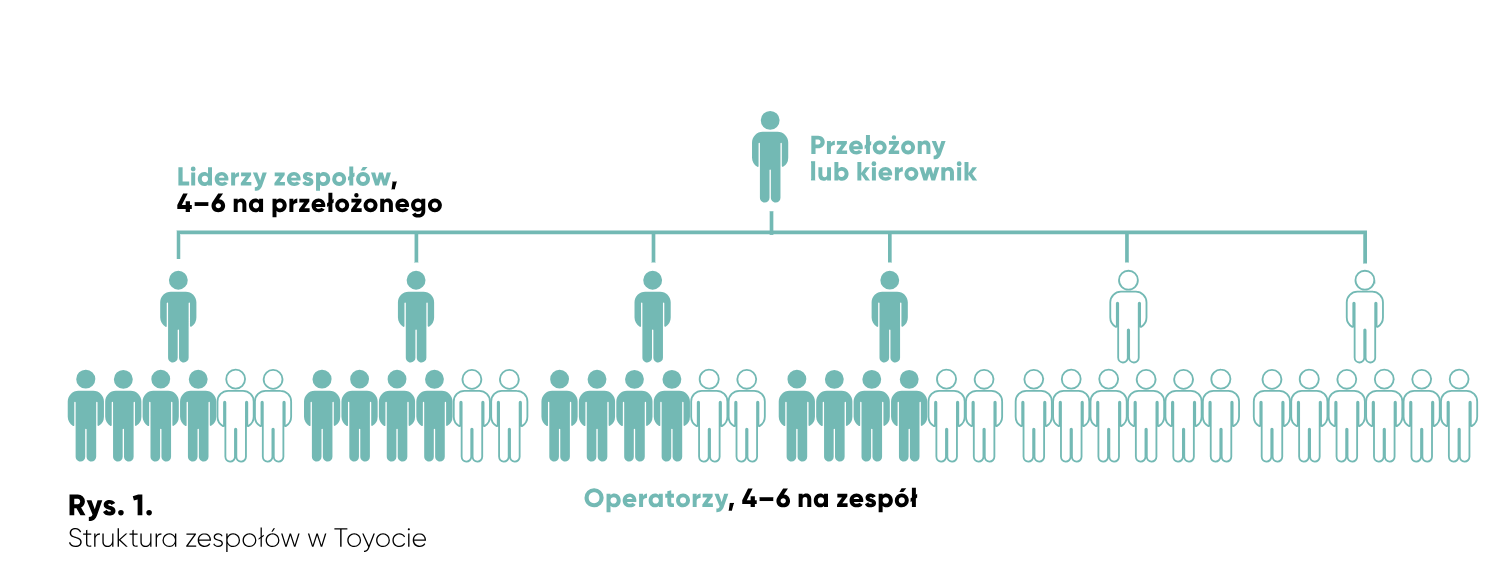
Od problemów do pomysłów
Oprócz pracy produkcyjnej lider zespołu ma za zadanie wspierać operatorów, pomagać w razie problemów, które mogą być oznaczone na linii andon i związane np. z bezpieczeństwem, czasem (pracownik nie nadąża) i jakością (produkt nie jest wystarczająco dobry), choć w Toyocie wadliwy produkt zazwyczaj nie jest dopuszczany do dalszego etapu produkcji, dlatego problem związany z jakością szybko staje się problemem związanym z czasem.
Lider zespołu pomaga w każdym wypadku. W razie poważniejszych problemów niezwłocznie pojawi się wsparcie ze strony przełożonego lub obsługi technicznej. Liderzy zespołów powinni się upewnić, że wszystkie materiały i narzędzia są dostępne i sprawne. Jeśli operator potrzebuje przerwy (np. na skorzystanie z toalety), przejmuje on jego obowiązki.
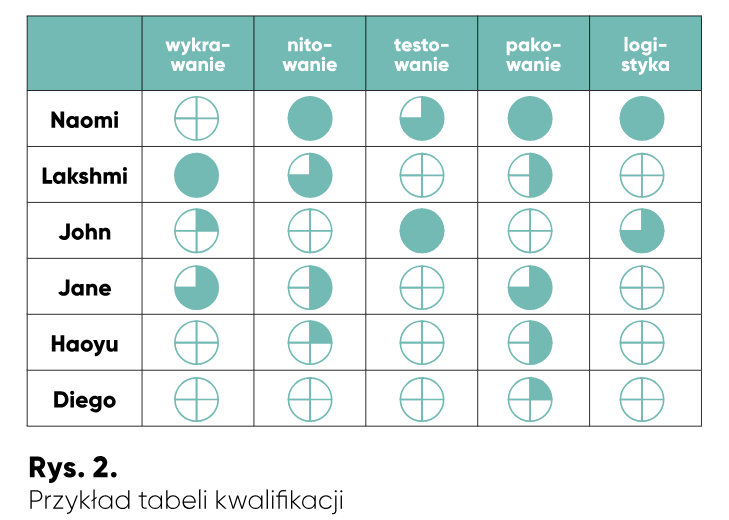
Liderzy zespołów śledzą również kwalifikacje i potrzeby szkoleniowe członków zespołu, m.in. za pomocą tabeli umiejętności lub tabeli kwalifikacji. Są w stanie szkolić operatorów w miejscu pracy, pomagając nowym pracownikom, dopóki nie będą oni w stanie samodzielnie wykonywać pracy. Weryfikują, czy pracownicy przestrzegają obowiązujących standardów i są pierwszymi osobami, z którymi można się kontaktować w celu zgłaszania pomysłów na ulepszenie procesów. Odgrywają również aktywną rolę we wdrażaniu ulepszeń.
Liderzy ułatwiają komunikację wewnątrz zespołu, na wyższych szczeblach oraz z sąsiednimi zespołami, również między zmianami. Śledzą wydajność i przestrzeganie standardów oraz przeprowadzają dwa razy w roku przegląd wydajności operatorów. Są oni również odpowiedzialni za przezbrojenie, jeśli zajdzie taka konieczność (choć większość linii produkcyjnych Toyoty jest na tyle elastyczna, że można na nich przełączać produkcję bez konieczności przezbrojenia).
Nad liderem zespołu znajduje się lider grupy (przełożony lub kierownik, już nie operator), który odpowiada za czterech do sześciu liderów zespołów i ich zespoły. W związku z tym przełożony jest odpowiedzialny za szesnaście do trzydziestu sześciu osób, choć zwykle jest to mniejsza liczba. Średnia wynosi około osiemnastu osób. Należy pamiętać, że nazwy „lider zespołu”, „lider grupy”, „przełożony” itp., są używane i definiowane bardzo różnie w różnych firmach.
Korzyści wynikające ze struktury zespołu
Pytanie brzmi: czy to wszystko jest tego warte? Czy warto zatrudniać dodatkowych pracowników do tworzenia małych zespołów, aby lepiej wspierać pracowników liniowych? Toyota uważa, że tak (i ja się z tym zgadzam). Na szczęście mam potwierdzające to dane. Kilka lat temu odbyłem Grand Tour po japońskiej branży motoryzacyjnej. W ramach tego doświadczenia zmierzyłem procent czasu, w którym pracownik wnosi wartość dodaną na linii montażowej. Zapytałem również niektóre zakłady o stosunek liczby przełożonych do liczby kierowników liniowych.
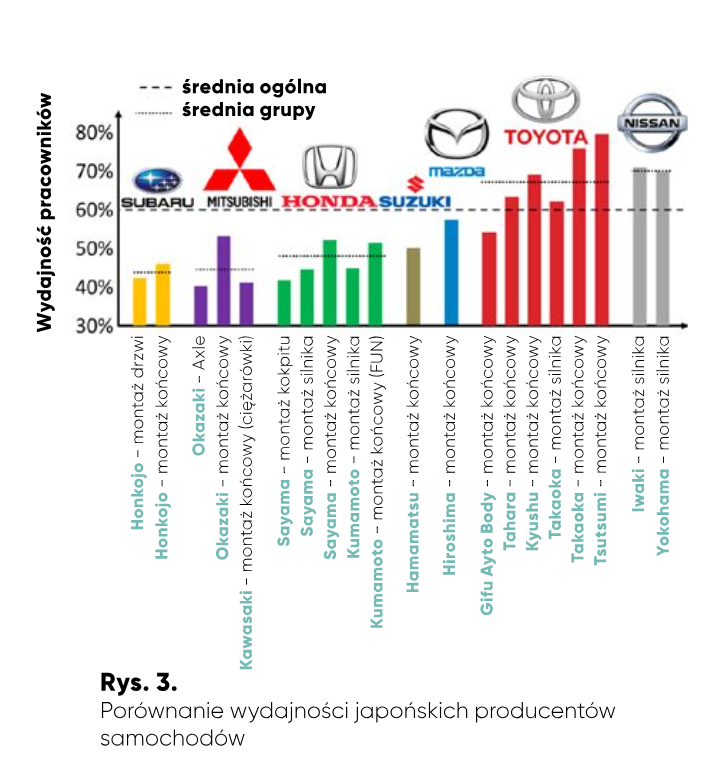
Już wtedy zauważyłem korelację między mniejszymi zespołami a lepszymi wynikami, ale nigdy nie umieściłem tego na wykresie. Poniżej znajduje się zależność procentowej wartości dodanej w odniesieniu do wielkości zespołu w różnych fabrykach samochodów (i jednej fabryce ciężarówek) w Japonii. Dodałem również linię trendu.
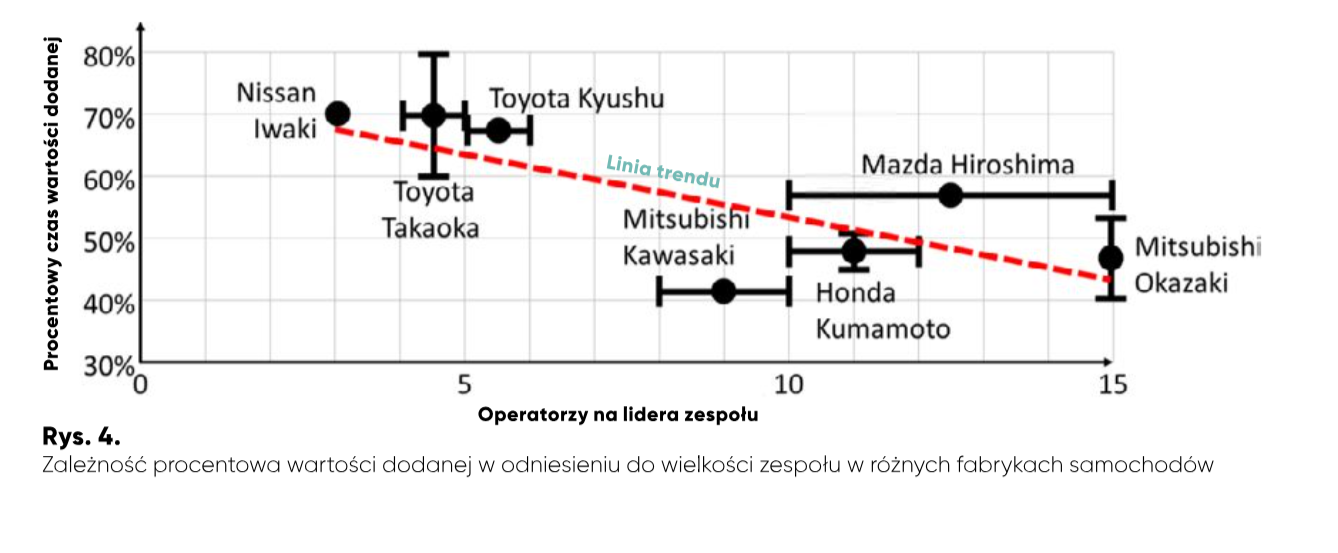
Uwaga! Dane są nieco chaotyczne. Na przykład zmierzyłem tylko jedną linię w Mazda Hiroszima (z wydajnością na poziomie 57 proc.). Mazda wskazała również szeroki zakres od dziesięciu do piętnastu operatorów na lidera zespołu.
Fabryka Mitsubishi w Okazaki poinformowała mnie, że na jednego lidera zespołu przypada piętnastu pracowników, a ja przeprowadziłem pomiary na dwóch liniach – montażu osi na poziomie 40 proc. i montażu końcowego na poziomie 53 proc. Procentowa wartość dodana jest moim przybliżonym szacunkiem, a wielkość zespołu jest zgodna z informacjami przekazanymi przez zakład, stąd obie miary są lekko niepewne. Mimo to istnieje wyraźna korelacja między mniejszymi rozmiarami zespołów a znacznie lepszymi wynikami. Z grubsza rzecz biorąc, każde zmniejszenie zespołu o jedną osobę dodaje około dwóch punktów procentowych wartości dodanej czasu. (Uwaga: nie należy mylić zmniejszania wielkości zespołu ze zwalnianiem pracowników – to coś zupełnie innego).
Kontynuujmy analizę liczb. Jeśli na każdego lidera zespołu przypada piętnastu operatorów, to zespoły liczą szesnaście osób łącznie z liderami zespołów, czyli 6,3 proc. pracowników to liderzy zespołów. Jeśli lider zespołu pracuje produktywnie tylko przez połowę czasu, to 3,1 proc. osób (połowa z 6,3 proc.) wykonuje zadania ogólne, a 96,9 proc. rzeczywiście pracuje nad produktem. Wartość dodana wynosi 44 proc., więc 43 proc. czasu wszystkich pracowników generuje korzyści dla firmy (96,6 proc. pracuje z wydajnością 44 proc.).
Jeśli na każdego lidera zespołu przypada dziesięciu operatorów (tj. zespoły składają się z jedenastu osób, wliczając lidera zespołu), to 9,1 proc. pracowników to liderzy zespołów, czyli 4,5 proc. czasu pracy pracowników to praca ogólna, a 95,5 proc. czasu to praca nad produktem. Jednak procentowa wartość dodana wzrosła do 55 proc., co oznacza, że 52 proc. czasu poświęcanego przez pracowników generuje korzyści dla firmy. Opierając się na tych szacunkach, idealna wielkość zespołu wynosi od dwóch do sześciu osób, podobnie jak w wypadku Toyoty.
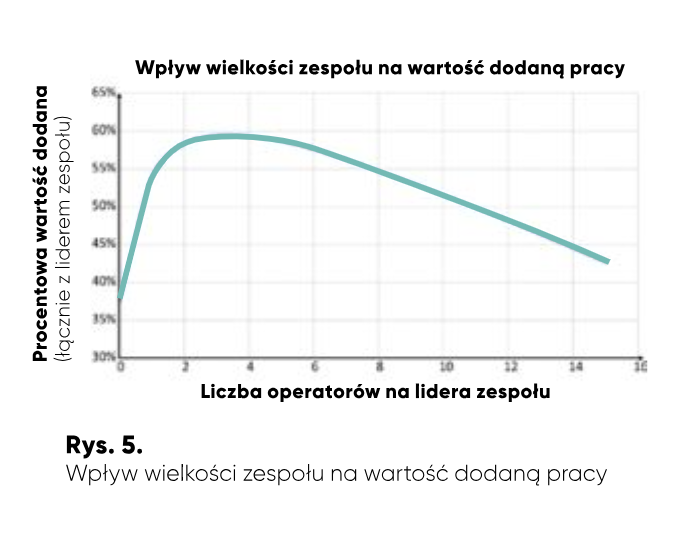
Należy pamiętać, że jest to tylko przybliżony szacunek, z wieloma założeniami. Dane nie są zbyt dokładne (przedział ufności wahałby się w dowolnym kierunku), dokonałem więc liniowej ekstrapolacji poza zakres moich danych (tj. wielkości zespołów poniżej trzech), i założyłem, że lider zespołu zarabia tyle samo co operator i tak dalej. Z drugiej strony – wątpię, by lider piętnastoosobowego zespołu był w stanie pracować nad produktem przez połowę swojego czasu. Ogólnie jednak wydaje się, że warto podjąć wysiłek, aby stworzyć mniejsze zespoły, liczące od dwóch do sześciu operatorów na lidera zespołu. Na marginesie, w projektach zaleca się również, aby wielkość zespołu wynosiła od trzech do sześciu osób, aby uzyskać idealną wydajność.
Dlaczego nie robimy tego na Zachodzie?
Odpowiedzią jest – jak to często bywa w metodyce Lean – księgowość. Koszt przełożonego lub lidera zespołu można zmierzyć bardzo precyzyjnie, ale korzyści są naprawdę trudne do określenia. Jeśli księgowość nie może tego zmierzyć, określa, że wartość ta wynosi zero (tj. lider zespołu nie ma żadnej wartości dla księgowości). W związku z tym, aby poprawić statystyki, liczba liderów zespołów została zmniejszona i często spotykamy się z zespołami liczącymi dwudziestu, trzydziestu, a nawet więcej operatorów na jednego przełożonego lub lidera zespołu.
Oczywiście lider zespołu jest całkowicie przytłoczony pracą i ledwie może wszystkiego dopilnować, nie mówiąc już o zapewnieniu właściwej pomocy swoim operatorom lub wspieraniu ulepszeń. W rezultacie spada wydajność i cierpi na tym cała działalność.
Odwrócenie tej sytuacji jest trudne, ponieważ należałoby zatrudnić liderów zespołów, co wiąże się z kosztami, a osiągnięcie korzyści z mniejszych zespołów zajmuje trochę czasu (kolejny przykład padołu łez zalewającego Lean). Jednak na dłuższą metę będzie to całkiem opłacalne.
Autor: Prof. Christoph Roser
Artykuł ukazał się w nr 3(45) czerwiec-lipiec 2023 czasopisma „Production Manager”.
Więcej interesujących treści w naszym najnowszym wydaniu. Dołącz do klubu naszych prenumeratorów ▶ https://www.production-manager.pl/prenumerata/
Zobacz również